FORCE Technology's history
From X-ray certification of steam boilers to IoT and digital twins — much has changed since the founding of Svejsecentralen back in 1940.
It all started with two welded steam boilers from Switzerland. They arrived in Denmark 1938 with the permission of the government, as the Swiss manufacturer was able to document that these boilers had been X-rayed and were approved for use. This drew the attention of the Danish industry — why couldn't we certify X-ray boilers in Denmark?
Two years later, on 25 October 1940, Svejsecentralen ["The Welding Centre"] was founded, so FORCE Technology can now call itself an octogenarian. The small business that was founded more than 80 years ago, out of a need to X-ray and certify steam boiler welds, has grown to become a large, multifaceted business. We have 16 areas of business, 1.000 employees, and activities in many countries.
Welding inspection: From X-ray machines to drones
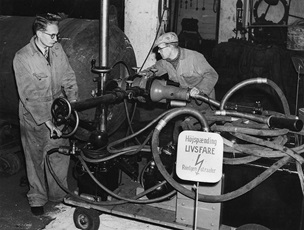
Precision is a prerequisite for technology
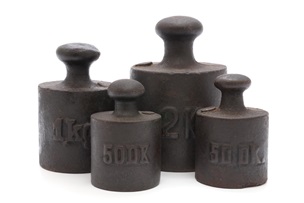
FORCE Technology's Weight and Mass Laboratory was founded in 1951, initially calibrating Danish weights that were directly traceable to the weight in Paris. In fact, we had weights from as far back as the 1600s that were once used by Ole Rømer — the man who first measured the speed of light. Those weights were later donated to an exhibition at Rosenborg Castle. Today, the very same laboratory performs its calibrations digitally and according to the new definition, but with the same goal of ensuring correct measurements and calculations in industry and society.
Many of our 400 other testing facilities have gone on a similar journey. Today, for example, we are developing digital twins: digital copies of real-world objects. This makes it possible to test, optimise, and monitor products and production processes independently of time and place. One of the methods often used to create digital twins is called computational fluid dynamics (CFD). It makes it possible to virtually display flows within and around structures. Among other uses, CFD calculations have been used to optimise the wind conditions around The Blue Planet.
The first transistor radios
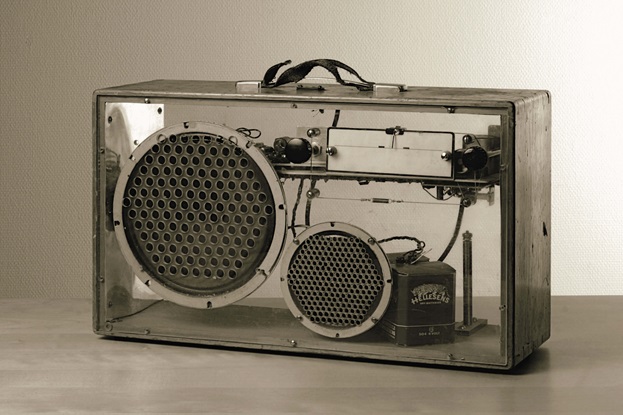
At about the same time as the invention of the transistor, the Technical Acoustics Laboratory was established for the purpose of conducting experiments in technical acoustics in areas like telegraphy and telephony. As technology has progressed, that business area became what is today FORCE Technology SenseLab, which performs some of the most precise audio quality tests in the world.
An airport on Saltholm?
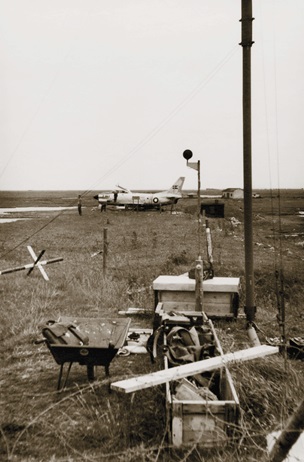
The Royal Danish Air Force supplied a North American F-86 Sabre jet fighter. With its afterburner engaged, it served as a noise source for a comprehensive testing programme conducted from 1964 to 1965. Measurements were taken at 10 locations on the island of Amager over 80 nights, under various weather conditions.
