ASIC power management for self-powered IoT sensors
ASICs for self-powered IoT sensor applications with integrated energy harvesting power management interfaces can help us end the need to replace batteries.
My IoT sensor’s battery is dead …. again ….
The Internet of Things is becoming a well-used term, and the prediction about how many millions or billions of devices that will be connected to the net can be difficult to comprehend. Gartner says, '6.4 Billion Connected “Things” Will Be in Use in 2016, Up 30 Percent from 2015;' but one thing is certain – there is still major potential in installing instruments globally using wireless sensors for a wealth of applications and for creating the “internet of things.” Everything from automation and alarm systems in the home, smart clothing and fitness trackers, to industrial monitoring and subsequent optimisation.A major barrier to realising this is the battery. If we can avoid using batteries, the rollout will be much stronger, since replacing batteries – e.g.in a wireless thermostat controlling the heat in your home - becomes a major barrier when you have 10 of them. The batteries will run out of power at different intervals, and the heating will be out of control until the batteries are replaced.
Self-powered sensors utilising energy-harvesting
One solution is to make the devices self-powered. A self-powered system, which charges itself with energy from its surroundings, means a service-free solution.
Depending on the surroundings, energy can be harvested from many sources, such as light, movement, heat, magnetic and electrical fields. Known as energy harvesting, the subject is becoming more widely discussed, but any major distribution of batteryless and self-powered systems is something that still lies in the future.
Read also: Batteryless electronics - energy harvesting
Designed for IoT sensors with varying energy demands
If you assess the available solutions and components for energy harvesting on the market, you will realise that there is a need for both deep competencies in physics and power electronics for it to get underway. It is not as simple as throwing out the battery and inserting an energy harvester; for example such as a thermoelectric generator, which harvests energy from heat.A self-powered device requires that the entire IoT sensor has been designed for energy harvesting – which includes the sensor, data processing and communication part. It must be considered that the energy source may vary and perhaps there will not always be sufficient energy, while the electrical profile of an energy-harvesting generator is very different from a battery.
Power management interfaces for batteryless IoT devices
The primary components for realising a self-powered solution not only require an energy harvesting generator (e.g. a solar cell, thermal generator, piezo element), they also require an interface for power management, as no energy harvesting generator has the same output characteristic as a battery.
A power management interface converts current and voltage to a level that can drive the IoT sensor, which typically requires 1.8–5 V. For example, a thermal generator supplies a very low voltage output (~20–50 mV DC) at low temperature gradients, whereas a piezoelectric generator supplies high voltages (~10–100 VAC) when it harvests energy from vibrations. At the same time, the impedance of the generator must be matched, to achieve the highest efficiency, which the power management interface also deals with.
Read also: Vibrations power tomorrow's IoT devices
The Energy Harvesting IC market
Several IC manufacturers have components for the energy harvesting market and offer several types of power management interfaces for energy harvesting. Their input stage is typically targeted for one or two types of generators. Many solar cell ICs also cover thermoelectric generators with low gradients, since their output profiles are similar, and they therefore can be driven in the same way. However, there are compromises, and many solutions have broad specifications to ensure that there is a wide application range and high volume.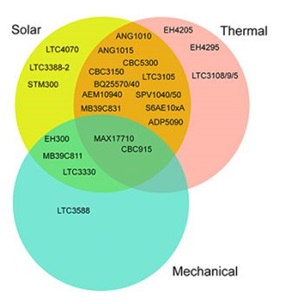
Cold start at low voltages
Whether a transistor is in a known state (high/low) depends typically on whether there is voltage on its gate – in other words, on whether it is polarised or not. Until then, a current out of control can flow. This typically means nothing in an electrical circuit because we are talking about very small currents, but when you have a source that supplies microwatts, it is important that there is constant control of the leakage currents. This means that many ICs require a battery as a stable energy source to be able to maintain their high efficiency properties, maintaining constant control of the circuit. If there is no stable energy store, then a large energy input will be required, before it can operate again. This is typically defined as the cold start scenario for an energy harvesting IC, which operates without a battery. The minimum input current at a cold start is typically a factor of 10 larger than when operating with a full energy storage. For example, see Fig. 2, which shows an example of this input characteristic.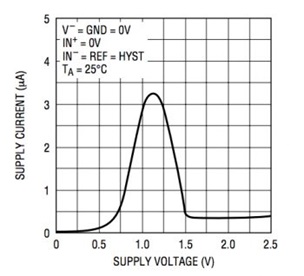
DC/DC replaces LDO in IoT sensors
An LDO is often used to deliver the correct voltage, if the IoT sensor’s MCU operates at a lower voltage than the power source. But the higher the voltage difference between the source and consumer, typically the higher the loss in the LDO.
A typical lithium, battery supplies 3 V or 3.7 V, whereas an MCU perhaps ideally runs on 2 V. In many cases, it therefore makes sense to utilise a DC/DC converter ensuring that this loss is kept to a minimum, which can be up to 40 % less in a DC/DC converter compared to an LDO.
Read also: Hardware evaluation at Donkey Republic
One-size IC does not fit all
Since many ICs attempt to cover a wide range of energy harvesting generator technologies, this means it is easier to find an IC solution that can function, but optimisation is difficult. Typically, the energy available is sparse, and a high efficiency is therefore important. However, the price of an IC is even more important. Extra functionality in an IC, which is not used, is a waste of silicon, resulting in a price higher than necessary.This means that many IoT sensor developers hit a price wall, when the Bill of Materials is made for a self-powered solution. If the generator costs a couple of dollars, and the energy harvesting IC costs even more, there is suddenly a large price difference compared to the less than one-dollar price of a coin cell battery.
ASIC – Custom chip for self-powered IoT sensors
At high volumes, >100,000 IoT sensors, it makes sense to evaluate custom made ICs (ASIC) for integration of discrete solutions. An ASIC can include energy harvesting power management interface, sensor interface, processor and communication interface on the same chip, in other words, a system-on-a-chip (SoC). This optimises the use of silicon and thus the unit price. You can keep the leakage current to a minimum and operate with high efficiency, and you can miniaturise your IoT sensor, with far fewer components. By building a system on a single chip, you can also ensure energy-smart operation. In other words, based on how much energy there is present, the IoT sensor can adjust how much it does.
In scenarios where the complete self-powered IoT sensor solution comes down in price to a couple of dollars and takes up less space than a matchstick, it becomes relevant to talk about the wide distribution of IoT sensors. Levels, such as temperature, humidity, vibration on e.g. a production line can suddenly be measuring per metre; alarm and safety systems can monitor all doors and windows and the indoor climate in a building can be controlled through a matrix of measurement points rather than using a single sensor. There are many possibilities, and it is easy to come up with the first ideas for potential self-powered concepts. Once the IoT has become free of the battery, there is ‘almost’ no limits to what can be optimised in our daily lives.
FORCE Technology works every day with IoT sensors and energy harvesting in many different industries and develops ASIC IP for energy harvesting. FORCE Technology runs the project “Batteryless and self-powered electronics”, which is part of a GTS performance contract with the Danish Agency for Science, Technology and Innovation. The activities are supervised by representatives from Danish industry and their aim is to promote Danish companies’ exploitation of the technological and commercial potential of energy harvesting.