ASIC power management til selvforsynende IoT-sensorer
ASICs til selvforsynende IoT-sensorapplikationer med integreret energy harvesting power management interfaces kan hjælpe os af med batteriskift.
Min IoT-sensors batteri er løbet tør… igen…
Internet of Things er ved at være et godt brugt begreb, og spådommene om hvor mange millioner eller milliarder enheder, der kommer på nettet, kan være svære at forholde sig til. Gartner Says ”6.4 Billion Connected “Things” Will Be in Use in 2016, Up 30 Percent from 2015,” men ét er sikkert – at der ligger et stadigt stort potentiale i at instrumentere omverdenen med trådløse sensorer til et væld af applikationer og få ”ting på nettet”. Alt fra home automation og alarmsystemer, intelligent tøj og fitness trackere til industriel monitorering og herigennem optimering.En stor barriere for at realisere ovenstående er batterier. Hvis vi kan undgå batterier, vil udrulningen gå meget stærkere, da et batteriskift – fx i en trådløs termostat – bliver en stor barriere, når man har 10 af dem. De løber tør på skift, og varmen buldrer derudaf ude af kontrol, indtil man får batterierne skiftet.
Energy harvesting til energi selvforsynende sensorer
Én løsning er at gøre enhederne selvforsynende med energi. Et energi-autonomt system, der lader sig selv op med energi fra omgivelserne, betyder en servicefri løsning.Afhængigt af omgivelserne kan det dreje sig om energi fra mange kilder såsom lys, bevægelse, varme, magnetiske og elektriske felter. Emnet kaldes energy harvesting og er på flere og fleres læber, men større udbredelse af batteriløse og selvforsynende systemer lader stadig vente på sig.
Designet til IoT sensorer med varierende energikrav
Hvis man vurderer de tilgængelige løsninger og komponenter på energy harvesting markedet, vil man opleve, at der er behov for dybe kompetencer både indenfor fysik og effektelektronik for at komme i gang. Man kan ikke blot smide batteriet ud og indsætte en energihøster som fx en termoelektrisk generator til at høste energi fra varme.
En selvforsynende enhed kræver, at hele IoT-sensorenheden inkl. sensor-, dataprocesserings- og kommunikationsdelen er designet til energy harvesting. Der skal nemlig tages højde for, at energikilden kan variere, og der muligvis ikke altid er energi nok. Samtidig er den elektriske profil af en energy harvesting generator er meget forskellig fra et batteri.
Læs også: Vibrationer forsyner fremtidens IoT-enheder med energi
Power management interfaces til batteriløse IoT apparater
De primære komponenter, det kræver at realisere en selvforsynende løsning, er ikke kun en energy harvesting generator (som fx solcelle, termogenerator, piezoelement), men også et interface til power management, da ingen energy harvesting generator har samme output karakteristik som et batteri.Et power management interface sørger for at konvertere strøm og spænding til et niveau, der kan drive IoT-sensoren, som typisk har et behov, der ligger indenfor for 1,8-5 V. Fx leverer en termogenerator en meget lav udgangsspænding (~20-50 mV DC) ved lave temperaturgradienter, hvorimod en piezoelektrisk generator leverer høje spændinger (~10-100 VAC), når det høster energi fra vibrationer. Samtidig skal impedansen af generatoren matches for at opnå højeste effektivitet, hvilket power management interfacet også tager sig af.
Energy harvesting IC-markedet
Flere IC-producenter har komponenter til energy harvesting markedet og udbyder flere typer power management interfaces til energy harvesting. Disse består af et indgangstrin, som typisk er målrettet en eller to typer generatorer. Mange solcelle IC’er dækker fx også termoelektriske generatorer ved lave gradienter, da deres impedans-match er lignende, og de derfor kan drives på samme måde. Dog er der kompromiser, og mange løsninger har brede specifikationer for at sikre bred anvendelse og høj volumen.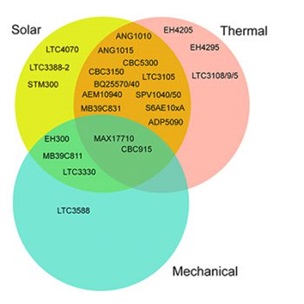
Kold start ved lave spændinger
