How are hygienic process surfaces chosen?
FORCE Technology works to establish a correlation between surface topography on product contact surfaces and cleanability of materials in contact with, e.g. food, by preparing a hygiene factor.
The statutory requirements are the same regardless of whether you consult the Machinery Directive (2006/42/EC) or EU regulation 852/2004 on the hygiene of foodstuffs.
It is specified that surfaces in contact with products must be smooth and free from cracks and crevices and must not exchange substances with the products. Furthermore, they must be cleanable at a level that ensures that they are clean and free from substances that may contaminate the products before process plants are commissioned in production. In practice, random sampling is used in production to verify that the product contact areas are clean. It is, of course, a prerequisite that good materials have been chosen with cleanable surfaces in the construction phase of machines and process lines.
These general specifications are, however, of little practical use for manufacturers of process equipment. They need specific knowledge about material qualities and surface characteristics to be able to make the right choices.
The current guidelines and rules of thumb are based on the characterization of surface roughness given by the Ra value. This is a measure of the mean distance between top and bottom over a distance of six mm on the surface (according to ISO 4287), and it is often measured only in one direction. Traditionally, this measurement takes place with a physical pickup, which is moved across the surface. The characterization of the surface characteristics by only one number is a major simplification, which is quite easy to infer by observing a typical surface topography for a steel surface, as shown in figure 1. Typical surface profile for stainless steel is shown in figure 2.
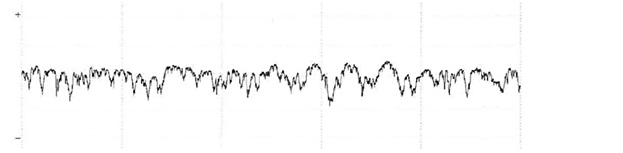
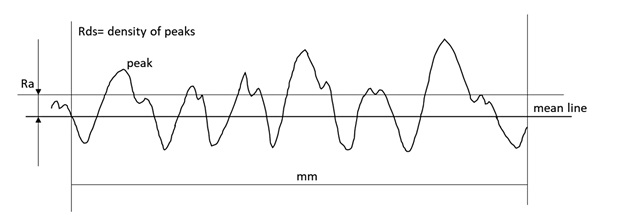
Hygiene factor
To obtain a more adequate description of a surface like the one in figure 1, FORCE Technology has been working on the development of a hygiene factor (HF), which aims to better assess the hygiene quality of a surface. This measure also includes the number of peaks. The idea behind the hygiene factor is for the entire assessment to be carried out using an optical 3D microscope.
The formula for calculating the hygiene factor is shown below. Ra is the geometric mean distance from the mean line in a roughness profile, and Rpd is Peak Density (number of peaks per cm on the roughness profile):
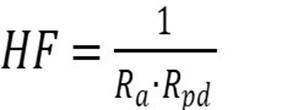
A modification is used in that the parameters are not measured on a fixed roughness profile, as defined in the ISO 4287 standard, which is the raw profile filtered through a high pass and a low pass filter with typical lengths of lc and ls, respectively. Instead, ls= 2.5 µm and lc= 25 µm is used.
When determining the roughness profile for the profiles shown in figure 3, it appears that the distance between top and bottom in the profiles is the same, and the Ra value will therefore be the same. It is, however, evident that there is a difference between the distance between the peaks, and in practice translates in a different topography.
It may therefore be relevant to include a measure of the peak density, which is Rpd.
In this way, it is possible to describe whether the surface has a soft and open shape with relatively few peaks or it is closed with multiple peaks and a short distance between these. Thus, it is possible to differentiate between the profiles shown in figure 3.
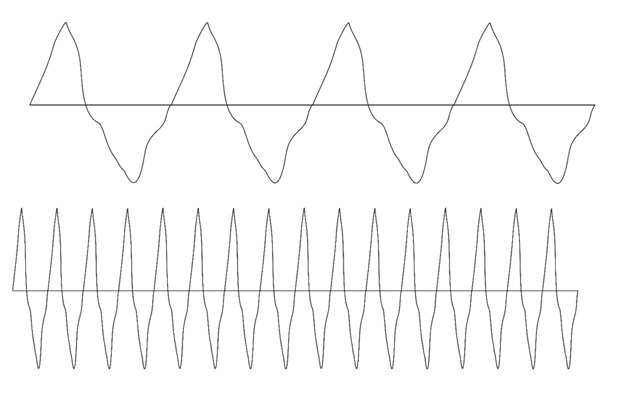
The goal is to use the hygiene factor as a tool to assess the hygiene quality on all types of material without carrying out experimental work.
