Power IoT devices through harvesting energy from your surroundings
Small wireless battery driven devices for monitoring purposes, such as in air conditioning systems, alarm systems and industrial monitoring systems, are often limited in their functionality and range of application because of limited battery lifetime and subsequent service and maintenance requirements.
Small wireless battery driven devices for monitoring purposes, such as in air conditioning systems, alarm systems and industrial monitoring systems, are often limited in their functionality and range of application because of limited battery lifetime and subsequent service and maintenance requirements.
Solutions meeting the battery life requirements through energy harvesting
Several solutions meet the battery lifetime requirements by instead harvesting energy from the surroundings.
Energy harvesting is about harvesting the energy from the electronic device’s immediate surroundings and extending its lifetime and ultimately, making products that are energy self-sufficient.
A good example of Danish energy harvesting technology is the bicycle light ReeLight, which utilises an electromagnetic generator and the parking disc, Park Solar, which utilises solar cells.
Read also: Powering IoT sensors using ambient energy
New sources of power through kinetic energy
Energy in the surrounding environment is found in many forms, such as light, heat, radio waves, magnetic fields and motion. One of the next fields that has been given greater attention is energy harvesting from vibrations and motion, also known as kinetic energy harvesting – a field that has been researched for many years but which so far, has resulted in only a few commercial applications. This will change in the near future, with maturing energy harvesting technologies and optimised low-power power electronics.
When working with kinetic energy harvesting from motion, motion can be divided into two groups – vibrations and impulses. Vibrations are everywhere around us, when things are set in motion and when resonances arise. These oscillations can drive a mechanical generator, if the frequency matches the resonance frequency of the energy harvesting generator.
Impulses are everywhere around us, e.g. when a simple movement is executed like the closing of a door or when a button is pressed. These movements can cause adjacent materials to oscillate or can cause a bi-stable material to change position.
Read also: Batteryless electronics - energy harvesting
Harvesting kinetic energy
When energy from vibrations is to be harvested, an energy harvesting device is designed to match the frequency which the surroundings are vibrating with. For example, it may be the vibrations in a concrete structure, which oscillate at 1-2 Hz when traffic drives past, or an industrial machine/motor, which oscillates at 60 Hz. See fig. 1 for examples of different types of vibrations.
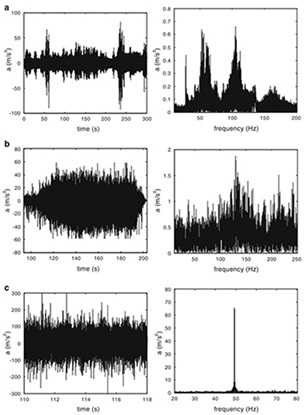
Left column is the acceleration level and the right is the frequency spectrum for:
a) radiator for a car driving on a gravel road
b) tunnel excavation machine
c) concrete casting mould
Ref.: Design and Implementation of Energy Harvesting Powered Wireless Sensor Networks, Vuckovic, D.
Some of the kinetic energy can be converted into electrical energy using different types of energy generators. For example, an electromagnetic generator which converts oscillations to a fluctuating magnetic field, which through coils, generates electrical energy.
As well as piezoelectric material (a ceramic material that consists of piezo crystals), which has the property that when its physical shape is changed, some of the mechanical energy is transformed into electrical energy, which is known as the piezoelectric effect. In addition, electrostatic generators can be used to harvest vibration energy by changing the physical distance between the already positively charged and negatively charged sides of the generator, and thus change the voltage potential.
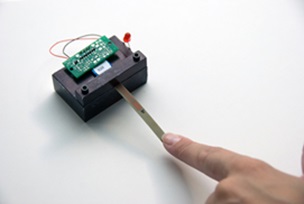
Piezoelectric generator.
The reason why there are many more solutions using solar cells than kinetic energy generators today is because of energy density and complexity, especially when connecting the generator and mechanical movement, and when connecting electronics to the generator. As fig. 1 with the three examples from the vibrating environment shows, both the acceleration level and frequency oscillate and differ, which requires differently designed generators.
Narrow bandwidth of kinetic energy limits diverse applications
The bandwidth of kinetic energy harvesting generators is often a few Hz, which requires a vibrating environment with a fixed frequency. To create a generator that can cover different environments, several design methods to make a generator with a greater bandwidth is required; either by sacrificing efficiency and lowering the system’s Q factor, or by introducing a magnetic field that affects the generator’s movement. The mechanical design can also be changed to achieve a bi-stable system, which can switch between to states.Ongoing adjustment for variable motion
Rather than design for a large bandwidth, the generator can be tuned to the ongoing specific vibration frequency and this ensures high efficiency. This can be done mechanically with the system’s inertia making the system able to change the resonance frequency, or electronically by changing the load.The disadvantage of mechanical tuning is the increased size and complexity, and the disadvantage of electronic tuning is the increased energy consumption in the electronic power control circuit. A combination of mechanical and electronic tuning exists in the form of a variable magnetic field around the generator.
Power electronics enables energy harvesting in new applications
When energy is harvested from motion, it is critical that the power electronics can handle the variable amounts of energy that are generated. Often there are AC signals, which must be rectified, and with photoelectric generators there are often high voltages with very low current, and with electromagnetic generators it is the opposite, with low voltages and high current. There are a lot of topologies for this purpose, which can either be implemented in analogue components or digitally in a microcontroller. In addition, FORCE Technology has carried out research into the potential of ASICs for piezoelectric generators to ensure a high efficiency and low price of components.With the widespread use of IoT systems and small distributing sensor nodes everywhere, there is an increased need for self-sufficient solutions and at the same time the possibilities increase as the energy consumption of electronics decrease, and in particular as wireless communication requires less and less energy (nanowatt – microwatt). Some of the self-sufficient applications that will appear will be used in particular for monitoring buildings, for transport means and industrial machines and plants. Here, small devices can monitor vibrations, humidity levels, temperature etc., and transmit the data wirelessly, without having to be serviced and change batteries, but just live on the harvested energy from motions and vibrations.
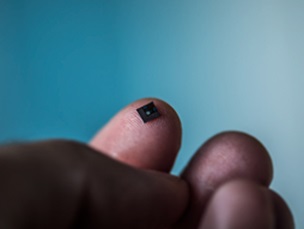
FORCE Technology is carrying out research into the potential of ASICs for energy harvesting, etc.
Every day, FORCE Technology provides consultancy to companies on how to implement new technologies and make their products self-sufficient. This is achieved by carrying out an analysis of the energy present in the surroundings, linked with the technical possibilities, the development and test of prototypes, and microelectronics for the control of energy from energy harvesting generators for energy storage and application.