High-energy X-ray tomography ensures flawless 3D-printed rocket engines for Orbex
Orbex utilises high-energy X-ray tomography to inspect 3D-printed rocket engines, ensuring the detection of critical flaws and enhancing launch reliability and sustainability.
Company providing launch systems for microsatellites saves resources with additive manufacturing
Orbex is a British-Danish company developing launch systems for microsatellites. They have a strong focus on sustainability, using biofuel for propulsion and resource-saving additive manufacturing for the rocket's engines.
Aerospace parts need to be 100% flawless before flying, but non-destructive inspection of dense and large AM parts is challenging. Orbex teamed up with us, with support from the European Space Agency, to complete their suite of inspection techniques with high-energy X-ray tomography to ensure their engines are ready to fly.
High-energy X-ray tomography inspection cell is capable of reliably detecting flaws in aerospace applications
3D printing for aerospace applications requires thorough non-destructive inspection to find critical flaws before flying. We developed a high-energy X-ray tomography inspection cell capable of reliably detecting flaws such as stuck powder, deformations and porosity in 3D-printed rocket engines.
Stuck powder could put the launch vehicle’s functionality at risk
Orbex uses an AM technique called selective laser melting, in which multiple lasers weld metallic powder layer by layer to produce the desired shape. After the print process, the remaining powder has to be shaken out. Especially in small internal structures such as cooling channels, powder might get stuck, which cannot be assessed visually.
Stuck powder could compromise the cooling rate of the engine, potentially leading to the total loss of the launch vehicle and payload. On top of this, porosity, inclusions and deviations from the intended shape can put the launch vehicle’s functionality at risk.
X-ray lets you see through the material from every angle
High-energy X-rays are able to penetrate even large and dense samples like a rocket engine and can be recorded as images on an X-ray detector. Taking a large number of X-ray images while rotating the sample means one can see through the material from every angle. A computer algorithm reconstructs these images into a 3D model of the rocket engine, showing both the external and internal features.
Dealing with high-energy X-rays is not without difficulty both for unwanted artefacts in the images and radiation protection. FT has a long tradition of dealing with high-energy X-rays for non-destructive testing, so the CT setup is geared towards the best image quality, reducing unwanted artefacts.
High-energy CT setup scanned the rocket engine; located and quantified non-conformances
Orbex provided us with AM-produced rocket engines with known non-conformances, such as stuck powder in the cooling channels. The high-energy CT setup was able to scan the rocket engine, produce CT data and 3D models as well as precisely locate and quantify these non-conformances. That means using this technique for all newly produced rocket engines at Orbex will bring them a large step closer to fully assuring that the engines are ready to fly.
Project continuation set to benefit the whole European space industry
Orbex is convinced that high-energy X-ray CT is essential for quality control in their space activities and has successfully applied for further funding together with us to develop an inline inspection setup based on the results in this case study to assure the compliance of all their AM-produced space parts. That extends to scanning parts from previous missions for potential reusing and recycling, making their business even more environmentally sustainable.
The European Space Agency has been univocal in its support for this project and its continuation, as it will benefit the whole European space industry.
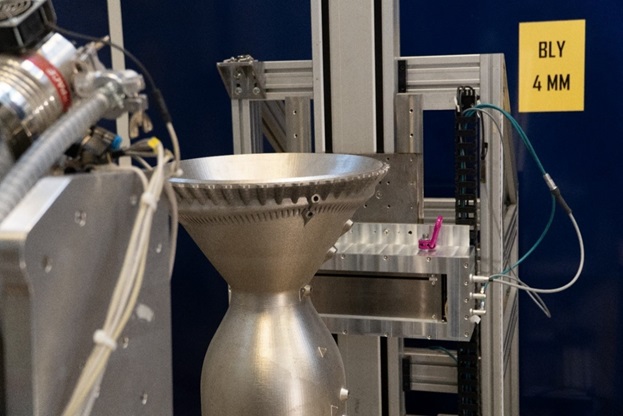
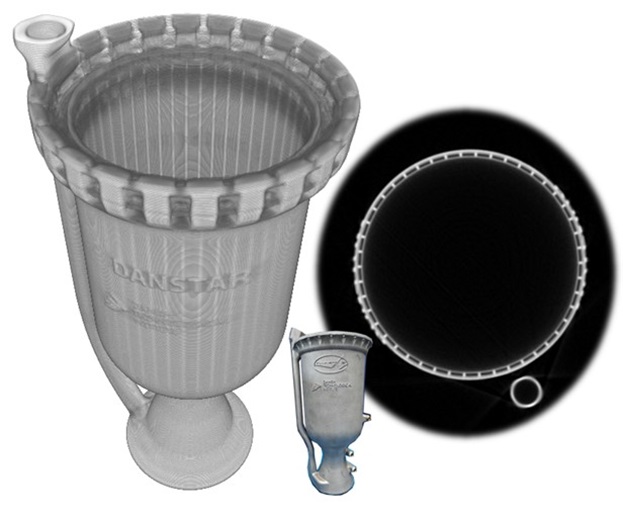