How to design and produce composite components with natural flax fibres
The benefits of natural fibres used for structural components was tested in a development project. Get the learnings from our project, where flax-fibres are used in a city bicycle frame.
A city bicycle frame made of bio-based epoxy/flax composite material was produced to demonstrate that sustainable materials can be used for structural composite components. Flax fiber was selected because of it’s unique mechanical properties; high stiffness, low density, and excellent vibration damping.
Natural fiber reinforcements, such as flax fiber, are finding their niche in the composites industry, particularly where lightweight constructions that absorb vibrations are required. They are often used in combination with carbon fiber to produce hybrid materials that offer the advantages of high-stiffness from the carbon and excellent damping from the natural fibers.
Finding the right quality flax fabric
There are at present only a few suppliers of flax fabrics and the weave and thickness choices are limited. The fabrics are typically thicker than glass- and carbon-fiber reinforcements, and this presents a challenge achieving the desired fiber orientations and layer thicknesses in the composite part. Furthermore, the fabric weave tends to have a more open structure, which corresponds to low fiber-weight-fraction and reduced mechanical properties.
For structural applications, such as a city bicycle frame, a hybrid laminate consisting of flax-fiber fabric combined with layers of glass- or carbon-fiber is recommended. If the look of natural fibers is desired, then a layer of flax-fiber can be used for the outer layer.

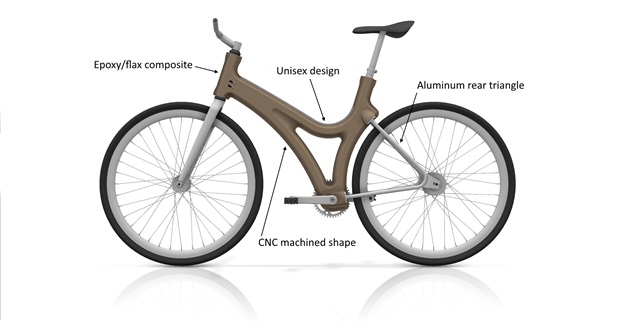
The manufacturing technology
The frame was designed to be manufactured using open molding technology, such as compression molding, which would greatly reduce the manufacturing time and complexity, compared to conventional composite frame production processes. In this approach, the frame consists of two halves, left and right, which are glued together.
The final shape is machined using a simple 3-axis CNC, and aluminum inserts are glued into the frame for attaching the crank and seat post.
Complexity of the geometry
Material drapability is a property that defines how easily a 2-dimensional material, such as a fabric, can be stretched to conform to a 3-dimensional surface. This is very important and needs to be taken into consideration during the design of composite parts. In general; the more complex the geometry, the more difficult the part is to produce. Simple shapes work best, preferably with single curved surfaces or slight double curved surfaces.
In hindsight, the design concept shown above would have been much easier to produce if it didn’t include complex features such as the protrusions for the crank and the cut-out in the middle of the frame. Areas where the flax-fiber fabric did not conform to the shape of the mold can be seen in the prototype above. This frame was produced using vacuum resin infusion (VARTM) technology and illustrates the importance of fabric drapability.
This project was conducted under the Industry’s Composite Laboratory during the period of 2016-2018.