Updates and outcomes from the Digital Factory Acceleration programme
Below, you can find links to cases, events, news, and other relevant material to the Digital Factory Acceleration project.
The Digital Factory Acceleration programme (Den Digitale Fabrik) is designed to help Danish small and medium-sized production companies translate digital innovation into value. The aim is to ensure, that the integration of new digital technologies from the Industry 4.0 agenda results in a competitive advantage, whether related to cost reduction, quality improvement, higher outputs or shorter delivery times.
Find news, notes and cases from the project below.
Cases from participating companies
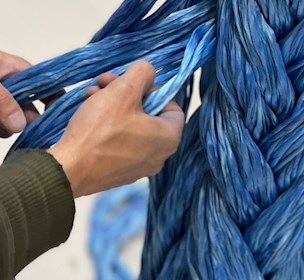
Dynamica Ropes joins Digital Factory Acceleration programme
/Page
Dynamica Ropes wants to increase production efficiency through digitisation.
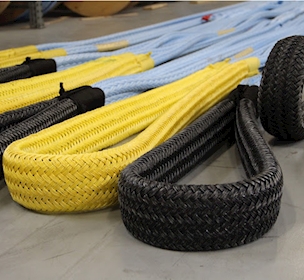
From efficiency to sustainability
/Page
Read about Dynamica Ropes’ digital transformation journey.
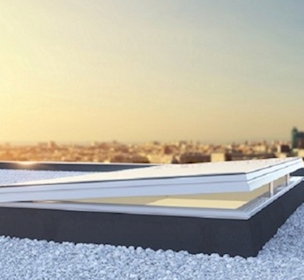
Case article: Unilite A/S
/Page
Adopting a product configurator to improve operational efficiency and customer experience.
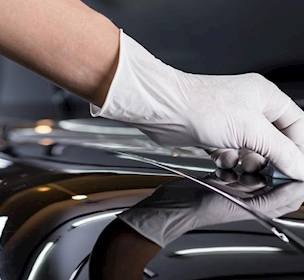
Baden-Jensen A/S case
/Page
Towards a digital future through paperless production.
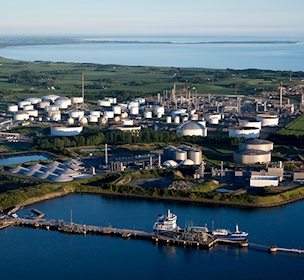
Kalundborg Refinery joins DFA Programme
/Page
Explores ways to enhance operational efficiency.
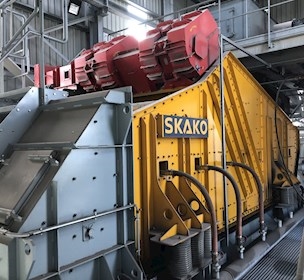
Skako A/S joins DFA programme
/Page
Aims to achieve operational excellence and future growth.
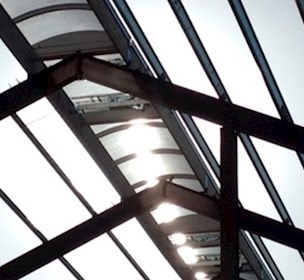
Unilite continues collaboration within DFA project
/Page
Read more about the company's plans to improve production.
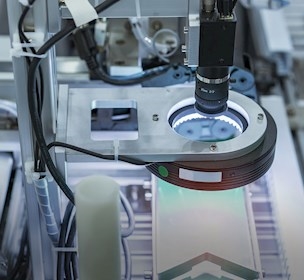
Metalcolour A/S joins DFA programme
/Page
The company has well-defined objectives for the programme's outcome.
Unilite joins DFA programme
/Page
Unilite seeks guidance and support in solving the product configuration problem
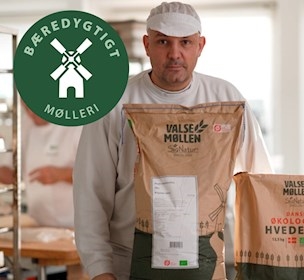
Valsemøllen begins DFR phase of DFA programme
/Page
Valsemøllen has identified three main focus areas for Digital Factory Realisation phase.
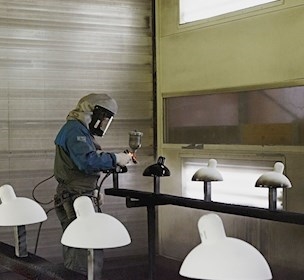
Brandt A/S joins Digital Factory Acceleration programme
/Page
Leading industrial coating company joins DFA programme to enhance growth.
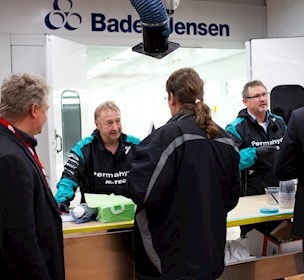
Baden-Jensen A/S joins DFA programme
/Page
The company has high expectations for programme’s outcome.
