Digital twins of baking ovens - for design, development, management & optimisation
Food processing companies, as well as many other types of industrial companies, constantly rely on and have increased interest in monitoring and optimising their production line.
This in turn also fuels an interest in further developing the production equipment to meet higher yield and standards, such as animal welfare, resource reduction and product quality.
Industry 4.0 focusses on digital integration of the physical production, a useful framework for this is the digital twin. To demonstrate the capabilities of the Digital Twin, FORCE Technology has teamed up with Danish leading developer of industrial baking oven systems Haas-Meincke A/S - Part of Bühler Group, to create a digital twin of one of their test unit located at their facilities in Skovlunde.
What is a digital twin?
A digital twin is a unique digital representation of a physical product, with all its main features and characteristics coupled to physical entity through sensors and often a IoT setup. Depending on the intended use and complexity of the physical entity the digital twin can vary a lot in complexity.
For the simple purely data-driven cases a simple 3D CAD model is supplemented with sensor data to give the user a basic insight in the performance and state of the asset. However, this is either a new concept or what is considered a true digital twin with all the promising and associated business opportunities.
For achieving a true digital twin, a layer of simulation and/or mathematical models, from e.g. high fidelity CAE tools is developed and implemented on top of the 3D CAD and sensor data, providing the possibility to model what-if-scenarios, advance in time, test and train before deployment among others. The large amount of data and insight, then open for training of AI and neural networks, for intelligent autonomous decision making. A level that few commercial digital twins are at today.
As all other products, it is also important to acknowledge that the digital twin can only provide the data and information for which it is designed and setup for. Including skilled expertise within digital twinning from the beginning is therefore highly recommendable.
Adding additional features and outputs to the digital twins afterwards can and will in most cases be easier than adding or changing physical components, but not as cheap as including it from the beginning. However, over complicating the digital twin can also challenge the business case in development cost and time, so balancing this an important aspect.
The business case behind digital twins - it starts in the design phase
As the complexity of digital twins can be high, it is important to evaluate the business case for how much to include, which will be different for each case, company, and product, and maybe develop in phases.
For the case of the baking oven, the foundations for its digital twins has been laid, with a digital twin prototype. The prototype is a functional dynamic real time model without the live sensor connectivity. One can say that it is an advanced virtual prototype prepared for receiving and analysing real data and the first step in developing a true digital twin. A digital twin prototype has a long list of benefits in the design phase, beside from forming the foundation of the final digital twin. Thus, added value is already created before deployment, and identified in the project as:
- Real-time dynamic response of the modelled product for performance evaluation
- Product improvement and testing prior to expensive manufacture and testing
- Imbedded accuracy of high-fidelity simulations in real time output
- In-depth experience using 3D animations using VR
- Lifetime modelling and failure analyses
- Identification of ideal placement of physical sensors
- Easy access and communicate design and performance to stakeholders and team members in one platform.
Using the digital twin
Through this cooperation, FORCE Technology aims to help Haas-Meincke A/S gain a better understanding of their units’ behaviour under different conditions, utilising their expert knowledge to build the digital twin to enable better understanding, visual representation and future development of their product.
This allows them to easily manage and optimise their existing products, design new ones, and present existing and potential new products to customers even before they are made.
Currently, this digital twin allows for adjustability of the baking room temperature, both magnitude and location in the different zones of the baking chamber. This is done by allowing fully adjustable settings of all valves for guiding the airflow inside the baking chamber and the intake/outlet of the burner chamber.
Further improvements aim to add other baking ovens, by operator choice, to give a fully adjustable overview of an entire production line. This will ensure that valve position, length of production line, number of units needed can be determined more accurately before ordering the initial unit.
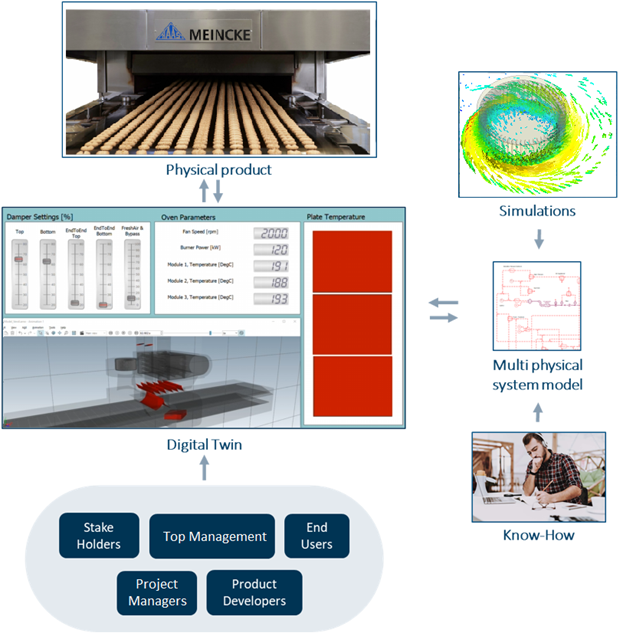