Aerodynamic assesment of vessels
Wind tunnel tests at the design stage can be used to ensure that a vessel meets the operational and class requirements with regard to propulsion, manoeuvring, dynamic positioning, mooring and stability.
FORCE Technology provides a wide variety of services within the field of maritime aerodynamics. Our aerodynamic services provided to the shipbuilding and shipping industry include:
- Analysis of funnel performance - smoke dispersion
- Helicopter operation studies
- Streamline investigation of propeller-induced vibrations
- Wind and current loads
- Anemometer calibration curves
- Wind comfort studies
- Flow field measurements and visualisations
In addition to the above, we also carry out R&D projects, e.g. reducing wind resistance on ships, funnel optimisation etc.
Analysis of funnel performance
A vessel or ship can be subject to unfavourable wind conditions when at sea. It is essential for the operator that the vessel is operational at all times. Adverse wind conditions can severely decrease the funnel performance leaving passenger decks, outdoor working areas or ventilation inlets engulfed in smoke.
Ship designers and owners face a major challenge to ensure that smoke nuisance on such outdoor areas is minimised, thus enabling the passengers to safely enjoy their stay or for the crew to work without experiencing the discomfort of smoke or noxious gases, e.g. SO2 and NOX near ventilation inlets. The latter – if exceeding given exposure limits – can cause severe health problems and cause shutdown of the vessel in periods of operation.
Helicopter operation investigations
A large number of vessels are equipped with a helicopter landing deck or helicopter operation zones (e.g. winching zones). The helicopter landing deck and operation zones can be used for commercial, exploration or safety purposes. Especially for safety purposes, a permanent serviceability even under difficult and adverse wind and sea states is of paramount importance.
Testing a model vessel in a wind tunnel experiment at an early stage of the design is an ideal tool to explore potential risks concerning helicopter operations.
Streamline investigation of propeller-induced vibrations
Reliable estimates of flow streamlines and wake fields on vessels are very important, especially in cases where noise and vibration have been encountered during trials. For evaluation of adverse streamline or wake fields, FORCE Technology uses the wind tunnel as a supplement to CFD calculations, streamline tests and wake field measurements in the towing tank.
By utilising our high-speed wind tunnel, we are able to operate at favourably high Reynolds numbers which enables the tests to be carried out yielding very accurate results. In addition, model modifications in the wind tunnel are very rapid and easy compared with towing tank models, thereby facilitating rapid optimisation.
The method has been proven by successful implementation of the proposed modifications on several full-scale vessels. Further, this method is fast and very cost-effective compared to other approaches.
Wind and current loads
All vessels will be subject to considerable wind and current forces during operations which affect the operational requirements, stability, manoeuvring and propulsion, just to mention a few; factors which must all be analysed in the initial design phase to ensure a cost-effective vessel.
Wind tunnel tests at the design stage can be used to ensure that the vessel meets the operational and class requirements with regard to propulsion, manoeuvring, dynamic positioning, mooring and stability. The thruster units can be dimensioned to handle harbour manoeuvring up to a certain wind speed as and dynamic positioning units can be dimensioned to a certain combination of wind and current speeds.
To determine the environmental loads the vessel will experience, the above-water part of the model is exposed to a wind profile which resembles an ocean wind with regard to velocity distribution and turbulence intensity, while the underwater part is exposed to a uniform wind profile with low turbulence intensity to resemble a vertical current profile.
Further, a key point in the interpretation of results of sea trials is to take the wind component into consideration. This may be done on the basis of wind load coefficients based on wind tunnel tests.
Anemometer calibration curves
Any anemometer installed on a vessel will be subject to the local flow field. By testing a model of the vessel in the wind tunnel, the ratio between the relative wind direction and wind speed to the undisturbed true wind direction and wind speed can be determined and presented in terms of anemometer calibration curves. Having accurate data on the wind speed and direction is important in terms of both helicopter operation, harbour manoeuvring and dynamic positioning situations. Furthermore, the anemometer calibration curves can be used during sea trials to correct for the wind resistance.
Wind comfort
Open recreational areas on cruise vessels, ferries and yachts are often subject to strong wind due to the wind speed at sea and the wind speed created by the ships’ forward motion. The same applies to outdoor working areas on service vessels, drill ships etc. These environmental conditions typically reduce passenger comfort or sets expensive limitations to the working time. Thus it is important to take the wind comfort into account in the design stage of the vessel.
To meet the comfort criteria, it is essential to produce reliable data on the implications that the local gust winds will have on the actual design of the recreational or working areas.
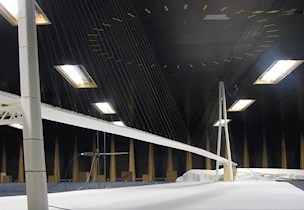
Facility
In-house wind tunnel facility
Related services
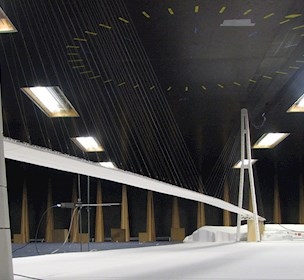
Model tests to ensure optimum bridge aerodynamics.
/Service
We carry out model tests to ensure optimum bridge aerodynamics.
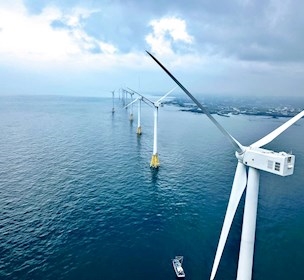
Offshore aerodynamics
/Service
We perform wind tunnel studies for the offshore industry on numerous types of offshore structures.
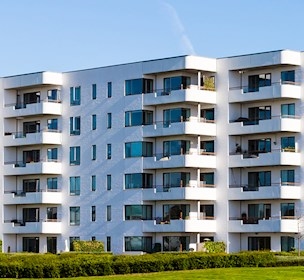
Building aerodynamics
/Service
We test the wind environment surrounding a structure or site to ensure that it is optimised.