Reliability strategies and tools
This article explains how to get started with setting a reliability strategy and choosing the right tools to develop reliable electronic products.
How do we build reliability into the product development process from the very beginning? Which tools should we focus on to get the most value for our money? How can we implement these tools optimally? These are the questions many Danish businesses are asking themselves when they want to optimise quality, product development costs, and time to market for new products that incorporate electronics.
In-house knowledge vs. external assistance
Some businesses already have the necessary knowledge in-house, while others need some assistance to develop a reliability strategy with clear goals in terms of desired product lifetime, acceptable rate of failure or service period requirements and to determine which reliability tools are most important in achieving those goals. FORCE Technology has developed this knowledge in the performance contract entitled "A proactive paradigm for electronic product reliability".
One important lesson is that the optimal reliability strategy and associated tools must be adapted to a specific product and a specific situation. This is because every strategy and the tools needed to achieve it depend highly on several factors, such as the product to be developed, the company’s experience and skillset, the application of the product, the volume to be produced, and the price point.
The importance of precise requirements specifications
A precise requirements specification is an important foundation of most reliability strategies. Significant time and money can be saved in the development process by choosing clear success criteria and specific procedures to verify every requirement in terms of:
- hardware
- software
- mechanics
- lifetime
- use environment.
FORCE Technology has found that reliability and robustness issues often stems from requirements specification that was not adapted to the product's actual usage or use environment, and thus does not contain all the relevant parameters. In some cases, the requirements specification from a previous product is used as-is, without taking the new product into account.
Revealing ambiguities and testing strategies
A thorough analysis of existing materials that relate to the new product's actual situation often reveals ambiguities and uncertainties that span multiple fields, thus leading to the risk of not taking changing requirements and conditions into account. A review of the requirements specification, or a requirements specification workshop concerning software and hardware, are effective tools for revealing this. Simulation studies and stress tests are other useful tools.
A requirements specification is an important foundation for a reliability strategy, but it must also be said that it is not the only tool that can ensure reliability and robustness of new products. As mentioned before, the optimum combination depends on the situation at hand.
A well-adapted reliability strategy, based on a thorough requirements specification and supported by relevant tools, can help companies optimize quality and reduce development costs.
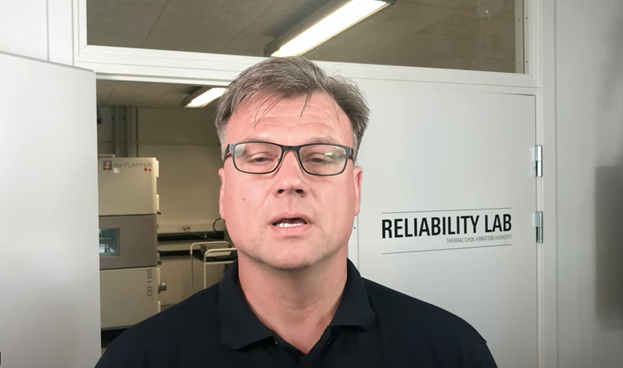