Repair, service life extension and short lead time with laser cladding
Laser cladding turned out to be the best method of obtaining wear-resistant components for DSB.
Violent forces are brought into play when DSB’s IC trains set off. Both the end brackets and the pin bolts are exposed to the forces when coupling the train carriages together. Consequently, these train components are worn. When the wear reaches a certain level, the components need replacement.
These special components may, in the worst-case scenario, face a lead time of more than six months. There is typically little or no room for any delays or a wrong number of spare parts without affecting the operation of DSB’s train service.
Repair and service life extension
”It had come to DSB’s attention that FORCE Technology could repair and prolong the service life of critical components, and we initiated tests with laser cladding of the parts. Through our materials know-how, we selected two materials that together would improve the application considerably, making the surfaces extremely wear-resistant”, says Peter Tommy Nielsen, project manager at FORCE Technology.
”Thus, in close dialogue with the customer, we successfully transferred the developed procedure to the actual components. These two weeks’ work yields an approved and very fast repair procedure at a fraction of the price for a new component and, additionally, improved components in comparison with the original train components”, concludes Peter Tommy Nielsen.
In conclusion, DSB is not only secured on-time supplies of pin bolts and end brackets, but also upgraded components with extended service life resulting in cost savings.
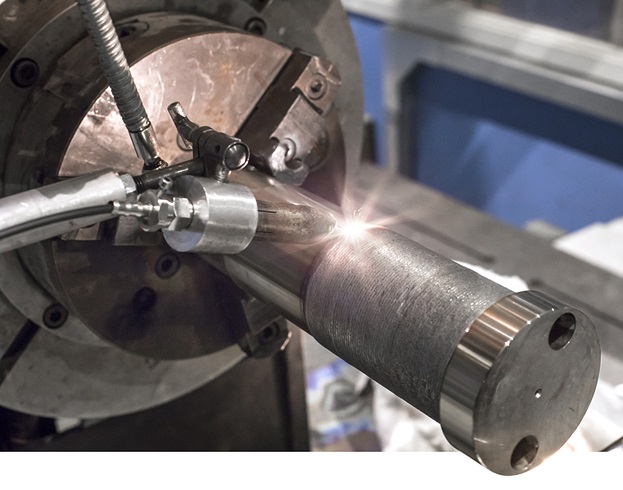