Brintskørhed i stål - hvad er det?
Brintskørhed er særlig kritisk ved anvendelse af højstyrke stål, og test af fx bolte før installation kan give en god indikation af, om boltene indeholder hydrogen fra fremstillingsprocessen
Hydrogenrevner og brintskørhed
Hydrogenrevner og brintskørhed er begge begreber, som medfører revner i stålmaterialer. Næsten alle, der har kendskab til svejsning, har på et eller andet tidspunkt stiftet bekendtskab med fænomenet hydrogenrevner.
Fænomenet brintskørhed er mindre kendt, men skadesmekanismen er den samme. Hydrogen og brint er det samme grundstof, som under uheldige forhold kan forårsage revner i stålmaterialer. Det er primært stål med høj styrke og materialer med lokal forøget hårdhed, der er de mest følsomme overfor hydrogenrevner og brintskørhed.
Hydrogen er et grundstof, der kan optræde i stål på lige fod med mange andre legeringselementer. Ligheden stopper dog der, da hydrogen oftest er et uønsket element.
Akkumuleret hydrogen reducerer styrken
Hydrogen er grundstof nummer 1 i det periodiske system. Hydrogenatomer er så små, at de har mulighed for at diffundere igennem stål og under visse forhold, kan hydrogen blive fanget/akkumuleret inde i selve stålmaterialet. Afhængig af ståltypen, kan den hydrogen, der bliver inde i stålet, være yderst skadelig for stålmaterialets mekaniske egenskaber.
Akkumulering af hydrogen vil ske langs korngrænserne i materialet og efter noget tid, vil der dannes hulrum pga. det interne tryk, der opstår. Når trykket bliver tilstrækkeligt højt, vil stålmaterialets sejhed og styrke være reduceret i en sådan grad, at der kan opstå et brud. Stålet er blevet mere sprødt, og derfor kaldes det brintskørhed.
Mekanismen er skitseret herunder, hvor de røde pletter skal illustrere brintatomer.
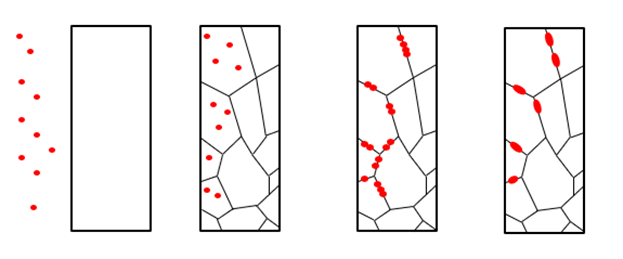
Den bedst kendte kilde til hydrogen i forbindelse med svejsning, er fugt og utilstrækkeligt rengjorte grundmaterialer. Opløsningsgraden af hydrogen er relativ stor i smeltet svejsemetal, men i det øjeblik svejsemetallet størkner, falder opløseligheden, og hydrogen vil akkumulere i svejsemetallet eller diffundere ind i grundmaterialet.
På grund af varmepåvirkningen fra svejsningen, er mikrostrukturen ofte ændret i fusionslinjen og den varmepåvirkede zone. Hydrogen vil typisk samle sig her, hvilket kan forårsage hydrogenrevner. På grund af spændingerne i det størknede svejsemetal, kan hydrogenrevner også ses i tværgående retning i selve svejsemetallet.
Et par eksempler er vist herunder, hvor hydrogenrevnerne er markeret med blå pile. Normalt kræver diffusionsprocessen tid, og det er ikke unormalt, at hydrogenrevner først opstår nogle dage efter, at svejsearbejdet er afsluttet. Dette forklarer også, hvorfor mange fremstillingsstandarder kræver, et der skal gå mellem 24 og 48 timer, før der kan laves ikkedestruktiv kontrol af svejsesømme.
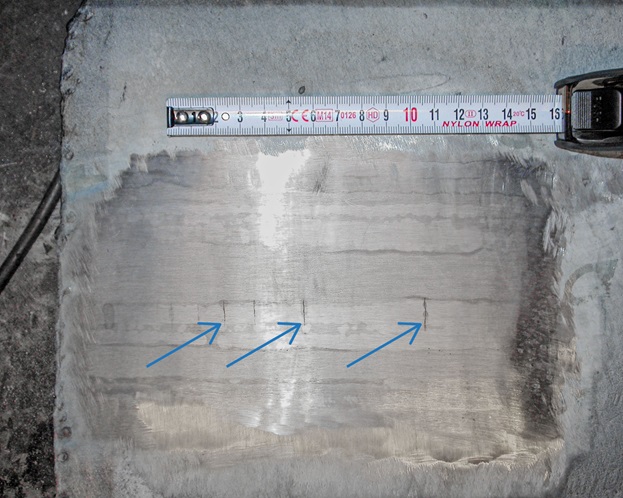
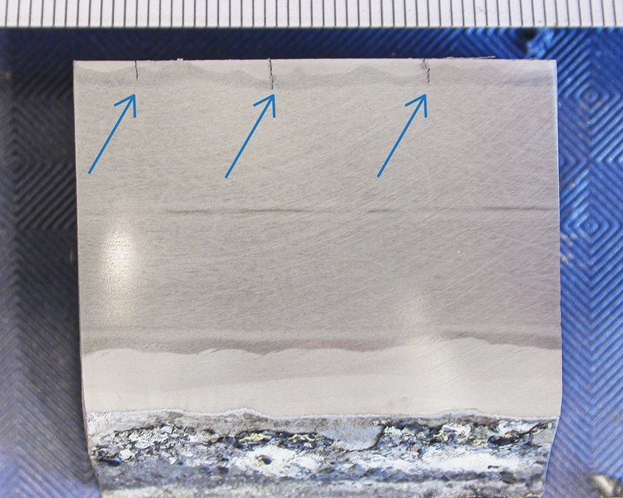
Der findes standarder og litteratur, der beskriver, hvorledes hydrogenrevner kan undgås. Generelt er hydrogenrevner - forårsaget af svejsning - ikke et problem i industrien i dag, pga. kendskab til problematikken.
