ANDT services are essential to secure pipeline integrity in Southeast Asia
Pipelines in Southeast Asia face unique challenges, requiring advanced inspection techniques to maintain safety and integrity.
Pipelines represent a vital part of the energy infrastructure and FORCE Technology works closely with energy companies and marine contractors to contribute to their integrity and reduce the risk of accidents. We deploy a diverse array of technology and workflows as part of our Advanced Non-Destructive Testing (NDT) services, which are performed by our own personnel and trusted expert partners.
In Southeast Asia, where the energy sector is rapidly expanding and the demands on infrastructure continue to grow, advanced inspection services are essential. By leveraging the technologies and services described below and more, FORCE Technology helps ensure that pipelines remain safe, reliable, and fit for purpose, supporting the region’s energy needs while minimising environmental risks.
Pipeline ovality and custom inspection tools
Ensuring the geometrical integrity of pipelines is critical, especially in regions like Southeast Asia, where offshore and onshore infrastructure faces unique environmental challenges. Our pipeline ovality services provide unprecedented accuracy in assessing the geometry of pipelines, whether for routine inspections or in response to potential damage.
We offer both off-the-shelf and custom-built inspection tools, tailored precisely to meet the specific needs of our clients. Bespoke scanner solutions are designed to adapt to a variety of pipeline geometries and can be positioned on pre-mounted guideposts for precise deployment. With capabilities extending to depths of 3000 meters and applicable to pipelines ranging from 2” to 46” in diameter, our technology is ideal for Southeast Asia's diverse and often challenging operational environments.
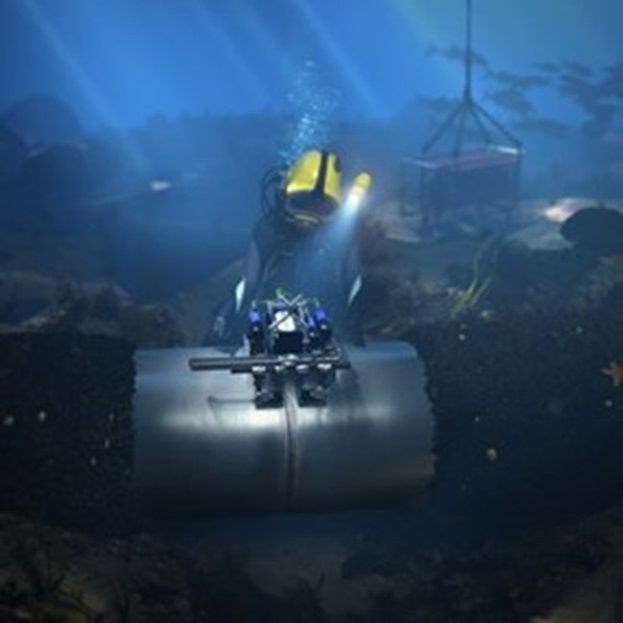
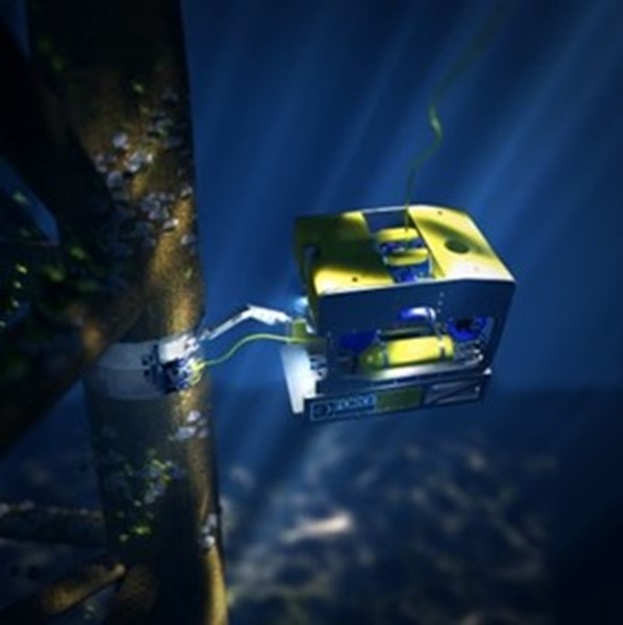
Corrosion mapping for complex geometries
Corrosion is a significant threat to the integrity of pipelines, particularly in Southeast Asia’s harsh marine and industrial environments. Our corrosion and erosion mapping services utilise advanced techniques such as conventional shearwave technology, Time of Flight Diffraction (ToFD), and Phased Array to detect and quantify corrosion in pipelines, bends, and other complex geometries.
Whether using off-the-shelf solutions or custom-designed scanners, we ensure thorough coverage and accurate assessments, helping operators maintain the safety and functionality of their critical infrastructure.
Advanced weld inspection for subsea applications
Weld integrity is another crucial aspect of maintaining pipeline safety, and our advanced weld inspection services are designed to meet the highest standards in the industry. Using our modular and flexible system, we can adapt to a wide range of geometries, allowing access to areas that were previously difficult or impossible to inspect.
Our latest phased array technology, deployed through the P-Scan 5 subsea inspection system, not only increases the speed and efficiency of inspections but also significantly improves data quality. The high-resolution digital outputs allow for detailed 3D simulations and modelling, paving the way for the integration of artificial intelligence (AI) and machine learning (ML) in data interpretation. This cutting-edge approach reduces subsea operation time and enhances the ability to detect structural weaknesses that might otherwise go unnoticed.
Contact us today to access our ANDT services for your subsea infrastructure
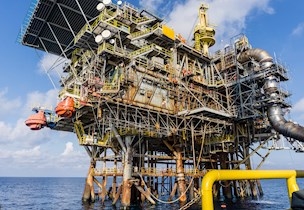
Ensuring safe offshore pipeline operations in Thailand
/Article
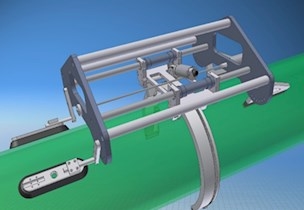
Pipeline integrity management & ANDT services
/Article
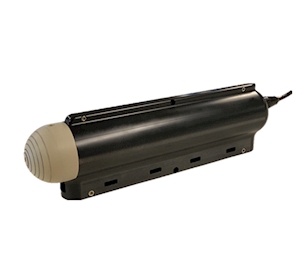
Ensuring subsea integrity with FIGS in deep waters
/Article
FORCE Technology's FIGS and ROVs ensure subsea integrity with advanced cathodic protection.
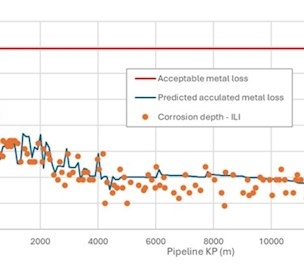
Pipeline integrity management with CorPos-ADMT & ANDT
/Article
Enhance pipeline integrity management with CorPos-ADTM & ANDT. Learn more today!
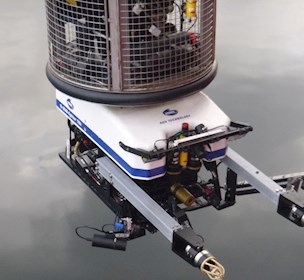
Revolutionizing subsea inspection of CP systems
/Article
FiGS® offers non-contact assessments, boosting maintenance efficiency and extending CP systems' lifespan.