Why model tests should be part of the retrofit process
Large gains can be achieved by retrofitting your vessel, but which retrofit solution fits best? To fully understand and gain the most of your retrofit, accurate model tests are needed to verify possible improvements.
The overall goal of a retrofit is to reduce the fuel consumption, and from a hydrodynamic point of view, this can be done either by reducing the hull resistance, improving the propulsive efficiency or reducing the speed. Reducing the speed is the most obvious choice and has been applied with slow steaming for the last decade. The next step is typically improvement of the bulbous bow and/or replacement of the propeller. Should naturally be replaced in one optimisation process to gain the full advantage immediately.
What must be done prior to a retrofit?
Prior to a retrofit, it is important to identify the operational profile of the vessel from either a performance monitoring system, the old noon reports or thoughts about new operation possibilities. The profile could be anything from two points (loaded/ballast) to a 3x3 matrix with combinations of speeds and draughts. In theory, the matrix could be larger, but in our experience, the result will not differ much, and the CFD calculation time would increase significantly.
The first step – bulbous bow
A logical first optimisation step is to address the hull resistance through a parametric CFD optimisation of the bulbous bow. The overall saving with a new bulbous bow can be up to 20% of the operational profile, but the saving is typically in the range of 5-15%. If the saving is large, it is often an indication of a vessel operating at conditions far from the original design point. In most cases, only a limited saving can be achieved close to the original point or maybe even a small penalty.
The CFD optimisation is typically finalised with a fine mesh RANS CFD calculation for accurate estimation of the reduced hull resistance. However, ship owners do not use this estimation to operate a vessel at higher speeds with unchanged main engine power. Instead, the result is used as input for the propeller vendors to design a propeller to match the new operational profile.
The next step - propeller
In order to obtain the full advantage of the slow steaming and the reduced hull resistance, an improvement of the propulsive efficiency can be made by designing a new propeller for lower speeds. This is typically done by reducing the blade area and hence increase the fuel efficiency. However, this alone does not cause the increase in efficiency.
Today modern propellers are designed by using CFD, and modern profiles are applied for the propeller blades – this also contributes to the improved efficiency. The new propeller will typically have one or two blades less than the original and a 3-10% better performance.
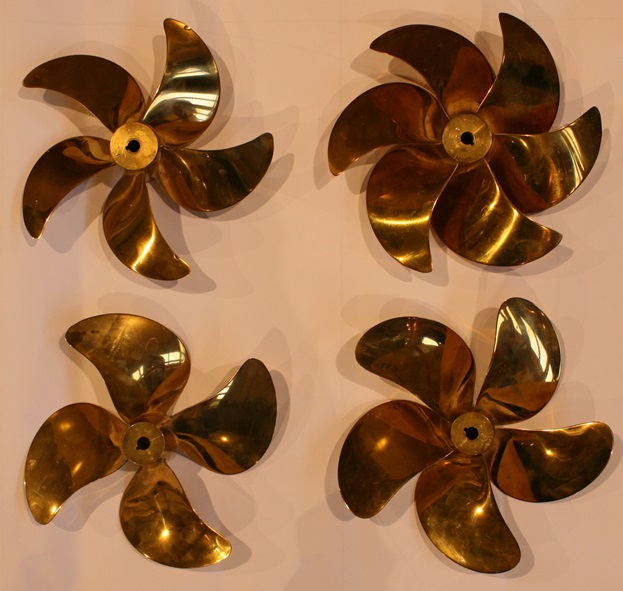
Verification of the calculated savings
With optimised designs of the bulbous bow and propeller, the next step is verification of the calculated savings by accurate self-propulsion model tests. A hull model with a replaceable bulbous bow will be manufactured in a scale suitable for both self-propulsion and later cavitation tests. Also, models of the original and new propeller will be milled in brass.
In the towing tank, we test the new bulbous bow to verify the CFD-calculated savings. As opposed to the tests with a single bulbous bow, we often see that several propeller vendors hand in their proposals for the new propeller. By means of comparative self-propulsion model tests, a comparison is carried out to evaluate the best-performing propeller. Typically, we test 2-3 new propellers, but for some projects, five propeller vendors have handed in their proposals for the best-performing propeller.
After the self-propulsion tests, the most promising designs need to be checked for cavitation performance. Here it is evaluated if the propellers are suitable for operation with regard to durability under operation, i.e. if there is cavitation erosion. During the self-propulsion tests, the best-performing propeller might fail in the cavitation test. In this case, there are two options, either a re-design followed by new tests and possible delays or to proceed with the next best propeller. Therefore, we always recommend testing more than one new propeller.
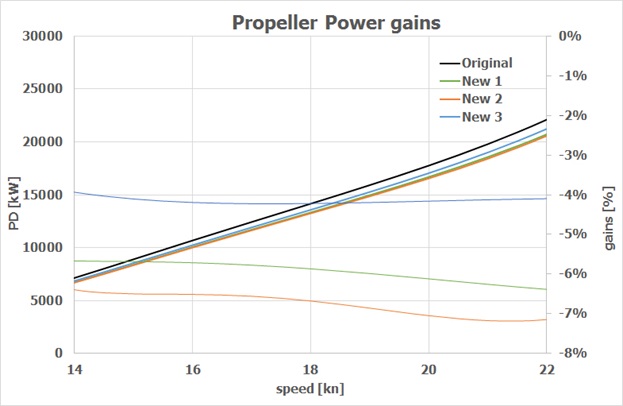