Composites leave traditional materials behind
Composite longboard, lighter and with superior ride 'feel' compared to competitors, emerged from a case study during a course by FORCE Technology and DTU Wind Energy.
It’s a relatively simple product, which served as a good illustration for the attendees on the course “Hands-on”: Manufacturing and quality control of composite material, and that‘s why the longboard was chosen.
The course was held at DTU Wind Energy as a part of the Industry’s Composite Laboratory. The objective was to provide the attendees with an understanding of designing and manufacturing with composites. The course consisted of both theory and practice, and was structured so that it demonstrated the advantages of using composites as well as some of the challenges to be aware of.
An overwhelming process
When you are not used to working with composites it can be an overwhelming process. Among some of the biggest challenges with composites are material selection (fiber type and resin system), determining the required number of fabric layers and orientation, calculating the strength and stiffness of composite laminates, mold design and production, and the materials and processes associated with the manufacturing of composite parts.To avoid beginner’s mistakes and to get the most performance out of the material, it is a good idea to get help from a professional.
Composites with adjustable properties
Instead of just making a longboard out of composites for the sake of a case study, we wanted to improve upon the boards currently on the market. We believed that this was the best way to demonstrate the benefits of composite materials. One of the advantages with using composites is that it allows for greater flexibility than other materials. This is because the composition of fibres and resin together with the fiber orientation allows for the material properties to be adjusted.The main objective was to reduce weight. This would make the board easier to accelerate and decelerate. This had to be done without affecting the stiffness of the board. The second objective was to maximize the vibration damping, so that the board would be comfortable to ride.
The results were amazing - the stiffness on the prototype was almost the same as available designs, but the weight was reduced by 30%. And that was after our first attempt!
Advanced analysis determines the choice of material early in the design process
The choice of material is the key to success. As a starting point, we compared the materials used in three longboards available on the market: 5-ply maple, bamboo, and 5-ply maple with glassfiber/carbon fiber laminate face sheets. Bamboo and 5-ply with carbon were the two best solutions based on the analysis.To help with the design and material selection, we used a software program called CES selector (produced by GRANTA Design). This tool allows the user to quickly identify the most appropriate materials, or combination of materials, for a certain application.
We knew that a sandwich panel with carbon fiber face sheets and a core material made from foam would produce a light, stiff panel. We then added this material combination into CES Selector and compared it to the existing board designs. We immediately saw a large increase in performance. In CES Selector we could also look at the damping properties of different technical fibers, which showed that flax fiber was 1000 times better at absorbing vibrations than carbon fibers.
Our final design ended up being a hybrid fibre design with carbon fibres and flax fibres in the face sheets. Using CES selector, we were able to identify the right combination of materials and properties in our prototype compared to the current designs already before the first round of testing. The form was drawn in Dassault Systémes CATIA 3D CAD and afterwards produced at Röttger´s Værktøj A/S. After that, the longboard was produced by vacuum infusion, which is a relatively simple and economic method for production of prototypes.
By making calculations on the current products that are made from different materials, a manufacture can speed up the prototype development process, thereby saving time and money.
IKL shall help develop competitive products for the manufacturing industry
Today there is a huge potential in applying composites. But before you get started, it requires qualifications and knowledge regarding the manufacturing process, because it is a special material to work with. If any company wishes to enter this market, it requires the transformation of new materials into competitive products.
To help Danish companies, FORCE Technology has established The Industry’s Composite Laboratory, which is a research- and development project supported by the Ministry of Higher Education and Science.
The objective is to establish a commercial platform that can support the composites industry with all aspects of design, calculation, material technology, production and quality control.
Modified prototype is placed in production
The longboard however is not forgotten. In association with the software producer GRANTA, FORCE Technology has created a webinar with the title: “How to combine materials to optimize performance”, where the longboard is used as a case study to show the whole process.
Furthermore, FORCE Technology has been contacted by an American entrepreneurial company called Community Skate, because they would like to produce a similar skateboard. They would like to replace the carbon fibres with flax fibres, meaning that the percentage of sustainable materials will be even higher.
At present FORCE Technology is working with Community Skate to develop a serial production manufacturing process that maintains the advantages of a light-weight design, while at the same time fulfilling the requirement of sustainable materials.
