EquiLung provides effective moisture and water protection for electronic devices
EquiLung technology, which can prevent the accumulation of humidity and water, has now been tested in the real world – and the result is a success.
EquiLung prevents water penetration
EquiLung is a bag or balloon that can be installed in a "watertight" device to prevent liquid water and humid air from entering through gaskets, cables and ports.
By "watertight” device, we mean a non-hermetically-sealed device with a high IP rating that prevents water from exiting. In this context, we will focus on the effect on penetration by liquid water.
Temperature changes affect pressure
When a "watertight" device undergoes temperature changes, the pressure inside the device undergoes a corresponding change. At lower temperatures, the pressure inside the device will be lower than that of the surroundings; at higher temperatures, the internal pressure will be higher.
Devices may be rapidly cooled due to such influences as rainy weather, pressure cleaning, and ordinary diurnal temperature changes.
How liquid water and humid air can enter
The pressure drop that occurs when a device is cooled can lead to the following common problems:
- Penetration of liquid water through gaskets, cables and ports. This normally results in large droplets or accumulations of water that slowly disappear when the device is opened.
- Penetration of humid air (containing gaseous water; i.e., water vapour) through gaskets, cables and ports. This normally results in a fine layer of internal condensation that rapidly disappears when the device is opened.
Figure 1 shows the result of a simple test of two "watertight" devices. Here, the devices are represented by two identical cabinets of a type commonly used for electronics. The cabinets were first exposed to constant heat (85°C) for thermal stability, then sprayed with cold water using a handheld spray nozzle for at least 2 minutes.
Before the test, both cabinets had a small connecting piece installed and connected to a hose running down into a glass containing coloured water (red). If the pressure inside a cabinet drops, water will be sucked into the cabinet.
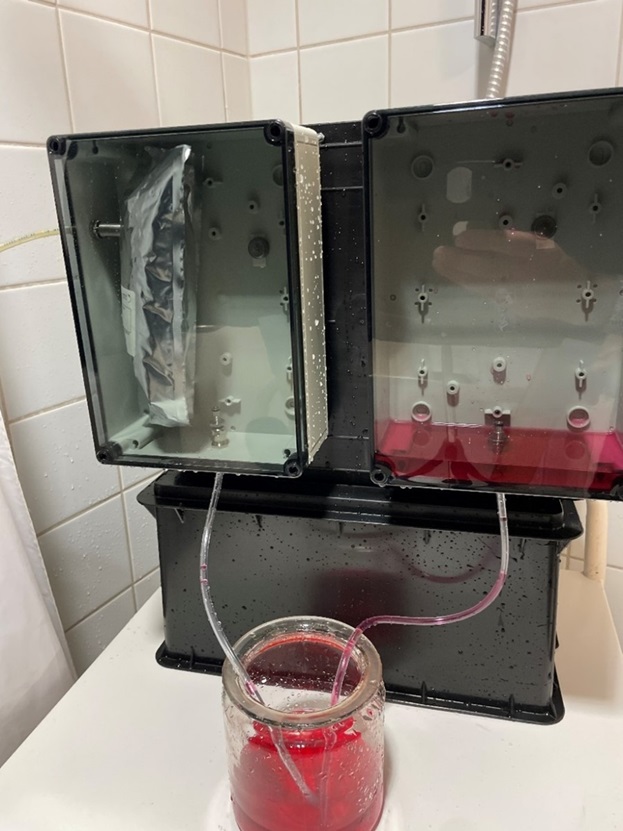
EquiLung equalises pressure
As shown here, EquiLung has equalised the pressure in the cabinet to the left by expanding. Water has not entered the case. In the cabinet to the right, a drop in pressure caused liquid to be sucked inside. The volume of liquid is equal to the difference in the volume of the air inside before and after the pressure drop.
Thus, EquiLung seems to work well in a real-world application where a "watertight" device undergoes a pressure drop caused by a change in temperature.
How effective is EquiLung at handling leaks?
