Savings of more than 10% in manufacturing costs for SME
Modularisation and process optimisation have reduced manufacturing costs on core products by more than 10%. But most importantly, a 61-year-old manufacturing company has gained a new mindset.
New opportunities for automation
"It makes us ask ourselves, 'Why didn't we do it sooner?' The benefits are tremendous," says Flemming Jensen, director and co-owner of BSV Krantilbehør A/S.
Approximately 60% of BSV Krantilbehør's sales come from pallet forks and mechanical grabs. In a MADE demonstration project, this SME became aware of further automation opportunities and a new way to organise the manufacturing of these two products.
Jensen answers his own question:
"I think it has to do with the fact that we're a company from the times when the materials were the expensive part and the man-hours weren't a concern. Today, our competitors in Europe and the rest of the world face the same problems with material pricing as we do, so rising wages here in Denmark are a bigger challenge for us. Another part of the story is that rather than standardising, we've come up with a lot of exciting things," he explains.
Jensen emphasises that BSV Krantilbehør, being a contract manufacturing company, still delivers products tailored to customers' needs.
After receiving help from FORCE Technology through a MADE demonstration project, the company can now do this with fewer components and better processes. The manufacturing operations for the company's series of pallet forks and mechanical grabs have been reviewed with a fine-toothed comb, and each product has been broken down into components and processes.
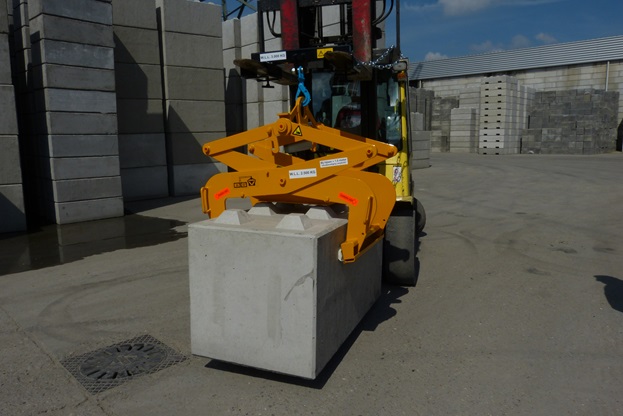
”The aim was to modularise the manufacturing operation, reducing the number of different types of components and using the company's welding robot for as much of the welding as possible," explains Andrew Hoff, lead consultant at FORCE Technology.
Making the most of the workforce and achieving greater flexibility
The pallet fork handles are just one example out of many component variant reductions. The same type of handle that is now used on all pallet forks. This means that more units of this handle must now be produced.
"An increase in the number of units makes it worth looking into ways to automate the production of a component," says Allan Richardy, head of product design and co-owner of BSV Krantilbehør.
Previously, BSV Krantilbehør produced the different types of handles with manual bending. Now, a subcontractor has automated this manufacturing step. As it turns out, an increase in the number of units also makes it worth their while for subcontractors with the right machinery (an automated pipe bender, in this case) to offer their services.
Outsourcing this portion of the manufacturing process has reduced the production cost of a handle by about 30%. More importantly, though, it frees up a resource that can be both expensive and hard to come by for many Danish manufacturers.
”We're making the most of our workforce and achieving greater flexibility," Richardy notes.
This is also the project's main driver, in terms of increasing the use of the company's welding robot instead of welding everything by hand. For example, all forks for the pallet forks are now welded by the welding robot, and this has required adjustments to processes and designs.
That said, automation and modularisation also speed up production and delivery.
”Time is a parameter we can compete on. If we cut delivery times by two weeks while still delivering the same quality and functionality, that's significant to our customers," Jensen explains.
Lowering prices and increasing coverage
The MADE demonstration project become all the rage at BSV Krantilbehør. Now, the company is also looking into reducing the number of different types of steel used for production. This results in higher volumes and better purchase prices, as well as a focus on types of steel which can be reliably delivered.
But most importantly, according to Jensen and Richardy, the project has changed the way people think.
"It changed our organisation's entire mindset. Everyone thinks in terms of modularisation and process optimisation. In the past, if we needed a component, we just invented it. Now, we do everything we can to use existing components. Even if a component is kind of overkill for a particular application, we're ultimately earning more that way," says Richardy.
According to Jensen, modularisation and process optimisation have reduced production costs for pallet forks and mechanical grabs by 10-12%.
”As a company, you can choose to lower the prices of your products or increase coverage. We chose to do both. Now, we're ready to take on a greater share of the market, and we're also continuing to invest in ways to make our manufacturing processes more efficient," Jensen says, adding that BSV Krantilbehør is currently hiring for a dedicated process and procurement optimisation position.
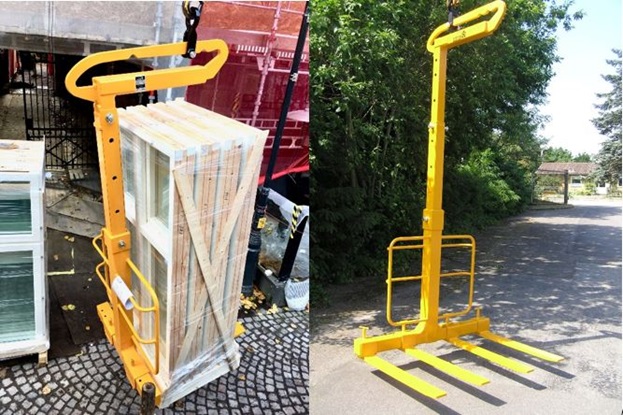