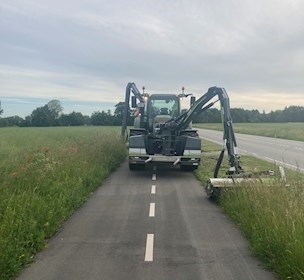
GreenTec completes mapping and analysis phase
/Page
Activity plan to capture identified capacity increase opportunities defined
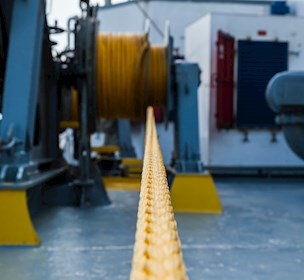
Dynamica Ropes completes Phase 1 of the program
/Page
Dynamica Ropes identified solutions to increase production capacity up to 7 %.
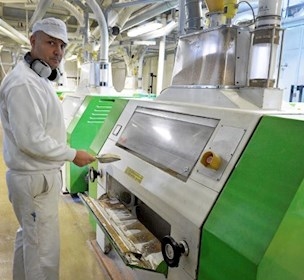
Valsemøllen counts on efficiency increase of 10-20%
/Page
Valsemøllen is developing and strengthening its competitive advantage for future market needs.
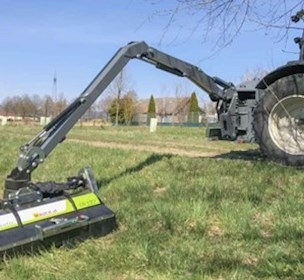
GreenTec joins the programme
/Page
GreenTec is counting on taking productivity to a higher level through digitalisation.
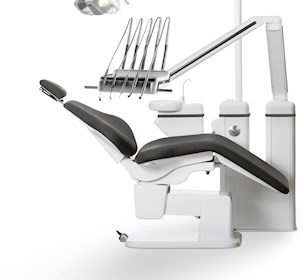
Heka Dental joins Digital Factory Acceleration Programme
/Page
Existing data will be analysed and used to identify the optimisation areas.
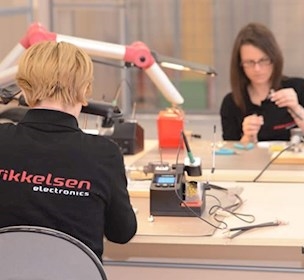
Mikkelsen Electronics joins DFM to increase effectivity
/Page
The programme will help find the best digitalisation solution for their production setting.
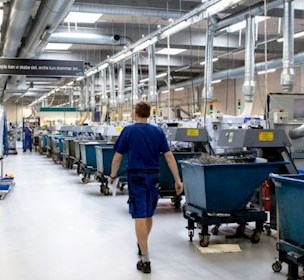
RPA to free up manual capacity by 12% at LPM
/Page
Robot Process Automation has potential to help LPM Production cutting 12% of manual processing time.
Knowledge sharing events
Knowledge sharing event at Aalborg University
/Page
Exploring ways to enhance operational efficiency.
Knowledge-sharing initiatives throughout fall 2023
/Page
Read more about the knowledge-sharing activities
Knowledge dissemination event with EGN
/Page
EGN Denmark members introduced to the DFA programme, its approach and findings.
VIA University students learn about Digital Factory Mapping
/Page
The Digital Factory Mapping approach helps manufacturers accelerate their digital transformation journey.
Building engineers learn about Digital Factory Mapping
/Page
The approach adopted in the Digital Factory Acceleration programme to accelerate the digital journey
Knowledge dissemination event at the Rotary Club
/Page
DFA programme presented in Copenhagen.
Lecture about our Digital Factory Mapping approach
/Page
Introducing Global Business Engineering and Production students to the approaches
The lighthouse for digital innovation event
/Page
Two-hour free event, in collaboration with Business Esbjerg, for production and innovation managers.
Project status, milestones and publications
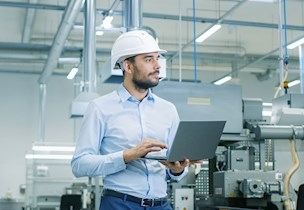
Digital Factory Acceleration: Paperless production
/Page
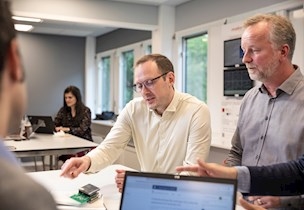
Key challenges and improvement opportunities for SMEs
/Article
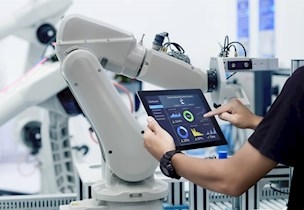
DFA Programme: half-way status
/Page
About the project
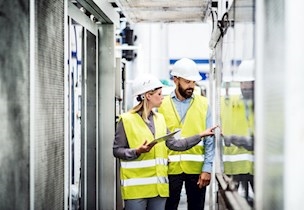
The requirements for joining
/Page
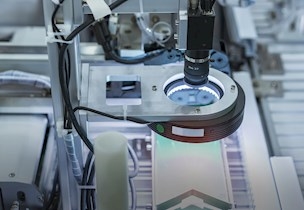
Project