Retrofitting a new bulbous bow
The challenges for today’s shipowners are both regulatory and financial. The regulatory matters are difficult to affect, but the financial matters can be addressed.
One way of addressing the financial challenge is by reducing the cost of the ship in operation. The fuel cost for a merchant ship is between 30% - 70% of the total cost including capital costs, so being able to save fuel really improves the financial result.
The easiest way to save fuel is to reduce speed, and as a consequence, slow-steaming has become popular for shipowners over the past few years. Traditionally, ships have been designed and optimised with one single design point in focus (often a full load draught and high speed) and often have excellent performance at this point. As many ships are now operating off their design point, this can result in relatively poor performance; especially ships with bulbous bows are sensitive to operation at 'off design' conditions. So the fuel cost savings from slow-steaming might not be as large as they potentially could be, but this can to some extent be corrected by introducing a static trim.
FORCE Technology has carried out numerous studies on optimising a new bulbous bow based on the ship’s operational profile. All have been retrofit studies where a section of the bow is cut off and replaced with a new one. Examples of such studies is Maersk Line, who recently exchanged the bow on five 4,500 TEU vessels and five 8,500 vessels.
The easiest way to save fuel is to reduce speed, and as a consequence, slow-steaming has become popular for shipowners over the past few years. Traditionally, ships have been designed and optimised with one single design point in focus (often a full load draught and high speed) and often have excellent performance at this point. As many ships are now operating off their design point, this can result in relatively poor performance; especially ships with bulbous bows are sensitive to operation at 'off design' conditions. So the fuel cost savings from slow-steaming might not be as large as they potentially could be, but this can to some extent be corrected by introducing a static trim.
Re-optimising the bulbous bow
Today hull form optimisation for newbuildings has entered a new paradigm which is optimising the hull form for the ship’s operational profile, e.g. a distribution of draughts and speeds. Can an existing vessel benefit from being 're-optimised' to the actual operational profile? The answer is YES, and moreover a fairly good return of investment can be obtained.FORCE Technology has carried out numerous studies on optimising a new bulbous bow based on the ship’s operational profile. All have been retrofit studies where a section of the bow is cut off and replaced with a new one. Examples of such studies is Maersk Line, who recently exchanged the bow on five 4,500 TEU vessels and five 8,500 vessels.
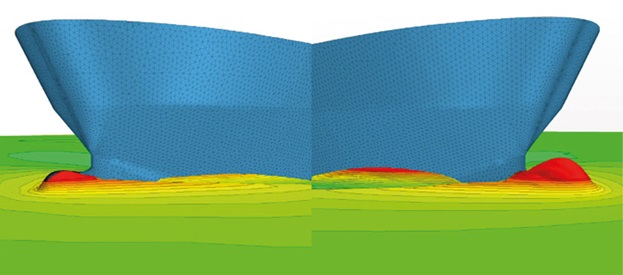
Case study - Clipper G-Class
Retrofitting a bulbous bow is not only interesting for large container vessels. FORCE Technology has also carried out a bulbous bow retrofit study on the Clipper G-Class, a 9,100 dwt multipurpose heavy lift container vessel. This vessel has originally been optimised for 7.5 m draught and a speed of 16 knots, but the operational profile shows that the vessel often operates at lighter draughts (~6.1 m) and slow-steam (~12.5 knots).The new bulbous bow is optimised for two speeds and two draughts where each combination of speed and draught is selected and weighted according to the operational profile. The new bulbous bow is designed utilizing parametric hull form optimisation by the FRIENDSHIP Framework. This framework is coupled with the advanced RANS CFD code STAR-CCM+ for evaluation of the resistance and an optimisation routine searching for lowest weighted resistance.
The weighted total resistance saving is 11.7%. It should be noted that for the deepest draught and highest speed (close to the original design point) of the operational profile, the resistance is actually increased by 2.5%, but the vessel rarely operates at this condition. Further, it should be mentioned that the performance of the original bulbous bow can be improved by trimming, and the new bulbous bow is less sensitive to trimming.
In addition to the optimisation services, FORCE Technology can provide a complete design package for a new bulbous bow including drawings for class approval and detailed construction drawings. The design package is made in cooperation with an acknowledged design firm and the client.
”Estimating the actual gain when modifying the bulbous bow is quite complex as it depends on the future and usually unknown operational profile, i.e. future loading and speed conditions. Further, the savings from the current practice for trim optimization will be reduced somewhat. These are the factors which must be dealt with systematically when considering a bulb modification. However, we have confidence in our final savings estimate, not least due to the proven optimization method used by FORCE Technology." Kjeld Roar Jensen, Clipper Fleet Management / Head of Performance Management