EquiLung's ability to compensate for any given leak depends primarily on the pressure required to deform it (that is, to fill it with air and to empty it).
Typical pressure differentials caused by temperature changes (30°C) are on the order of about 10%, or 100 hPa = mbar (atmospheric pressure is approx. 1000 hPa = mbar).
HALT chamber testing without EquiLung
Figure 2 shows the result of a temperature test on a 3.1 L IP67-rated electronics cabinet made of aluminium without EquiLung.
The cabinet was subjected to rapid thermal cycling between –5° and +55° in a HALT chamber with high airflow. The duration of the temperature change was just below 10 minutes. Additionally, the pressure inside the cabinet was measured.
We can see that the pressure changed almost as quickly as the temperature. In other words, we can expect the pressure inside the cabinet to follow the temperature change more or less directly.
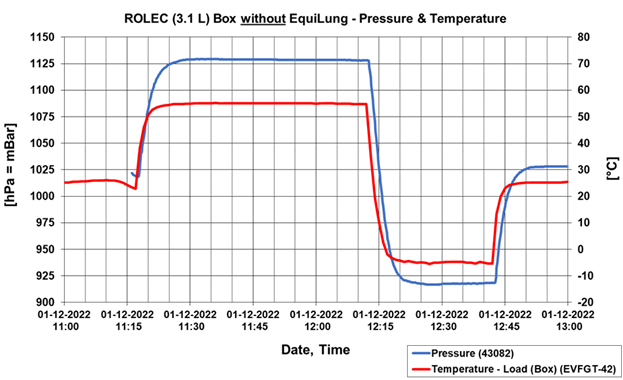
HALT chamber testing with EquiLung
Subsequently, the test was repeated using the same conditions and electronics cabinet, but with an EquiLung installed (see Figure 3). A few additional cycles were run during this test, with temperatures (high and low) marked with circles. During the first two temperature changes (green circles), the EquiLung was placed in the optimal position.
As shown, the EquiLung was able to limit pressure changes to about ±1 hPa. In other words, this is a 100-fold improvement over the test with no EquiLung.
During the later cycle (red circles), the EquiLung was moved slightly, making it somewhat more difficult for it to deform. This resulted in pressure changes on the order of ±2–3 hPa, or about 30–50 times better than the test with no EquiLung.
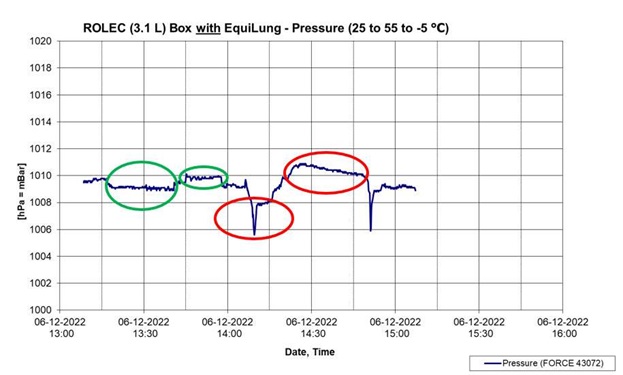
Comparing the 2–3 hPa to the conditions shown in Figure 1, we can see that the red water has been sucked about 15–20 cm up from the glass into the cabinet. This distance (i.e., a water column of 150–200 mm) corresponds to about 15–20 hPa. Consequently, the EquiLung used here would have no trouble compensating for this pressure differential. The 2–3 hPa for the EquiLung used correspond to a water column of just 20–30 mm.
Findings from expanded IPX4 testing with and without EquiLung
The existing IPXX water tests, described in IEC 60529, require the test water to have a temperature within ±5°C of the tested item's temperature (for IPX1 through IPX7). If it is not within this range, pressure compensation is required.
For IPX8, arbitrary temperatures are allowed. The test must simply be "more severe than IPX7", which could include using a different test water temperature. For IPX9, the test water must be at 80°C (±5°C).
