Simulate crane operations
Our SimFlex4 simulator has been extended with crane lifting functionalities. The new software is useful for planning, testing and verification of offshore lifts and for training of operators.
FORCE Technology has over the last three years added new crane functionalities to our SimFlex4 simulator. The developments have been co-financed by the Danish Ministry of Higher Education and Science. The new functionalities allow new types of offshore lifting operations to be simulated for operator training and for planning, testing and verification of offshore lifts. The software can also be applied in a desktop version for feasibility studies and design verifications in the early development phases.
Safe and efficient lifting operations
Ensuring safe and efficient operations by training operators in a simulator has for many years been a well-established practice. The same applies to crane operations as practicing lifting procedures on the real vessel with real crane equipment will often be too risky or impractical.
A simulator provides a virtual and realistic environment to test lifting plans and practise both standard procedures and how to mitigate emergency situations. Lessons can be learnt from mistakes without risking lives or equipment, thereby leading to improved safety and more efficient lifting operations with lower costs and downtime.
Crane simulations in real time with great accuracy
It is important that the simulator offers a realistic environment of the physical behaviour of both vessel and crane. Therefore, the well-established DEN-Mark1 mathematical model of the vessel has been integrated with Algoryx, a state-of-the-art multibody physics library. This integration allows all the moving parts of the crane, including winches, hydraulic actuators, pulleys, wires and payloads to be simulated in real time with great accuracy.
The simulation includes collision detection and friction between objects, for example between the deck of a vessel and the payload resting on the deck.
Fully integrated training cubicle
A training cubicle consisting of a crane operator seat, load instrument on a touch display and six large surrounding flat screens has been developed. This training cubicle is fully integrated with the SimFlex4 simulator and may be configured on various vessel models, both on free floating as well as Jack-Up vessels.
Our Jack-Up control and monitoring system and our dynamic positioning system can be part of the simulation of complex offshore lifting scenarios as shown in photo 1. Examples of configurations that have been tested are a 70m wind turbine service vessel equipped with a motion-compensated gangway (see photo 2 and 3) and a larger four-legged Jack-Up vessel with a 1600-ton leg-encircling installation crane with a boom length of 105 meters.
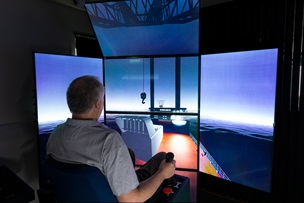
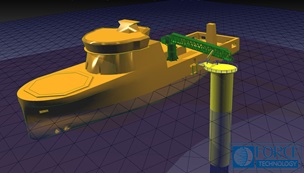
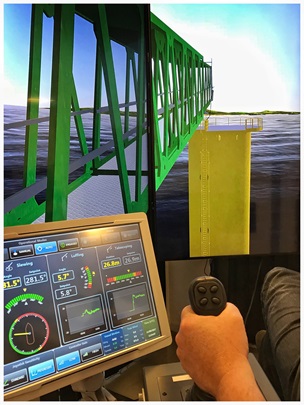
Future extension: testing of remote-controlled lifting equipment
The crane simulator functionality will form the basis of future extensions that will allow for design and testing of complex remote-controlled lifting equipment which is used during installation of wind turbine foundations, towers, blades and other components.
Such equipment is vital to ensure that components can be installed despite being subjected to the harsh offshore environments. Hence there is a special interest in tools that can verify so-called weather windows, i.e. the environmental conditions under which the equipment can be safely used.
Therefore, design tools will be developed that enables the industry to undertake such verifications during the design phases of new equipment. For such a tool, it is of great importance to model forces affecting payloads from turbulent wind. For subsea installations, splash zone forces are equally important. The new lifting equipment software will be developed during 2019-2020 in a new two-year Performance Contract co-financed by the Danish Ministry of Higher Education and Science.
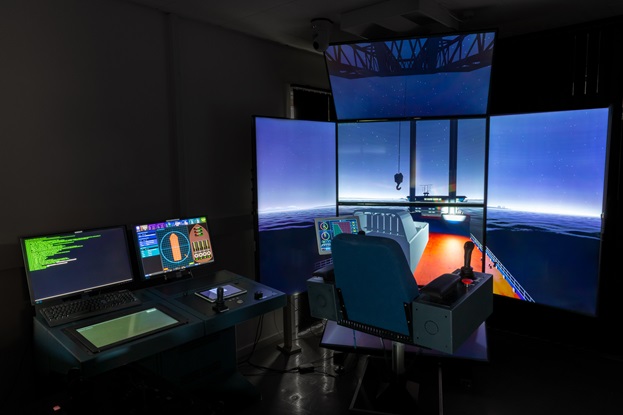