Digital twin prototype
The simulation driven digital twin starts with a clean sheet for a virgin product.
Step 1 – Defining the system and initial dimensioning
Identifying the operational constrictions, bottlenecks and weak points early in the design phase is vital. In this step you can test the response of the product during different scenarios with real time response of parameter changes. Flanked by a 3D CAD model for visualising the spatial geometry and initial dimensioning, the main characteristics of the product can be defined.Step 2 – Virtual testing and optimisation
Critical components or processes of the product are simulated using multi physical 3D models of the product, based on the parameters and CAD from step 1. Such high-fidelity simulations are taking all relevant details into account. Based on the findings, topology, process and performance can be optimised.Step 3 – Calibrating the dynamic system model
Using the optimised product from step 2, a Reduced Order Modelling technique can be used on the high-fidelity simulations and implemented in the dynamic system model from step 1, providing a highly accurate but fast dynamic system model. Having this platform reduces the amount of expensive physical prototypes as the risk of issues arising doing the physical test programs is reduced significantly.Step 4 – Virtual commissioning
The calibrated system model can also be used in the planning of the physical prototype test program and even testing and debugging the PLC on simulated conditions and perform software- (SiL) or hardware-in-the-loop testing, reducing valuable commissioning time.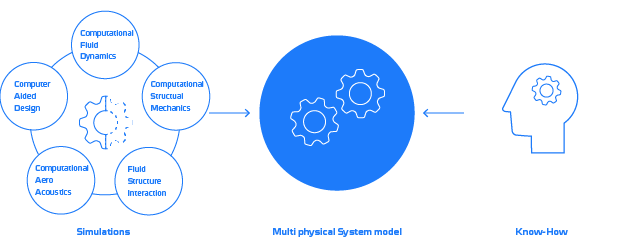
Using the Digital Twin Prototype provides the user with the opportunity to modify parameters and operating conditions of different components and allows to observe the response of the entire system in real time.
Being able to digitally operate an entire system is particularly interesting for product exhibitions and strategy planning. Stakeholders and all relevant team players within a project can benefit from having a quick and simplified understanding of a naturally complex system.
A Digital Twin Prototype is a great way to ease communication between product developers and end users from idea and design phase to commissioning and forms the backbone and platform for the Digital twin coupled to the physical entity through e.g. IoT and live sensor data.