Sådan optimerer du hærdeprocessen for epoxy – og sikrer kvaliteten af dit produkt
Mange virksomheder oplever kvalitetsudfordringer ved fremstilling af kompositter og coatings. Vi har udviklet en termisk analysemetode, der sikrer optimal epoxyudhærdning og reducerer risikoen for reklamationer og tilbagekaldelse af produkter.
Hærdeprocessens betydning for kvaliteten
Selvom hærdeprocessen ofte udgør en mindre del af produktionen af det færdige produkt, har den en helt afgørende betydning for kvaliteten af det færdige produkt. Det kan derfor godt betale sig, at optimere hærdeprocessen for derved at reducere fx reklamationer og tilbagekaldelse af produkter.
Udfordringen for de fleste virksomheder ligger i, at man mangler viden om processen og de optimale betingelser, herunder hærdetid og -temperatur. Derudover er det vigtigt for virksomheden at kende robustheden i processen ift. afvigelser på blandingsforholdet i flerkomponentsystemer.
En bredt anvendelig analysemetode
For at imødekomme disse problemstillinger, har vi identificeret og evalueret en termisk analysemetode der kan anvendes af virksomheder, der gerne vil optimere deres produktion af hærdende polymerer/plastsystemer, eksempelvis:
- resinsystemer ifm. kompositproduktion
- hærdeplastsystemer ifm. fremstilling af hærdeplast
- coatings - eksempelvis gelcoats, lak og malingssystemer, leading edge protection coatings, o.l.
Som modelhærdesystem er der valgt et kommercielt biobaseret 2-komponent-epoxysystem, der typisk anvendes ifm. vakuuminfusionsprocesser og RTM (resin transfer moulding) ved kompositfremstilling.
For disse fremstillingsprocesser gælder det, at har man styr på sin hærdeproces og kender man de optimale betingelser for temperatur og tid samt hvor meget eller lidt blandingsforholdet må afvige, har man mulighed for at minimere hærdetiden og derved optimere produktionen af det færdige produkt.
Dokumentation overfor kunder
Udover at optimere de interne fremstillingsprocesser kan analysemetoden bruges til, at sikre en ensartet kvalitet ved produktionen. Samtidig kan metoden anvendes som udgangskontrol, og implementeres i virksomhedens kvalitetssystem. Det betyder færre kasserede emner og derved en mere effektiv produktion.
Ved at anvende analysemetoden kan virksomheden sikre, at udhærdningsgraden overholdes og at produktet eller komponenten derfor har de specificerede egenskaber, som beskrevet i databladet fra leverandøren af epoxykomponenter. Dette kan være med til at give virksomheden en konkurrencefordel på markedet.
Komponenter af denne type anvendes ofte i kritiske og store konstruktioner fx i vindmøller, hvor havari og skader jævnligt ses. Her giver analysemetoden mulighed for, sammen med andre test, at placere og dokumentere skylden for en skade eller et havari, da man kan få svar på om komponenten eller enheden levede op til de specificerede krav til ophærdning og dermed de mekaniske og termiske egenskaber.
Hvad kan analysemetoden DSC anvendes til?
DSC (Differential Scanning Calorimetry) er en termisk analysemetode, hvor varmestrømning (heat flow) til og fra en prøve måles som funktion af temperatur eller tid, mens prøven udsættes for et kontrolleret temperaturprogram i en kontrolleret atmosfære.
Metoden benyttes fx til at bestemme et materiales glasovergangstemperatur (Tg), krystallisationstemperatur (Tc) ved køling og smeltetemperatur (Tm) ved opvarmning. Temperaturerne er karakteristiske for specifikke plast/resinsystemer, så resultaterne kan også bruges i kvalitetsmæssige sammenhænge og fx til at identificere ukendte/afvigende materialer.