The surprising results revealed that the noise could "skip" along the surface of the water like a stone, meaning that there was significantly less noise attenuation than there would have been over land. The conclusion from these experiments was that a portion of the Amager coast would be subjected to a certain amount of noise from the airport when the wind was easterly, but there would be no significant issues in the residential areas further inland.
As a result, the Danish Parliament decided to build the new airport. Financial issues, however, led to the project's cancellation. The existing airport in Kastrup remained instead. Since then, new technology has made aeroplanes far quieter — fortunately for Amager, which would otherwise be subjected to hellish levels of noise with today's air traffic.
Adventures in oil give way to a green, fossil-free future
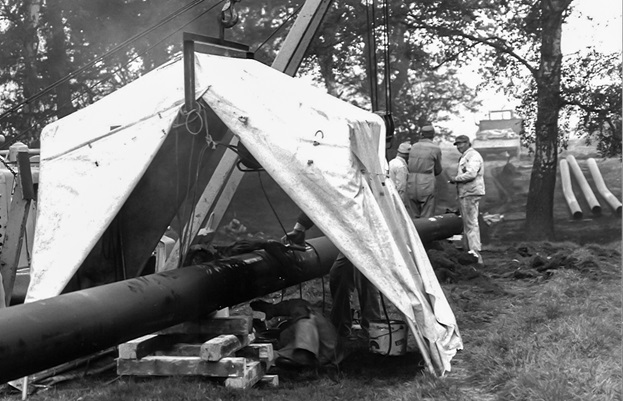
As early as 1957, Svejsecentralen received its first inspection job in the field of oil and gas extraction. That job was performed in Venezuela, but as gas and oil were discovered in the North Sea in the 1960s, those jobs began appearing closer to home. By the time the Danish oil and gas adventure began, Svejsecentralen had already accumulated 15 years of experience in the field.
When the second major oil crisis struck in 1979, it became clear that Denmark, with its relatively high oil consumption and relatively low oil production, would need to find alternatives to oil to meet its energy needs. In the early 1980s, Denmark's natural gas network was established. Svejsecentralen performed X-ray inspections on thousands of kilometres of piping to ensure that there were no cracks or other defects.
Today, FORCE Technology is still a major partner of the energy industry, but its outlook has shifted toward a greener, fossil-free future. As an example, one of our main new areas of focus is power-to-X technologies, which can convert sustainable power into hydrogen via electrolysis, and from there into liquid and gaseous fuels. These can ultimately minimise CO2 emissions by making transportation on land and at sea carbon neutral.
Ultrasound device developed for slaughterhouses offers expecting parents a glimpse of their child
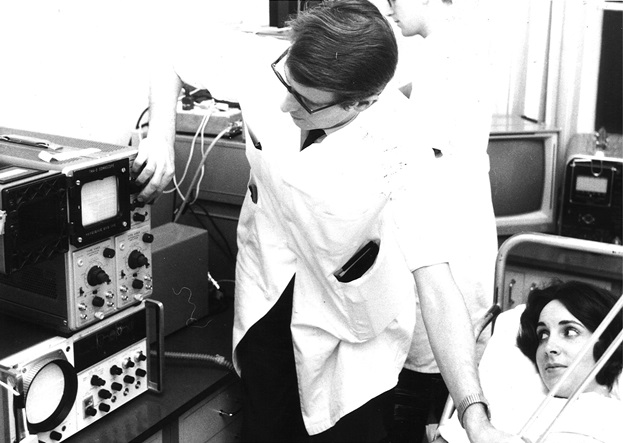
Svejsecentralen's first experiments with ultrasound were hardly major successes, but gradually, the technology improved, and we gained more experience with it. Given the greater precision and safety of ultrasound, it slowly replaced X-ray imaging.
Initially, our primary application for ultrasound inspections was in welding, but starting in 1961, slaughterhouses became a major customer segment, since ultrasound could also be used to measure layers of fat, muscle, and meat in pigs and cows. A physician at Gentofte Hospital read about Svejsecentralen's collaboration with the slaughterhouses and had the idea that it might be possible to scan pregnant woman in roughly the same way. Subsequently, a device was produced for hospital use. The photo shows the very same physician in 1966, inspecting a pregnant woman using ultrasound equipment developed by Svejsecentralen.
