From old wind turbine blades to new products
Worn wind turbine blades are considered problematic waste. Clenflex, an SME, wishes to solve the problems they pose by separating and recycling glass fibre and binders to produce e.g. boxes and tanks.
Worn wind turbine blades are a problematic kind of waste. Clenflex, an SME, wishes to solve the problems by separating and recycling glass fibre and binders to produce boxes, tanks, and other products. A MADE Material Demonstration Project yielded valuable knowledge about the process and the strength of glass fibres.
Wind turbines are an emblem of the green transformation.
While they do harvest carbon-neutral energy from the wind, wind turbines are not only part of the solution. They pose a problem of their own: a waste problem.
According to leading wind power association WindEurope, Europe will have approximately 66,000 tonnes of worn wind turbine blades in 2025. This number is estimated to rise to 230,000 tonnes annually in 2040.
From problems to opportunities
Up until now, the solution has simply been to dispose of the turbine blades, such as by burying them in the ground. Some actors have begun reusing the composite material in wind turbine blades to produce cement.
Clenflex, an SME located in Munkebo, on the island of Fyn, wants to take the next step and recycle the composite material in wind turbine blades. In doing so, a waste problem will become a waste opportunity.
"We want to separate the glass fibres and the binder so they can be used in new glass fibre products, creating a closed loop."Niels Immerkjær / Chief Technology Officer hos Clenflex
Testing has shown that recycled glass fibres retain enough strength to turn old wind turbine blades into products like small tanks and boxes for lifeboats.
Temperature and strength testing
Clenflex is a provider of complete pyrolysis solutions. Using heat, the company breaks down plastic waste into oil that can be converted into various chemicals and used to produce new plastics. The company wants to use the same process to separate glass fibre and binders, and this has been the focal point of a collaboration with FORCE Technology in a MADE Demonstration Project.
"We investigated the ideal temperature for removing all of the binder from the glass fibres. Then, we cast new glass fibre plates using the recycled fibres and studied their tensile strength," explains Leif Rasmussen, a materials and product testing specialist at FORCE Technology.
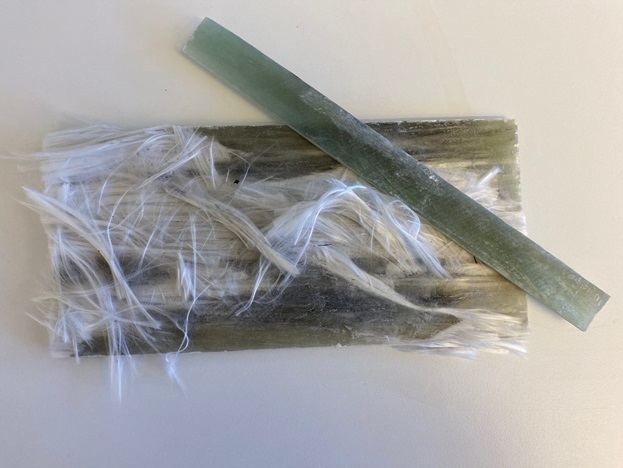
Less strength, but huge potential
Testing showed that recycled glass fibres only have about 25–30% of the strength of new glass fibres - but according to Immerkjær, this is no obstacle to large-scale applications.
"Now, we know how strong glass fibres are after being subjected to the heat treatment needed to separate the binder. There are tons of products that don't require glass fibres to be as strong as they need to be in wind turbine blades, or where recycled glass fibre can be used more as filler in some parts of the product, while new glass fibres are used in areas where maximum strength is needed," Immerkjær says.
"For instance, we've been talking to a business that produces small tanks using glass fibre. In this application, corrosion resistance is what matters, not strength. Other possible applications for recycled glass fibre include boxes for life jackets and inflatable lifeboats on ships."
New Danish exports
The next step for Clenflex will be to scale up the process, making it possible to apply pyrolysis to larger pieces of composite material than the pieces used in the MADE project, which measured about 30 x 20 x 5 cm.
Additionally, Clenflex needs to find a way to clean the binder. One of the company's partners that already converts pyrolysis oil into other chemicals believes it can handle this task. Provided that using pyrolysis for this process is profitable, both the glass fibres and binder will be recyclable.
Immerkjær believes that if this effort succeeds, it will serve as the foundation for a new Danish export.
"We have a group of investors that are supporting the project. A full-scale processing facility will cost around 100 million DKK to construct. This will generate more business for Danish companies that can supply ovens and cooling systems," Immerkjær explains.
This news post is a reproduction of the article "From old wind turbine blades to new products," published by MADE, the Manufacturing Academy of Denmark.
FORCE Technology is a part of MADE. Read more about opportunities at MADE here.