Revolutionizing subsea inspection of cathodic protection
FiGS® technology offers non-contact, comprehensive assessments, enhancing maintenance efficiency and extending the lifespan of CP systems.
Ensuring the longevity and integrity of underwater structures can deliver a significant return on investment when done properly. Cathodic Protection (CP) systems have been the cornerstone in preventing the corrosion of metal on subsea installations, from pipelines to templates, manifolds, jackets and Xmas trees. However, advancements in technology are setting the stage for transformative changes in how these structures are monitored and maintained.
At the forefront of this change is the FiGS® system, a non-contact field gradient sensor developed by FORCE Technology. This innovative sensor marks a significant improvement over traditional CP assessment methods by offering detailed insights without the need for direct contact of a structure – whether the structure is buried or not. FiGS® technology can evaluate the effectiveness of sacrificial anodes by mapping the electric fields, including strength and direction, set up by the CP system. This allows for a comprehensive assessment of anode conditions, detection of coating damages, and estimation of the remaining lifespan of CP systems.
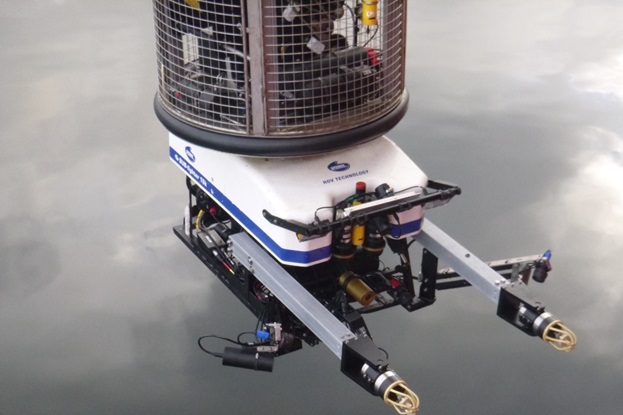
Changing the CP inspection paradigm
Traditionally, CP surveys require stabbing/contact measurement operations to measure the potential of sub-merged structures directly. What sets FiGS® apart is its versatility and ease of integration. The sensor can be mounted on both remotely operated vehicles (ROVs) and autonomous underwater vehicles (AUVs), making it suitable for inspecting a wide range of subsea structures across the oil, gas, and renewable energy sectors.
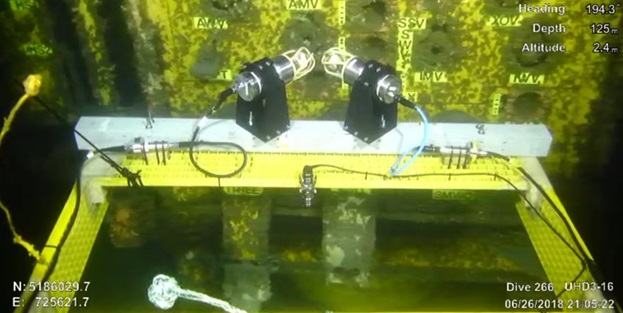
A further paradigm shift comes from FiGS® ability to form the cornerstone of proactive Integrity Management for the subsea assets of entire developments (or even groups of them). Operators can use the detailed insights from FiGS® surveys to predict potential failures and plan maintenance activities before critical failures occur. This holistic and predictive approach helps in extending the life of the assets and in scheduling interventions that minimize downtime and associated costs, while maximizing the efficiency of maintenance resources across large sites.
Unique Selling Points of FiGS® Technology
Because FiGS® offers non-contact measurements that require no direct contact with structures or anodes, the system minimises the risk of physical damage and shortens both preparation and execution times. It delivers comprehensive data on the CP system’s performance, including potential issues such as under-protection or excessive anode consumption. This detailed information aids in proactive maintenance and precise life expectancy assessments.
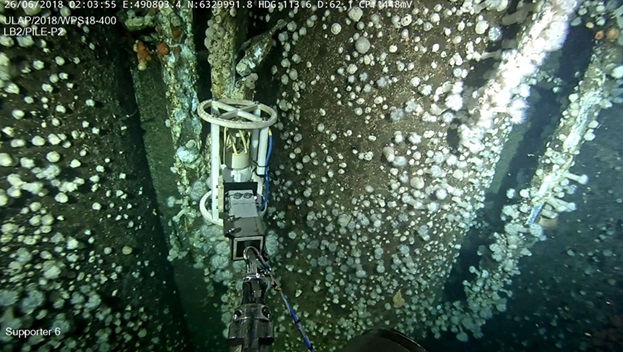
FiGS® enhances operational efficiency by enabling faster and more accurate inspections, which reduces the time vessels need to spend offshore and decreases environmental impacts. This results in lower operational costs and improved safety. FiGS®’ capacity for fast, precise inspections with extended data not only prolongs the lifespan of CP systems but also complies with safety standards, thus reducing the risks associated with subsea operations. Embracing such technologies is key to optimising offshore maintenance and as proof, major operators all over the world have already adopted it as their standard tool for Subsea Integrity Management.