DSC til evaluering af hærdningsprocesser
DSC kan bruges til evaluering af udhærdningshastigheden og udhærdningsgraden af et hærdesystem (fx et epoxysystem). Metoden kan bruges til at få en bedre forståelse af hærdesystemet hvorved produktionstiden (hærdetiden) for kompositten/hærdeplasten/coatingen kan minimeres, og som et værktøj der kan bruges til vurdering af den optimale udhærdningstemperatur i forhold til materialets (termiske/mekaniske) egenskaber. Herudover kan metoden bruges til at vurdere hvor robust processen er i forhold til afvigelser på blandingsforholdet i flerkomponentsystemer.
Varmeudviklingen der opstår ved udhærdning og glasovergangstemperatur (Tg) er vigtige parametre at kende, for at få en forståelse for hærdningen af epoxysystemet. Tg for en polymer er temperaturen hvor materialet går fra en hård, sprød tilstand til en mere viskøs, gummiagtig tilstand, så det er en materialeparameter der er afgørende for brugstemperaturen. Tg afhænger bl.a. af udhærdningsgraden i et specifikt system, men er også forskellig for forskellige materialer.
Bag om studiet af epoxyhærdning
Som modelsystem er der valgt et kommercielt SUPER SAP INR 2-komponent epoxy system der er anvendeligt til fremstilling af kompositemner ved vakuuminfusion og RTM. Epoxysystemet er indledningsvis hærdet ved 23 oC og efterfølgende efterhærdet ved forskellige temperaturer.
Udhærdningsgraden og hærdehastigheden af SUPER SAP INR SYSTEMet er undersøgt med DSC. Et typisk DSC termogram, der bruges ved evaluering af udhærdningsgraden og hærdehastigheder, er vist i figur 1. Når en epoxy hærder udvikles der varme, man siger også at reaktionen er exoterm (i modsætning en endoterm reaktion hvor der optages varme).
Varmeudviklingen (heat flow) er målt som en funktion af tiden, efter de to komponenter (resin og hærder) er blevet blandet, og er et udtryk for hvor meget epoxy der endnu ikke er hærdet (stort heatflow betyder at der er meget der ikke er hærdet, heatflow=0 betyder fuldt udhærdet). Der er vist fire forskellige grafer efter forskellige hærdetider (3 min, 12 h, 33 h og 100 h) ved rumtemperatur.
Undersøgelsen er udført for at evaluere metoden, og vurdere hvordan et overskud og et underskud af hærder (±5 %) påvirker hærdehastigheden samt udhærdningsgraden. Det er vigtigt at huske på, at dette kun er et modelsystem der kan vise trends, da der ved analyserne bruges meget små prøvemængder på 10-15 mg. For at evaluere effekten af prøvestørrelsen, blev der desuden udført en DSC test på et emne på ca. 200 g, både fra emnets centrum og emnets yderside.
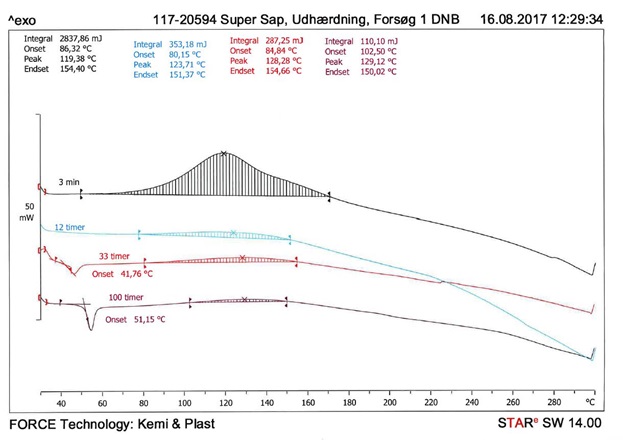
Resultat af studiet
Hærdning ved 23 °C uden efterhærdning
De to epoxykomponenter er blandet i henhold til databladet og hærdet ved 23 °C. Hærdeforløbet (uden efterhærdning) er studeret som funktion af tiden. Derudover er der evalueret prøver med 5 % mere og 5 % mindre hærder end angivet i databladet.
Ud fra DSC-termogrammerne (se eksemplet i figur 1) kan man bestemme Tg. Det observeres at Tg stiger med udhærdningsgraden, hvilket også er forventeligt. Efter 24 timer er Tg ca. 30-40 °C, og efter ca. 100 timer er Tg ca. 50-60 °C.