This should result in a test that is easier to pass, since the pressure inside the tested item will increase during spraying. In other words, a "standard" IP test provides no information about the tested item's ability to withstand pressure differentials such as those mentioned above in the (very common) worst-case scenario, in which the item is subjected to rain on a warm day.
Water resistance testing with thermal shocks and pressure drops
There is a special water resistance test used in the maritime industry. IEC 60945, section 8.5, titled "Thermal shock (portable equipment)" specifies a test in which the tested item is not only subjected to a thermal shock, but also dipped in water to cause a drop in pressure. Thus, this procedure also tests water tightness.
The first part of the test consists of 1 hour of dry heat at 70°C. Then, the tested item is immersed completely in water at 25°C. Passing this test often proves quite difficult. It should also be noted that the one hour of heat may not be sufficient to create a stable pressure in the tested item before the immersion (depending on its thermal capacity and its air- and watertightness).
Expanded IPX4 testing with two types of EquiLung
Inspired by the IP tests and the maritime test described here, we performed an expanded IPX4 test on four IP66-rated polystyrene electronics cabinets. Three of the cabinets had an EquiLung installed (two Type 1 EquiLungs with 1 mm and 5 mm connections, and one Type 2 EquiLung with a 5 mm connection), and the remaining cabinet was empty. The pressure inside the cabinets was measured throughout the testing process through a small connector.
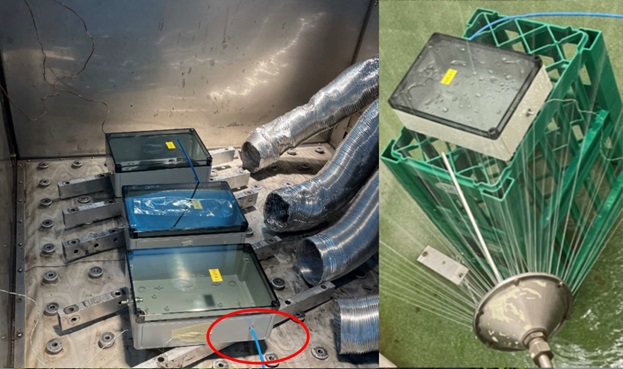
The cabinets were first pre-conditioned to 65°C for thermal stability. The pressure in the cabinets was then equalised at this temperature by briefly opening and closing the connector valve (red circle). Subsequently, the cabinets were subjected to the IPX4 exposure with the test time expanded from 5 to 10 minutes, or until the pressure in the cabinets became stable. The pressure measurements are shown in Figure 5.
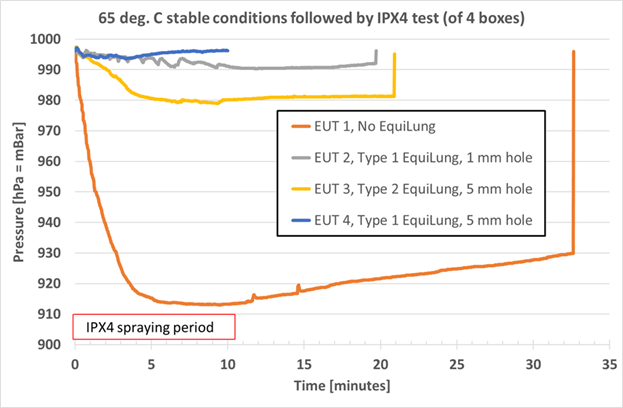
As in the two previous tests, the cabinet with no EquiLung underwent a significant pressure drop (approx. 80 hPa here). Additionally, several large droplets of water entered around this cabinet's gasket during the test.
The Type 1 EquiLung is the same one used in the two previous tests. The 5 mm connecting port yielded an additional difference of 2–3 hPa (i.e., a total pressure differential of 4–6 hPa) compared to the 1 mm port. This could have been caused by a small amount of water in the connector port, and this is an important limitation to note in relation to EquiLung.