Om en transistor er i et kendt stadie (høj/lav) afhænger typisk af, om der er spænding på dens gate – altså om den er polariseret. Indtil da kan der sagtens løbe strømme, som er ude af kontrol. Dette gør typisk ikke noget i et elektrisk kredsløb, da det drejer sig om små strømme, men når man har en kilde, der fx kun leverer mikroWatt, så er det vigtigt, at der konstant er styr på lækstrømmene. Derfor kræver mange IC’er et batteri som stabil energikilde for at kunne opretholde deres højeffektive egenskaber, så der konstant er styr på kredsløbet. Hvis der ikke er et konstant energilager, skal der et stort energi-input til, før den igen kan operere. Dette er typisk defineret som et koldstartsscenarie for en energy harvesting IC’er, der opererer uden batteri. Minimum input-strøm ved koldstart er typisk en faktor 10 større end ved operation med fyldt energilager. Se fx figur 2, hvor et eksempel på denne input-karakteristik er vist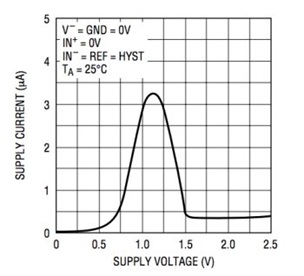
DC/DC erstatter LDO i IoT sensorer
Hvis IoT-sensorens MCU opererer ved en lavere spænding end strømkilden, benyttes ofte en LDO til at levere den rette spænding. Men jo højere spændingsforskellen mellem kilde og forbruger er, jo højere er tabet i LDO’en. Et typisk lithiumbatteri leverer 3 V eller 3,7 V, hvor en MCU typiske forsynes af 2 V. Derfor giver det i mange tilfælde mening at benytte en DC/DC-converter, der sørger for at minimere dette tab, hvilket kan være op til 40 % mindre end i en LDO.One-size IC passer ikke alle
At mange IC’er forsøger at dække bredt over flere energy harvesting generatorteknologier, gør det lettere at finde en IC, der kan fungere, men svært at optimere. Der er typisk sparsomt med energi tilstede, og en høj effektivitet er derfor vigtig. Endnu vigtigere er dog prisen på en IC. Ekstra funktionalitet, der ikke bruges i en IC, er spild af silicium, hvilket resulterer i en højere pris end nødvendigt. Derfor løber mange IoT-sensorudviklere hovedet mod en prismur, når Bill of Materials skal stilles op for en selvforsynende løsning. Hvis generatoren koster et par dollar, og energy harvesting IC’en oveni koster endnu mere, er der lige pludselig langt til den ene dollar, som fx et knapcellebatteri koster.Skræddersyet chip til selvforsynende IoT-sensors
I høj volumen, >100.000 IoT-sensorer, giver det mening at evaluere skræddersyede IC’er (ASIC) til at integrere ellers diskrete løsninger. En ASIC kan favne både energy harvesting power management interface, sensor interface, processor og kommunikationsinterface i samme chip, hvilket realiserer et såkaldt System-on-Chip. Herved optimerer man brugen af silicium og derved stykprisen. Man kan holde lækstrømmene i bund og operere højeffektivt, og man kan miniaturisere sin IoT-sensor til meget færre komponenter. Ved at samle systemet i én chip kan man også sikre energibevidst operation. Det vil sige, at på baggrund af hvor meget energi der er tilstede, kan IoT-sensoren justere, hvor meget den laver.
I scenarier, hvor den samlede selvforsynende IoT-sensor løsning kommer ned i en pris af et par dollar og fylder mindre end en tændstikæske, bliver det relevant at tale om den store udbredelse af IoT-sensorer. Niveauer såsom temperatur, fugtighed, vibration på fx en produktionslinje kan pludselig monitoreres pr. meter, alarm og sikkerhedssystemer kan monitorere alle døre og vinduer, og indeklimaet i en bygning kan blive styret gennem en matrix af målepunkter i stedet for en enkelt føler, der sidder lige ved siden af radiatoren. Mulighederne er mange, og det er let at komme på de første ideer til potentielle selvforsynende koncepter. Når først IoT-sensoren bliver fri af batteriet, er der ”næsten” ingen grænser for, hvor den kan optimere vores hverdag.
FORCE Technology arbejder til dagligt med IoT-sensorer og energy harvesting i mange forskellige industrier og udvikler ASIC IP til energy harvesting. FORCE Technology driver projektet ”Batteriløs og selvforsynende elektronik”, som er en del af GTS-resultatkontrakten med Styrelsen for Forskning og Uddannelse. Aktiviteterne vejledes af repræsentanter fra den danske industri og har til formål at fremme danske virksomheders udnyttelse af de teknologiske og forretningsmæssige muligheder i energy harvesting.
Relateret indhold
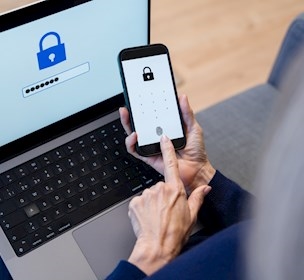
Cyber Resilience Act: nye krav til cyberrobusthed
/Artikel
EU indfører nye krav til produkter, processer og dokumentation. Få overblik over reglerne her.
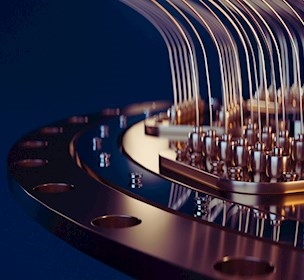
Kvanteteknologi - Status i Danmark
/Artikel
Kvanteteknologi har en stor strategisk betydning for global sikkerhed og innovation.
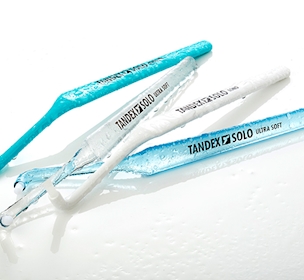
Automatiseret kontrol af kvalitet frigør hænder
/Case
Kamerateknologi effektiviserer produktionen og øger konkurrenceevnen hos TANDEX.