The article is also published in Plast Panorama no 7 august 2017 (only in Danish)
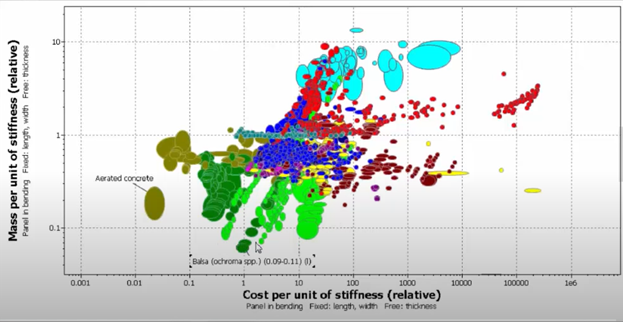
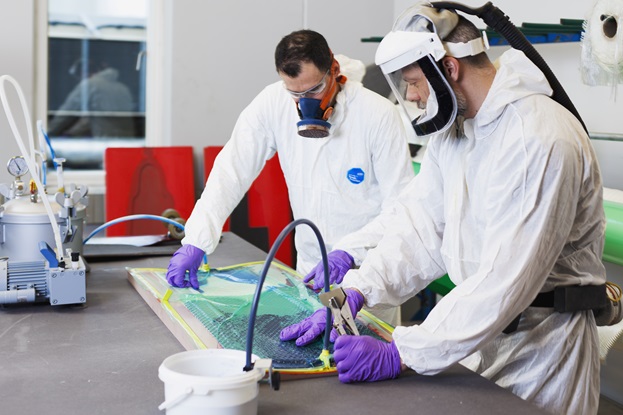
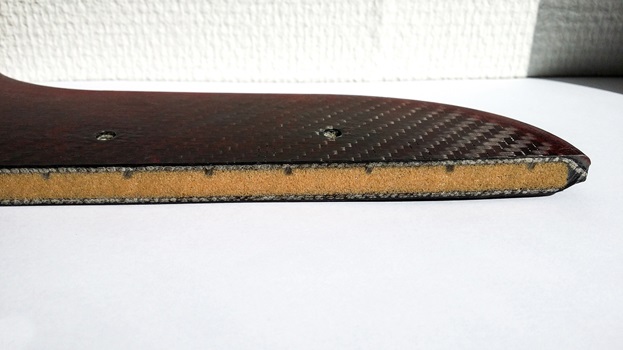
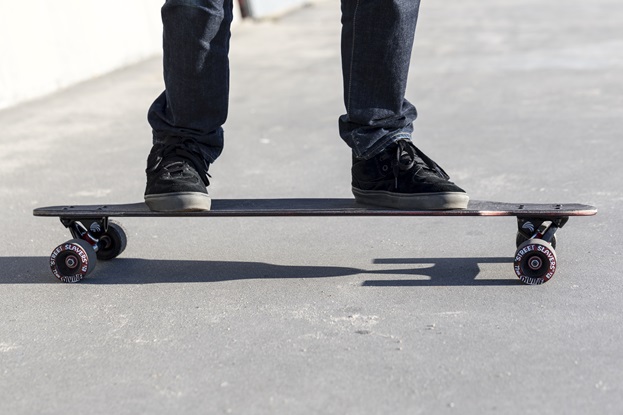
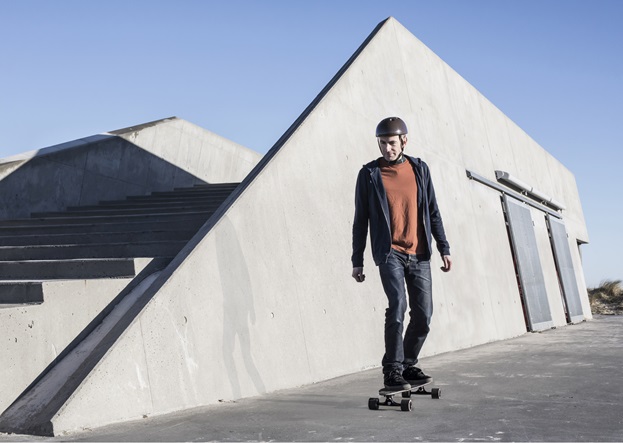