The Type 2 EquiLung was made of a thicker, less flexible foil than its Type 1 counterpart. It was also slightly too big for its cabinet. This made it significantly more difficult to deform. The difference could be easily felt with a hand. In this case, the pressure differential was about 15 hPa. No water entered any of the EquiLung-equipped cabinets.
Assessing water penetration through leaks
The tests performed show that a good EquiLung can limit pressure differentials within devices to 1–2 hPa, corresponding to a 10–20 mm water column. This means that water can be excluded from a device entirely if it must be sucked vertically for a distance of more than 10 to 20 mm e.g. through a cable gland mounted in the bottom of a cabinet and up along a wire. . However, in most practical applications, the limitation will be surface tension pulling a droplet of water through a small leak.
To get an idea of the magnitude of this effect, we can examine the Laplace pressure for a circular hole in a vertical wall (reference: C. W. Extrand (2018) Drainage of liquid from a small circular hole in a vertical wall, Journal of Adhesion Science and Technology, 32:10, 1142-1149, DOI:10.1080/01694243.2017.1400802):
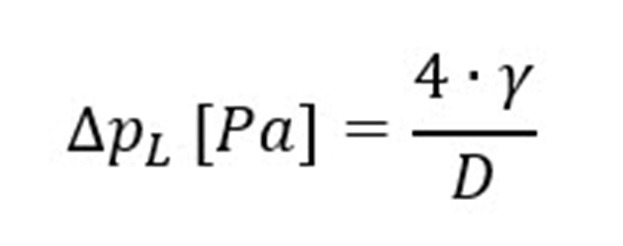
Here, ΔpL is the pressure difference (in pascals) required to force a droplet of liquid with surface tension γ (in N/m) through a circular hole with diameter D (m). For water, γ = 72.8 mN/m. Figure 6 shows the relationship between the hole's diameter and the pressure.
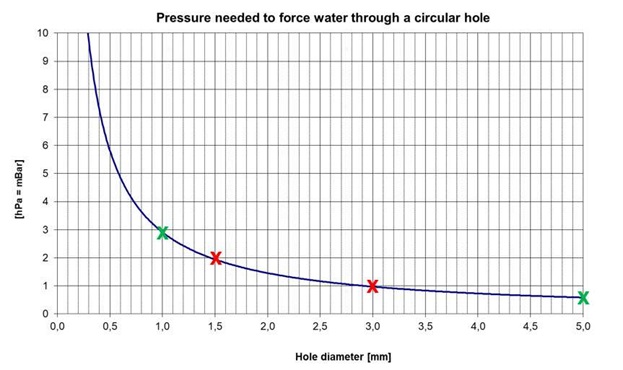
The above expression becomes more complicated if we account for the fact that the "hole material" may be hydrophilic (water-attracting) or hydrophobic (water-repelling). In the case of ordinary construction materials, such as plastic, rubber and metal, however, the impact is less than about 25%.
In practice, oils and dust on the surfaces also have an effect, as does the shape of the hole. Even so, we can be reasonably confident in concluding that an EquiLung capable of limiting pressure differences to about 1–2 hPa can prevent water from penetrating through holes smaller than about 1.5–3 mm (the red crosses in Figure 6).
EquiLung covers various leak types
The report SPM-176 ("Humidity testing of electronics and mechanics") lists the following magnitudes for equivalent leaks in devices:
- Typical IP66 / IP69 devices = 0.2 to 0.5 mm
- "Very small" leaks < 0.02 mm
- Typical watertight requirements < 0.01 mm
Figure 6 shows that all of the leaks listed above can be covered by a typical EquiLung with respect to ingress of water.
We can also see that EquiLung cannot improve significantly on the 1–2 hPa limitation because its intake hole will become too large (in the event that a small droplet forms in the hole). The tested values of 1 mm (slightly too small) and 5 mm (sufficiently large) seem perfectly adequate with regard to Figure 6 (note the green crosses).
Next step: testing EquiLung in real products
With the fundamental design criteria for EquiLung established, the next step is to test the "artificial lung" in real products supplied by companies.