Practical lifetime analysis for solar cell inverters
Can we say something about an electronic product's expected lifetime after a few days of practical testing? Actually, we can – but there are limitations and important distinctions to be made.
In a recently concluded case study, FORCE Technology conducted a "practical lifetime strip-down analysis" on solar cell inverters. This case study is part of Long Live Products and Materials, a project FORCE Technology is carrying out for the Danish Agency for Higher Education and Science.
Is an expensive solar cell inverter worth the price in the long term?
Our aim was to inspect and compare a "cheap" solar cell inverter and an "expensive" one in order to establish a measure of the two products' expected lifetimes.
The inverters were a 2 kW hybrid inverter from GC, based in China, and a 1.5 kW inverter from SMA, based in Germany. Both are single-phase products for use in private households and available on the Danish market. A hybrid inverter has a built-in control system for a battery pack, but the battery pack itself is not included.
The expensive solar cell inverter from SMA (figure 2) costs about four times as much as the cheap one from GC (figure 1) – but does it last four times as long?

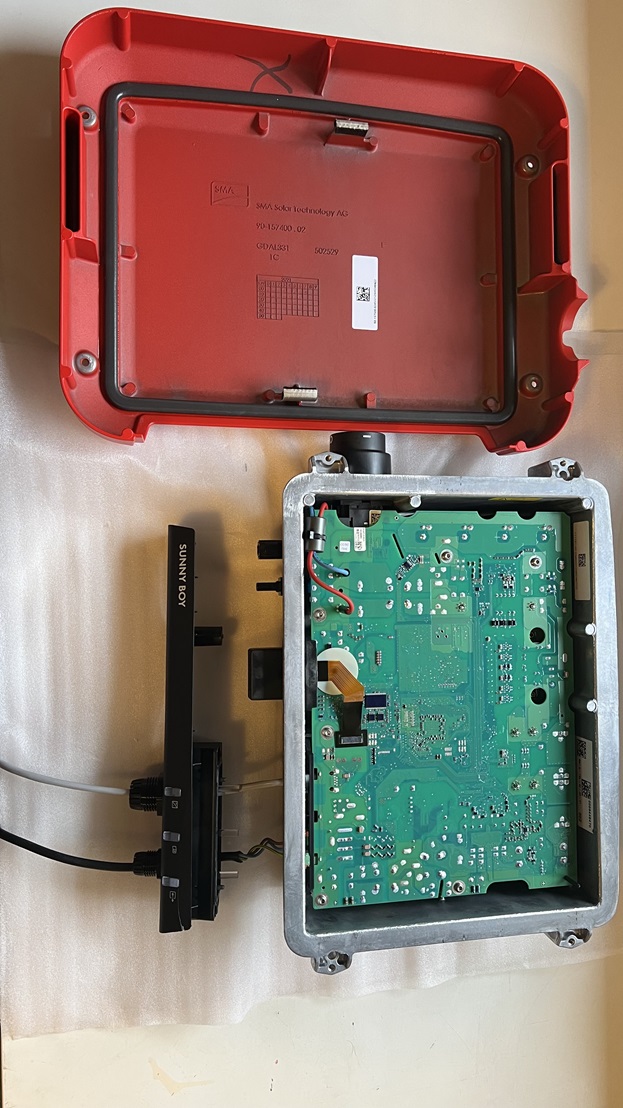
The expensive inverter from SMA, partially disassembled
Three solar cell inverter investigations conducted in a short timespan
Because we sought to conduct our lifetime study in less than one week, there was not enough time for a proper, lifetime test. In view of this, we chose to perform the following three activities:
- A visual inspection
- A rapid HALT test
- A thermographic analysis
Visual inspection
To perform the visual inspection, an experienced reliability specialist disassembled and inspected the two products.
The inspection generated many findings. In terms of product lifetimes, key findings included that the cheap product utilised an open design with at least 20 internal connectors. Meanwhile, the expensive product utilised a closed design with just five internal connectors.
The closed design protects the product from dust and water that could otherwise penetrate it. Because electrical connectors are notorious for reducing reliability, a greater number of internal connectors is associated with a greater risk of problems and reduced lifetime, all else equal.
This type of visual inspection is often conducted as part of a design review. This kind of review requires access to expertise in product reliability and robustness.
Rapid HALT test
The focus of this activity was on thermal and mechanical (vibration and shock) conditions. Consequently, we decided to use a thermo-mechanical rapid HALT as one of the physical tests. This test makes it possible to identify various weak points in a product in a single working day. It also allows us to quantify the margin that the product has relative to the stress it experiences during use. All else equal, a greater margin means a longer lifetime.
Figure 3 shows a condensed summary of the two rapid HALT tests in the form of logarithmic graphs with annotations. The heavy blue stroke on the Y axis indicates the product's specified temperature range, while the heavy red stroke shows temperature margins. The graphs clearly show that the expensive solar cell inverter (from SMA) has wider margins than the cheap one (from GC).