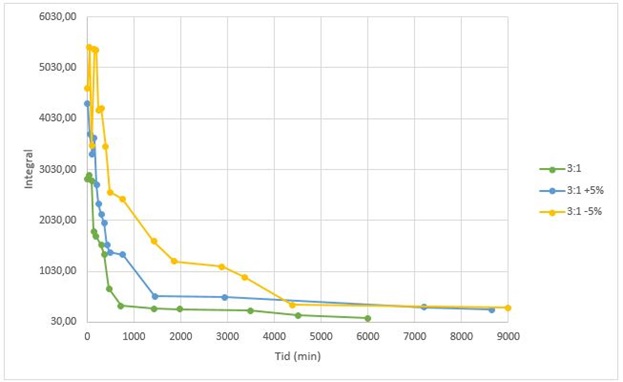
Efterhærdning ved 80, 100 og 120 °C
Til vurdering af Tg som funktion af efterhærdningstemperaturen, er prøverne efterhærdet i 2 timer ved hhv. 80, 100 og 120 °C efter støbning. Producenten anbefaler en efterhærdningstemperatur på 120 °C i 2 timer, og oplyser i databladet, at der ved denne efterhærdningstemperatur opnås et Tg på ca. 105 °C.
Figur 3 viser Tg som funktion af efterhærdningstemperaturen for en prøve på 10-15 mg. Det observeres at Tg bliver højere ved en højere efterhærdningstemperatur. Figur 4 viser Tg som funktion af efterhærdningstemperaturen for en prøve på 200 g, hvor både yderside og centrum er evalueret.
Der observeres ikke den samme effekt ved lille prøvermængde som ved stor prøvemængde, Dette er antageligt grundet forskellighed i reaktionskinetikken ved små og store prøver, primært temperaturforskelle på grund af resinens lave varmeledningsevne.
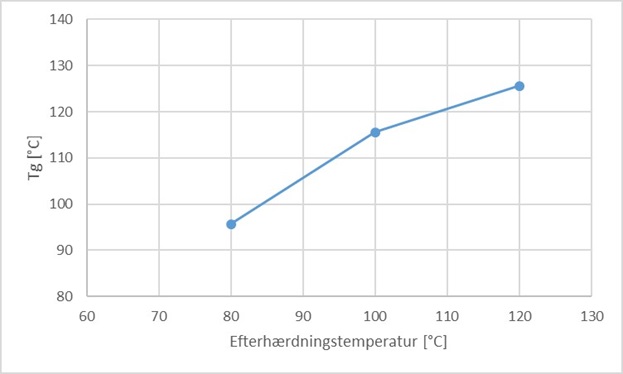
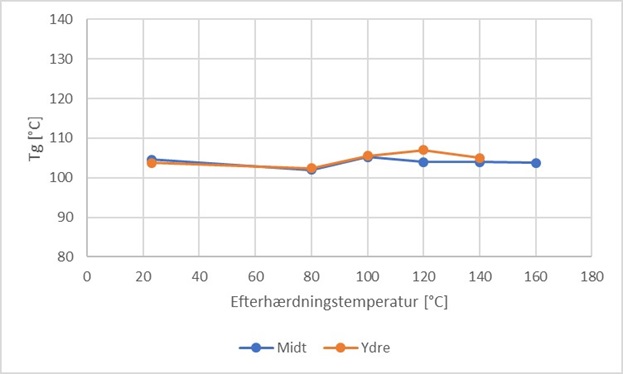
Konklusion
Vi har identificeret og evalueret en termisk analysemetode der kan anvendes bredt ifm. rådgivning af virksomheder der gerne vil optimere deres fremstillingsproces ifm. hærdesystemer. FORCE Technology kan med DSC metoden hjælpe virksomhederne med:
- At identificere et givent plast/resinsystem
- Evaluering af udhærdning samt udhærdningsgrad
- Evaluering af udhærdningshastigheden
- Bestemmelse af Tg
- Hærdeprocessens følsomhed over for afvigelser i blandingsforhold