Hydrogen fra korrosionsprocesser
I sure miljøer, som f.eks. kan opstå i spalter i en samling, eller ved korrosion i havvand, vil der være brintioner tilstede. Disse brintioner vil reagere med frie elektroner fra opløst jern og danne brint på gasform jf. denne reaktionsligning; 2H+ + 2e- -> H2. Brinten vil her også kunne diffundere ind i stålmaterialet, og hvis der er tale om højstyrkestål eller om kolddeformerede stålmaterialer, vil der være en potentiel risiko for initiering og vækst af brintinduceret revnedannelse.
Denne revnedannelse vil fortsætte, så længe der er et korrosivt miljø tilstede, kombineret med tilstrækkeligt store spændinger, og jo større revnen bliver, des større bliver spændingerne i stålmaterialet og dermed revnevæksten. Når revnen når en vis størrelse, vil det sandsynligvis ende med et overbelastningsbrud, som følge af, at tværsnitsarealet gradvist bliver reduceret, i takt med, at revnen vokser.
Typiske eksempler på denne type skade er højstyrkebolte, udsat for havvand eller korrosive miljøer på land. Et eksempel på brud i en højstyrkebolt af styrkeklasse 10.9 kvalitet er vist herunder.
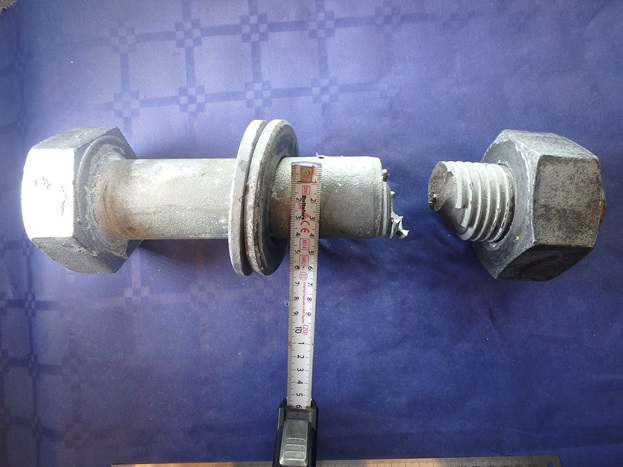
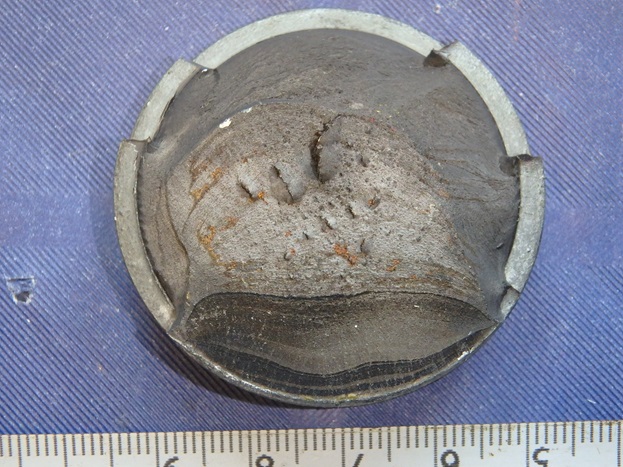
Anvendelse af højstyrke stål kan øge risikoen
Den generelle tendens er, at der i stigende grad anvendes højstyrkestål for at spare vægt og materialer. Følsomheden overfor hydrogeninduceret revnedannelse er en kombination af et korrosivt miljø og en vis styrke – og dermed hårdhed – af materialerne. Hvis man skal lave en konstruktion af højstyrkestål, eller hvor dele af højstyrkestål indgår, er det yderst vigtigt at foretage en granskning af, om der er risiko for hydrogeninduceret revnedannelse.
Ligeledes kan det være nødvendigt at udføre en kontrol af de materialer, der skal anvendes, for at sikre, at den specificerede hårdhed ikke er overskredet. En svejsning vil også typisk give en zone med højere hårdhed, så her er det også vigtigt at have fokus på at kontrollere/reducere hårdheden fra processen.
