Virtual manoeuvring test using RANS CFD
Evaluation of the manoeuvring characteristics for a ship is always challenging as it depends on numerous different variables such as environmental conditions, ship design, speed, etc.
Generally, a sea trial or a free running model test can determine the manoeuvring characteristics of a ship. However, if the manoeuvrability is deemed insufficient for a given design after the ship has been built, modification to the ship will be extremely expensive. Further, a free running model test is expensive in early design phase.
We are investigating the capabilities of CFD related to simulation of the free sailing manoeuvring tests to be able to assist the maritime industry in future design evaluations related to manoeuvring characteristics.
Evaluation during the design phase
During the early design stage, the designers and shipyards are typically evaluating the manoeuvring abilities based on analytical or regression-based methods.
However, these methods do have limitations when it comes to the accuracy or they may require model test data to build a good mathematical model.
It is also possible to perform direct manoeuvres in model tests, but large tanks and wave basins are required for this and the cost of running such tests is considerable.
CFD to evaluate the manoeuvring capabilities
In this scenario, the CFD simulations can potentially play a strategic role. We are working on an R&D project – public funded as a performance contract from the Ministry of Higher Education and Science. The goal is to investigate if a full set of IMO manoeuvring simulations in free sailing conditions (6-Degree of Freedom) can be made.
The investigated set of simulations cover 35 degrees turning circles and both 10/10 and 20/20 Zig-Zag manoeuvres and the results are compared with experimental data for validation.
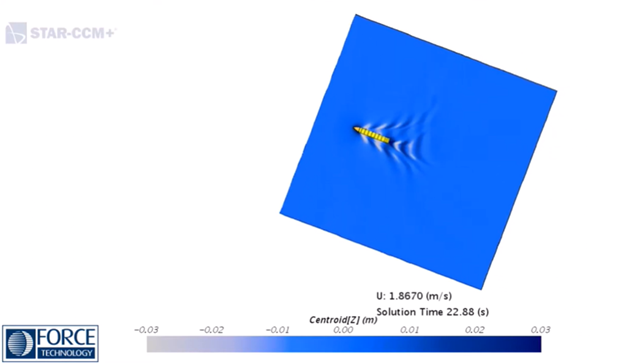
The analysis and outcome
For our analyses we have used the KCS (Korea Container Ship), a benchmark hull recommended by the ITTC and widely used within the maritime community. In the CFD simulations, the vessel, equipped with the rudder, was free in all 6 degrees of freedom, and the propeller was described with a simplified model, the virtual disk model, at constant rotational speed during the manoeuvres. The hull and the rudder, are moving in a background mesh using the overset approach.
The output from the simulations covers, besides the trajectories, an evaluation of the full set of IMO parameters such as advance, transfer, tactical diameter, vessel speed, roll, and yaw angle, and the rate of turning.
The results of the simulations obtained so far look quite promising when compared with the available experimental benchmark data. The deviations between the simulated and measured manoeuvres were in the range of 15% when comparing the evaluated standard IMO parameters.
On top of that, the CFD setup adopted for the mesh and the propeller appears to give reasonable results with a reasonable computational effort. The simulations are performed using the novel mesh approach, Automated Mesh Refinement, which is a powerful method for saving cells. This tool, combined with the simplified propeller model, represents means of reducing the effort without decreasing the accuracy of the results. So, this is a not negligible point, because saving time means delivering results to the client faster and allowing more simulations to run at the same time.
Finally, the advantage of the CFD is that we can provide results for different hull shapes and configurations in order to compare manoeuvring characteristics between designs. This is very useful, especially in the early design stage.
Furthermore, the CFD can provide detailed analysis and visualization of for instance local flow, pressure and vortices that are extremely difficult to obtain in the towing tank tests. So, for now results look promising. It may be that the models can be further refined in the future, but it is believed that they have good potential for practical applications in the design process.