Requirements for hygienic stainless steel surfaces
Historically, a lot of work has been done to investigate the hygiene quality and cleanability of stainless steel, and the established dogma for hygienic surfaces is an Ra value below 0.8 µm. This is supported by recognised organisations such as European Hygienic Engineering and Design Group (EHEDG) and 3A-Inc in the United States, and it is therefore often the requirement for stainless steel for food contact. There are few examples of how the pharmaceutical industry has its own requirements for surfaces with a lower roughness, e.g. Ra values below 0.3 µm.
It is, however, important to know how the product has been manufactured and its surface finish. Is it a ground surface or, for example, a 2B surface? Microscopic images of both surface types are shown in figure 4. It is obvious that the surface topographies differ, and it is therefore only natural to assume that the Ra value expresses something different in relation to each surface.
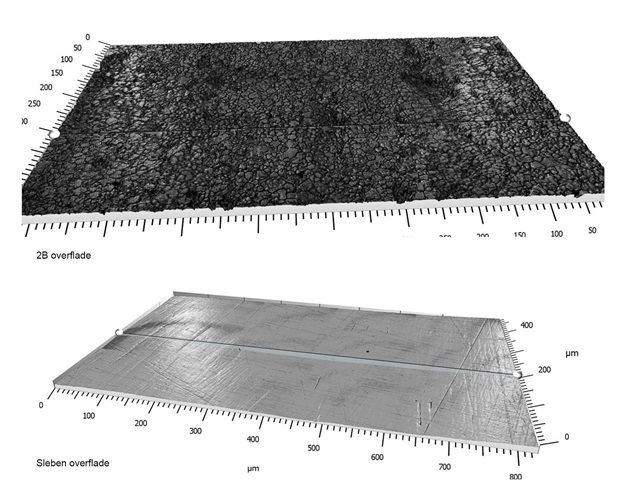
Both surfaces are available at hygienic quality and can easily be delivered with a surface roughness with Ra below 0.8 µm. The 2B surface is the direct product from the steelworks, which is cold-rolled and pickled while the ground surface is processed gradually until the requested surface roughness is obtained, which takes place on the basis of a surface that resembles 2B.
It has still not been concluded what the most hygienic surface is, but it is expected that it would be possible by correlating the hygiene factor and practical examinations of cleanability of different surfaces.
Requirements for hygienic surfaces of plastic and rubber
The same systematism has not been established for plastic and rubber as it has for stainless steel. In practice, a more subjective assessment is made to assess whether a surface is smooth enough to be used for food contact. The reason is that a number of products - such as packing made from rubber - must be more elastic and may therefore be more difficult to measure with the physical surface roughness gauge. The same applies to a number of plastic materials. Some plastic materials, for example PEEK, may, however, be so firm that it is possible to measure roughness.
Microscopy is already used to assess whether plastic and rubber surfaces have unevenness and irregularities. It is therefore natural to consider using 3D microscopy to determine the surface roughness, which also provides data for determining the hygiene factor.
The work with characterization of surface roughness and hygiene factors on plastic and rubber surfaces is a new area which has not yet proven its value in connection with the choice of material solutions with good hygienic quality.
Further development of the hygiene factor
Good preliminary results show that the hygiene factor is directly correlated with cleanability of both stainless steel and selected plastic materials.
The preliminary results and the further work with development of the hygiene factor are based on the activities within the result contract ”Competency centre for hygiene, health, and product safety”.
The goal is to develop a tool which may be used in industry to characterise materials with respect to their hygienic quality solely applying the hygiene factor determined by 3D microscopy. In this way, the hygiene factor may be of practical relevance for industry and be used, for example, to compare new surfaces and surfaces in use.
The future work will include correlation of the hygiene factor with cleaning time and testing of residual microbiological material on surfaces. This will take place partly in pilot plants and partly through field trials on components in industrial plants. Therefore, FORCE Technology would like to hear from companies interested in participating in case studies and practical testing.