Hydrogen fra fremstillingsprocesser – delayed fracture
Hydrogen kan også introduceres i et stålmateriale under selve fremstillingsprocessen. Enten fra stålfremstillingen af råmaterialet, eller fra overfladebehandling af en færdig komponent, som f.eks. varmgalvanisering. En typisk kilde til brint kan være afsyringsprocesser, som ofte anvendes til rengøring af stålemner før overfladebehandling.
Afrensning i f.eks. saltsyre forårsager en ganske kraftig udvikling af hydrogen, som vil diffundere ind og akkumuleres i et stålmateriale. For at undgå den skadelige virkning af det akkumulerede hydrogen, skal stålemnerne varmebehandles (bages) nogle timer ved cirka 200℃. Dette vil typisk indgå i fremstillingsproceduren, hvis der er en tilstrækkelig kvalitetssikring.
Der sker ikke umiddelbart noget ved, at der er akkumuleret hydrogen i et emne, når det ikke er belastet. Det bliver først et problem i det øjeblik, hvor eksempelvis en bolt bliver udsat for trækspændinger. Dette vil medføre diffusion af hydrogenatomer, som vil placere sig i de områder, hvor materialet er hårdest eller fremstår med deformeret mikrostruktur – typisk omkring bolthovedet eller gevind.
Efter en vis tid, og såfremt mængden af hydrogen i materialet kombineret med spændingerne når et kritisk niveau, vil der kunne opstå brud. Dette sker typisk indenfor de første 72 timer efter bolten er påført trækspændinger. Denne brudtype er også kendt som ”delayed fracture”. Et eksempel på brud i en 10.9 bolt, som følge af ovenstående, er vist på næste side.
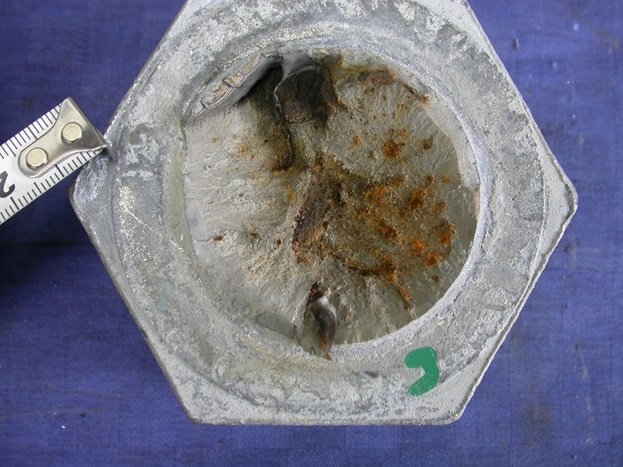
Ifølge standarden ISO 15330, ’Forspændingsprøvning til bestemmelse af brintskørhed’ kan bolte testes før installation.
Dette vil give en indikation af, hvorvidt boltene måtte indeholde hydrogen fra fremstillingen, og derfor med risiko for at knække efter opspænding.
Fotos herunder viser opspændingstest af M48 bolt med et moment på 9500 Nm, hvor bolten bestod testen.
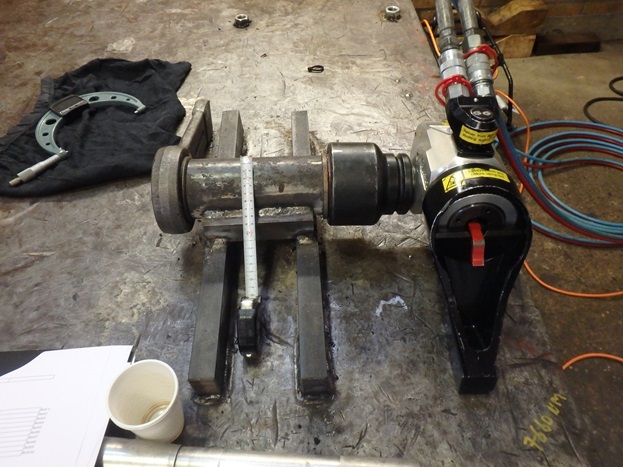
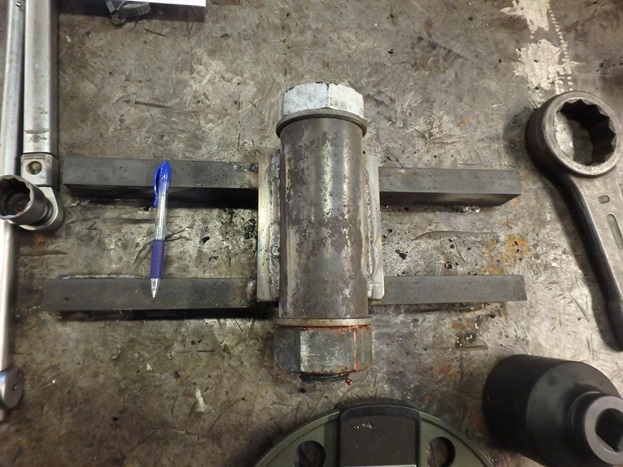