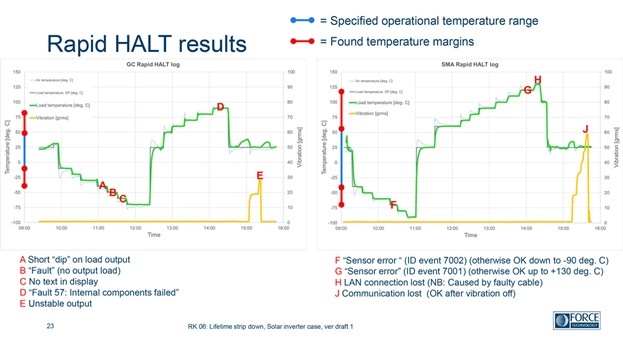
Thermographic analysis
Lastly, we conducted a thermographic analysis. This analysis can quickly provide an overview of the thermal conditions in an electronic product. All else equal, lower operating temperatures result in longer lifetimes for electronic components. A temperature increase in the order of 10–15°C will, on average, halve the lifetime of a product. We must, however, note that thermographic cameras do not necessarily measure temperatures precisely, and there are many pitfalls associated with the use of thermogaphic cameras.
Figure 4 shows a thermogram for the cheap inverter, which reached temperatures of up to +54°C in this operating mode (idle, load of just 60 W).
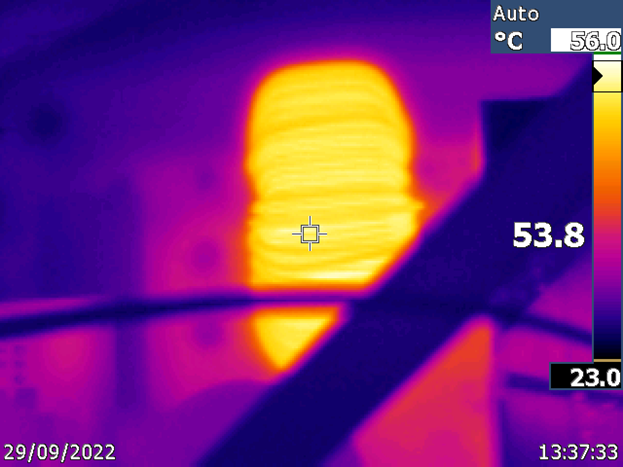
Figure 5 shows a thermogram taken in an operating mode which placed the maximum load on the battery pack. Here, temperatures above +110°C were measured on a power resistor. While the power resistor itself may be able to withstand such a high temperature, this still has an impact on the surrounding components and the PCB.
Unfortunately, it was only possible to operate the expensive inverter in an idle mode, without any real load placed on it. Figure 5 shows a thermogram for this inverter while idle, with temperatures of up to 40°C.
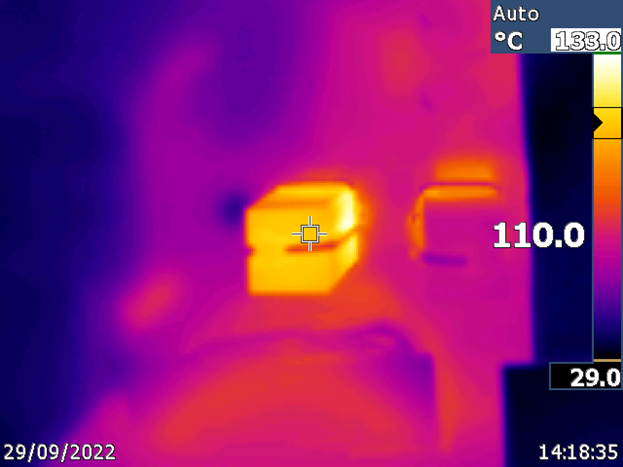
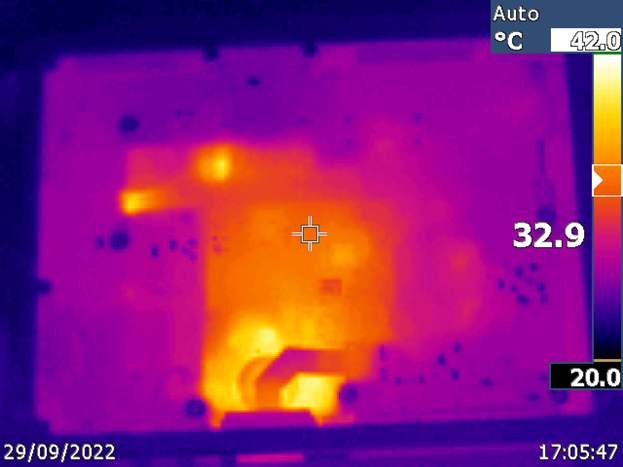
Lifetime analysis conclusions
The three different analyses performed found significant differences in conditions that impact the two products' lifetimes. These differences indicate that the expensive product has the greatest margins, and by extension, a longer expected lifetime.
As it turns out, it is absolutely possible to conduct a qualified comparison of the two products in less than one week. However, this kind of investigation cannot actually quantify a product's expected lifetime. It can only determine that one product appears to be superior to the other.
If a suitable reference from a similar product with known usage is available, it may be possible to calculate an estimated lifetime. In this particular case, an earlier version of a similar SMA inverter has been in use at the writer's home. It has operated without problems for more than 10 years now. All else equal, it would be reasonable to expect the same of the new version.
Lifetime as part of a circular strategy
Products and materials must live longer if we are to reduce our impact on the climate and minimise the consumption of resources. This goes beyond finances to support a circular business strategy.
Long lifetime of products is among the areas that FORCE Technology is focusing on in the performance contract project entitled "Long live products and materials."
Sources: SPM reports 140, 174 and 179.