As you probably know, ultrasound is still used to scan pregnant women, but it also has many other industrial applications. FORCE Technology, for example, developed P-Scan, an automated ultrasound inspection system used to inspect welds and check for corrosion.
Technology under our skin and in our ears
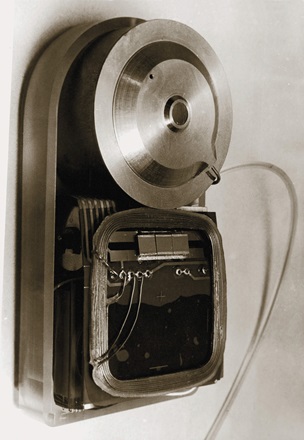
Today, FORCE Technology collaborates with many businesses that produce medical devices. For instance, we test hearing aids. In one year, more than 80% of the world's hearing aid designs were tested at our facilities. Our insight into sensors is also relevant in the healthcare system, which has a growing need for technological solutions. Additionally, our knowledge of standards and compliance is an excellent fit for the medical industry, which is highly regulated.
"Aim for their legs!" they yelled — or did they?
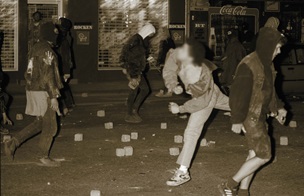
The police fired 113 rounds, and recordings from that dramatic captured an order given by the police. But what was really said? And was it yelled into a megaphone or not? FORCE Technology analysed the audio recordings for investigators with the National Police. Since then, the phrase "aim for their legs" has become synonymous with that evening.
Apart from the recording itself, all the megaphones the police had used were also studied in an anechoic chamber. The conclusion was that the famous phrase was not yelled into a megaphone. This conclusion was later confirmed by the FBI.
Space technology imposes unique requirements on quality and testing
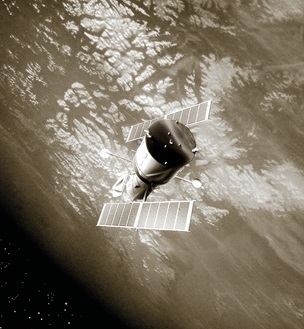
Since the European Space Agency (ESA) was founded in the 1970s, FORCE Technology has been a part of technological developments in space travel. For instance, did you know that ElektronikCentralen, which later became FORCE Technology, supplied the equipment used to expand the Hubble telescope's ten-metre solar panels?
We also participated in the development of rocket nozzles for the Ariane 6 rocket, which is slated to be launched in 2022. Meanwhile, one of our current employees is a young PhD student who is conducting research at NASA's Jet Propulsion Laboratory — the very ones behind the Mars rovers.
Speaking of the Mars rovers, we also had a small hand in Perseverance, which landed on Mars in early February 2021. That rover includes a colour reference that its cameras use to compare and calibrate photographic images. We subjected the colour reference to something known as a pyrotechnic shock test, which shows whether it will survive the violent g-forces that occur during landing. It did.
Microchip triggered tidal wave of new electronics
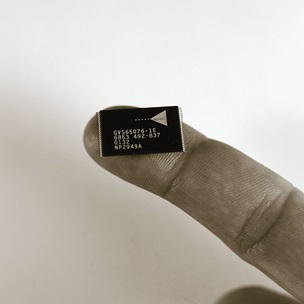
In the 1990s, DELTA (now a part of FORCE Technology) was a leader in microchips. It participated in the development of an ASIC chip that ultimately became a part of the BroBizz electronic toll collection system, used by thousands of drivers every day on the Great Belt Bridge and the Øresund Bridge.
With the introduction of microchips, many more electronic products began filling our homes, workplaces, and societies. As it turns out, these products do not exist independently of each other; they interact and affect each other. Consequently, EMC (electromagnetic compatibility) testing became a major new business area for FORCE Technology.
EMC testing makes it possible to determine whether a product can function together with other electronic equipment. For example, you should be able to turn on your new LED bulb while charging your mobile phone and playing music on your stereo — without annoying noise coming through the speakers, and without causing the charger to stop working.