Identification of crystalline materials with X-Ray Diffraction (XRD)
XRD is a powerful tool for identifying crystalline phases in materials and determining their relative proportions. This information is critical for understanding a material's properties and performance, and thus for applications like quality control and for diagnosing issues such as corrosion. XRD can also provide more detailed insights, including crystallographic details, stress analysis, and nanoparticle size measurements. At advanced international research facilities, very small samples can be analysed in a very short amount of time. This capability makes it ideal for studying small samples and performing real-time analysis of industrial processes.
Understanding the structural properties of a material is critical for optimising its performance
While knowing the chemical composition of a material is important, it does not tell the whole story. For instance, metals can consist of different crystallographic phases with dramatically different mechanical properties. In the same way, concrete has its overall strength and durability defined by the arrangement and type of particles. Understanding the structural properties of a material is critical for optimising its performance in the final application.
In XRD, the sample is hit by an X-ray beam, causing the material to scatter the incoming radiation. The scattered radiation reveals detailed information about the arrangement of the atoms in the material. Each crystalline material has its own unique so-called diffraction pattern, and the measured diffraction pattern of a sample can be compared to hundreds of thousands of diffraction patterns collected in international databases to find a match and thus identify the crystal structure of the material.
Understanding composition and crystallography can prolong lifetime
Different materials can share the same chemical composition but differ significantly in their crystal structure. One example is the iron oxides Fe₂O₃ (hematite) and Fe₃O₄ (magnetite). Both contain iron and oxygen, but they have different crystal structures, affecting their properties and behaviour. The distinction plays a crucial role in corrosion processes, and identifying the material can help determine the cause of the corrosion.
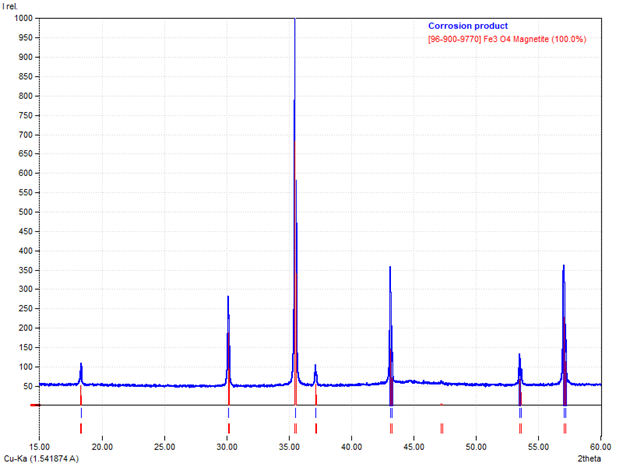
XRD is a powerful tool for distinguishing between phases like hematite and magnetite based on the unique fingerprints from their crystal structures. An example is shown in Figure 1, where a corrosion product is identified as 100% magnetite. Magnetite is generally produced at higher temperatures or environments with limited oxygen compared to hematite. Factors such as pH and electrical potentials can also be important for which iron oxide species is formed. In some cases, a small amount of magnetite can even be beneficial, as it can have a passivating effect on further corrosion to hematite, which is typically more detrimental. Identifying the iron oxides present in corrosion products is thus of great importance, and the primary tool for doing this is XRD.
Fine-point phase determination on surfaces – quality control of concrete
The simplest XRD analysis is the measurement of a homogeneous powder of a substance. However, it is also possible to focus the X-ray beam onto a fine spot on a surface and perform analysis at selected points to map different phases on a surface. As an example, a sample of concrete with multiple phases has been analysed with focusing optics providing a spot on the sample that is 0.4 mm × 0.4 mm. In the picture in Figure 2, 5 different analysis positions have been indicated. XRD analysis was performed on each of these individual spots to determine the various crystalline phases. The sample is approximately 3 cm × 3 cm.
Positionally focused XRD analysis is particularly useful for characterising heterogeneous crystalline materials, such as concrete. A palm-sized cross-section of typical construction-grade concrete may contain dozens of different chemical compounds distributed among the sand and stone aggregate, reinforcement materials and their cement matrix.
The constituent compounds of hardened concrete will inevitably react with each other, as well as with the surrounding environment. Some of these reactions can affect the strength and durability of the concrete structure. With positionally focused XRD, it is possible to quickly characterise the aggregates used, as well as the extent of deleterious reactions in a concrete sample with minimal sample preparation.
An example of this is the information collected from the investigation of the concrete sample, shown in Figure 2 below. The mineral composition of the different aggregate types was verified, and the typical products of cement carbonation were identified, e.g. two different CaCO3 polymorphs (Calcite and Vaterite), as well as amorphous SiO2, which is exsolved from the hydrated cement minerals during the carbonation process.
With the minimal sample preparation required for the analysis described above, the potential for bulk analysis of concrete, aggregates and other similar materials is significant, which in turn can contribute to more efficient recycling of construction materials.
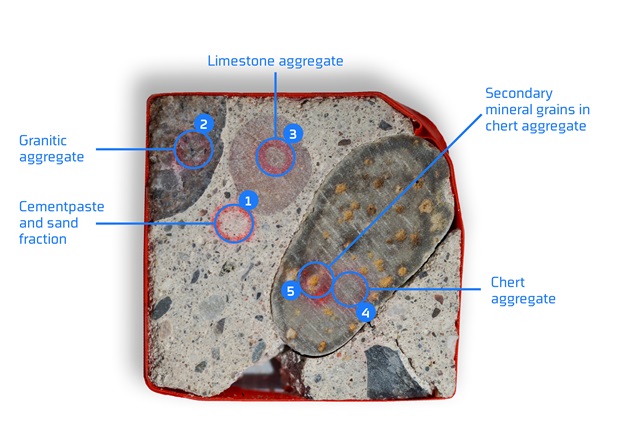
The sky is the limit – everything is possible at international synchrotron facilities
While many samples can be analysed and many questions answered by conventional lab-based XRD (such as from a copper X-ray tube), there sometimes is a need for even more advanced equipment! In modern synchrotron X-ray sources, electrons are accelerated to nearly the speed of light, emitting extremely bright X-rays.
When XRD is performed at a synchrotron, the technique is fundamentally similar to that used in a conventional lab. However, the X-ray beam at a synchrotron is up to 100,000 times brighter than a typical lab source. This extraordinary intensity enables analyses that are otherwise impossible, such as examining extremely small samples or conducting ultrafast measurements. This capability allows for real-time data collection of processes as they occur, providing insights that are unattainable with standard laboratory equipment.
We collaborate with some of the world's most powerful synchrotron facilities to deliver industry access to this world-class equipment. Key collaborations include:
- the European Synchrotron Radiation Facility (ESRF) in Grenoble, France
- the Deutsches Elektronen-Synchrotron (DESY) in Hamburg, Germany
- the MAX IV laboratory in Lund, Sweden
MAX IV, conveniently located near Copenhagen, features a Danish beamline known as DanMAX. DanMAX offers unique capabilities, combining XRD and X-ray tomography to provide crystalline phase information at specific points within a 3D image of the sample. This makes it particularly well-suited for studying industrial materials and processes, opening new possibilities for innovation and problem-solving.
The future of XRD is bright! The technique can be used to answer many questions, both in daily quality control and for answering the deeper questions in research and development projects.