The world's first automatic swab robot is Danish - and start-up receives help with approval
Danish Lifeline Robotics develops the world's first automatic swab robot, but the road to an MDD approval is long. In a MADE demonstration project, FORCE Technology has laid the foundation.
No more false positive COVID-19 results.
The goal for the Odense-based start-up Lifeline Robotics is clear. The company wants to contribute with knowledge and experience to end the pandemic, and the idea of a robot to carry out automatic throat swabs soon emerged.
In just four weeks, a team of researchers managed to complete a prototype which was able to both prepare a test and perform the actual swab, and then only the delivery to the laboratory remains.
While the world's first swab robot was developed in a hurry it is a far slower process to keep track of all the regulations and thus have the robot approved as a medical device.
Lifeline Robotics therefore sought help from a MADE demonstration project where FORCE Technology introduced them to the most important standards within the area and helped the start-up lay the foundation for their future quality control system.
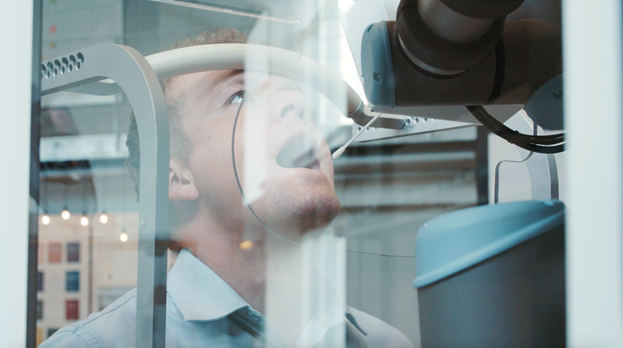
“When companies work with medical devices, they must comply with the regulations in EU’s MDR – Medical Devices Regulation”, says Morten Kjær Johansen, senior specialist from FORCE Technology, and he continues:
”Before the company starts producing the actual equipment it has to develop a quality control system that supports the company's processes, including risk management, to comply with all standards in the area.”
The sparring from the experts has been very beneficial to the start-up:
”The MADE demonstration project has prepared us for entering the world of medical equipment, and it has been the launching pad for becoming a company that can start developing medical devices”, says Andreas Holmetoft Lyder, Technical Product Owner at Lifeline Robotics.
Safety first
Before the company is allowed to attempt the demonstration of the product’s clinical capability on humans, it must meet several requirements in the standards regarding the product and the processes to substantiate that all security related details are under control.
”It is always more expensive to make changes in a development project along the way rather than getting it right from the beginning where the processes are adapted to the standards”, says Morten Kjær Johansen. ”This leads to safer and more suitable products in the end."
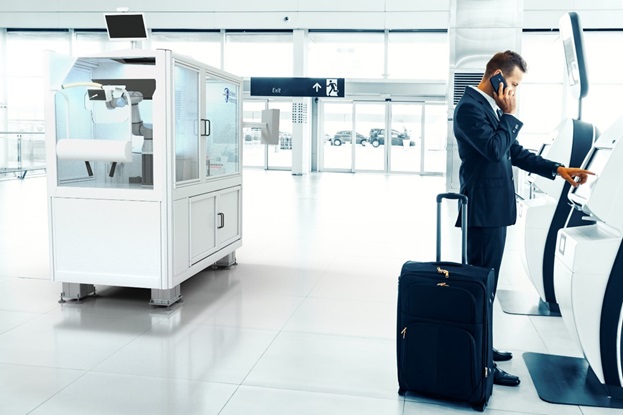
New knowledge called for a new employee
Lifeline Robotics quickly realised the necessity of having a dedicated and experienced coordinator to take the company through all the requirements, and on that basis the start-up had one more employee.
”We could have saved a lot of money if we had known how to go about it from the beginning and hadn't ‘just’ made a prototype of the swab robot right away”, says Julie Dalsgard, CEO at Lifeline Robotics.
”We learnt that we need someone dedicated to establishing a quality control system and working with risk management and usability at our company if we are to have any hope of commercialising a MedTech product”, says Julie Dalsgard.
Continued major need for contact tracing continues the development process
Lifeline Robotics sophisticates the product, and part of the process is to investigate whether sub-elements of the swab are subject to the same requirements as medical devices and to have this part developed, marketed, and sold.
”Even though the COVID-19 is currently heavily declining we still see a major societal need for contact tracing with automated swabbing”, says Julie Dalsgaard and adds:
”The corona pandemic showed us that manual swabbing presents challenges with so many swabbers, and it is inevitable that there is variation in the manual work. However, data from the pandemic have shown that this variation has resulted in a large ratio of false negatives even though PCR analyses have been applied. We would like to change that”, says Julie Dalsgard, CEO for Lifeline Robotics.