Parametric bulb optimisation
Bulbous bows designed for one top speed condition only will not be efficient in other operational conditions. Especially at lower speeds, they increase wave making and decrease vessel performance, significantly.
Why bulb optimisation?
In times of environmental and economic challenges, retro-fitting of existing ships is a promising investment to support green shipping and guarantee an optimal power demand for your fleet. Ships that are equipped with bulbous bows and that especially operate with operational profiles covering several loading conditions and vessel speeds can benefit from a bulbous bow optimisation.
By considering multiple operational conditions in the design process, it is possible to optimise bulbous bow designs not solely for single speeds and loading conditions, but also for the individual operational profile of each vessel. The result may be a slightly reduced effect of the bulbous bow at the original top speed point, but a significantly improved effect of the bow at the remaining points in the operational speed leading to significant savings on average for the profile.
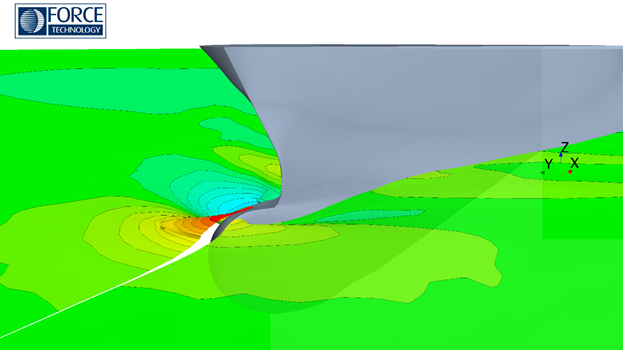
Parametric optimisation
We have developed an advanced, streamlined and cost-efficient approach combining modern computer and RANS-CFD technologies with year-long hydrodynamic experience in ship design and model testing.
By applying parametric multi-objective optimisation, retro-fitted bulbous bows can be designed to minimise fuel costs and the propulsive power demand over the entire operational profile.
By fitting individual steel drawings and your preferred cut out, a parametric bulbous bow can be designed. It can be adjusted according to several different design variables. Bulb length, fullness and breadths can be varied as well as height, section shapes and nose tip elevation. Different typical bulb shapes, such as ∆, O or ∇ shaped bulb cross sections can easily be realised.
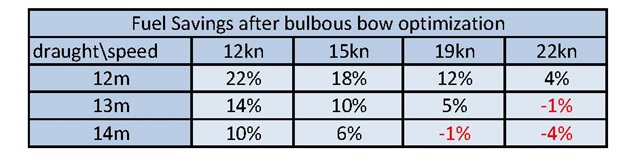
The optimal bulb design
Controlled by automated optimisation algorithms, different bulbous bow designs will be generated varying all applied geometry parameters. For each valid design, CFD simulations will be carried out, taking the necessary geometrical and hydrodynamic design constraints such as volume, LCB and KMT limits, maximum dimensions and geometrical hard points into account.
Based on the outcome of each CFD simulation, the algorithm will adapt the design parameter towards an optimal end result, considering a single or several loading conditions and applied speeds. Parametric optimisation is an efficient tool for optimising bulbous bows over a specific operational profile.
The objective for the optimisation is selected for each individual problem. Good drivers for the optimisation are often a minimum resistance or propulsive power, as the optimisations mainly focus on reducing the ships wave making. Due to our strong experience with ship hull line optimisation, we select an efficient optimisation algorithm such as a linear, non-linear or heuristic algorithm leading to an optimal solution.
The outcome of the automated, parametric optimisation will be benchmarked against the hull lines with the original bulb design. A detailed RANS-CFD investigation will be carried out for both designs in order to quantify potential savings in effective or delivered propeller power. Hereby we can also assist the decision about whether it is profitable to continue the retro-fit process and invest the money in model testing and a conversion of the vessel.
Within the last years of slow steaming, we have worked on numerous retro-fitting projects. Just by optimising the bulbous bow you can achieve fuel savings up to 15 to 20% on average over the complete operational profile. However, the saving potential depends on how far the original optimisation condition is from the conditions in the operational profile.