Tailored blade inspection solutions for every stage from factory floor to offshore turbine
Discover specialised ultrasonic inspection setups for wind turbine blades. Designed for both production and in-service use. Fast, flexible and field-proven across blade sizes and conditions.
Ensure blade integrity from day one with automated inspection solutions for production and service
Flaws like weak bonding, delamination or voids can compromise structural integrity during blade manufacturing. As blades increase in size, undetected defects pose greater safety and performance risks. Early, automated inspection is key to ensuring consistent quality, reducing rework and securing long-term blade reliability.
We offer a range of automated scanners to help identify flaws early and maintain consistent quality.
Solutions: Automated ultrasonic P-scan inspection of blades during manufacturing
The most effective non-destructive inspection of a wind turbine blade is automated ultrasonic P-scan, ideally performed immediately after manufacturing.
One scanner type that is always required is the forklift-mounted scanner. Mounted on a slightly modified forklift, it offers excellent coverage, high data quality and resolution, and fast inspection speeds. The unit is fully self-contained, with onboard power and water supply, allowing the operator to focus entirely on scanning. This setup ensures efficient, high-quality data collection for later analysis and reporting without the need for additional equipment or setup time. Depending on blade geometry and inspection requirements, multiple scanners may be needed to complete the inspection of a single blade.
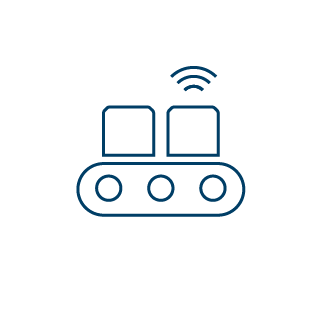
Manufacturing phase
Ensure blade quality from the start with automated ultrasonic inspection systems designed for fast, consistent flaw detection during production.
Self-contained, forklift-mounted scanners with onboard power and water supply make inspections quick and reliable. The integrated setup enables efficient, high-quality data collection ready for analysis and reporting—without extra equipment or time-consuming setup.
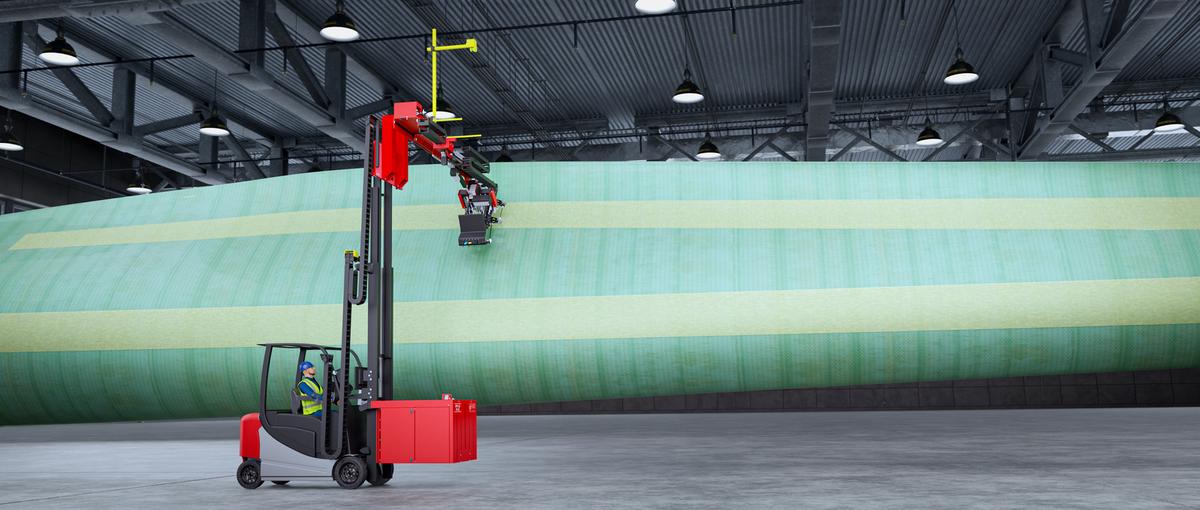
The AMS-111PA: the most advanced scanner for inspection of the largest blades
The AMS-111PA covers scan widths up to 1 m with high resolution and operates at speeds around 30 mm/sec.
Equipped with advanced electronics for precise, multi-position blade inspection.
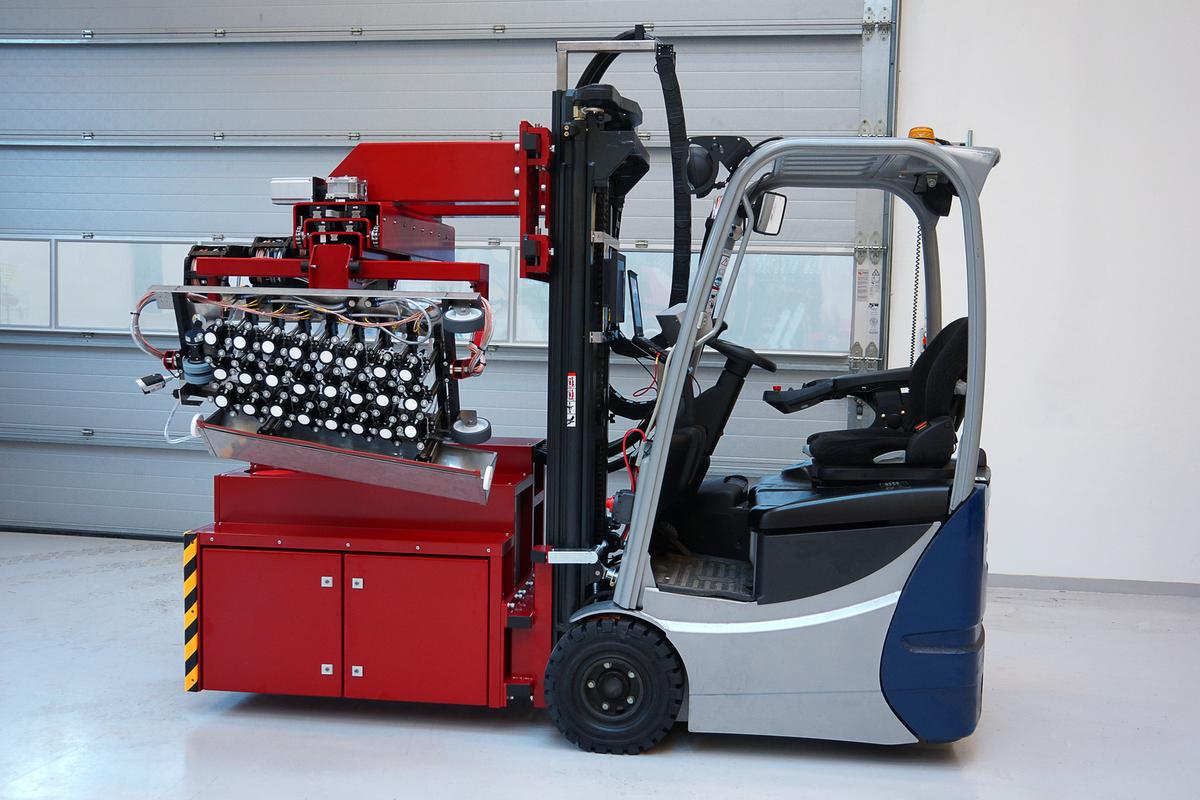
The AMS-71PA: has more controlled moving axes
The AMS-71PA scanner performs the same core functions as the AMS-111PA but features a smaller probe array and only two controlled axes (up/down and in/out).
Movement along the blade is handled by the forklift at a pre-defined speed, programmed by Still.
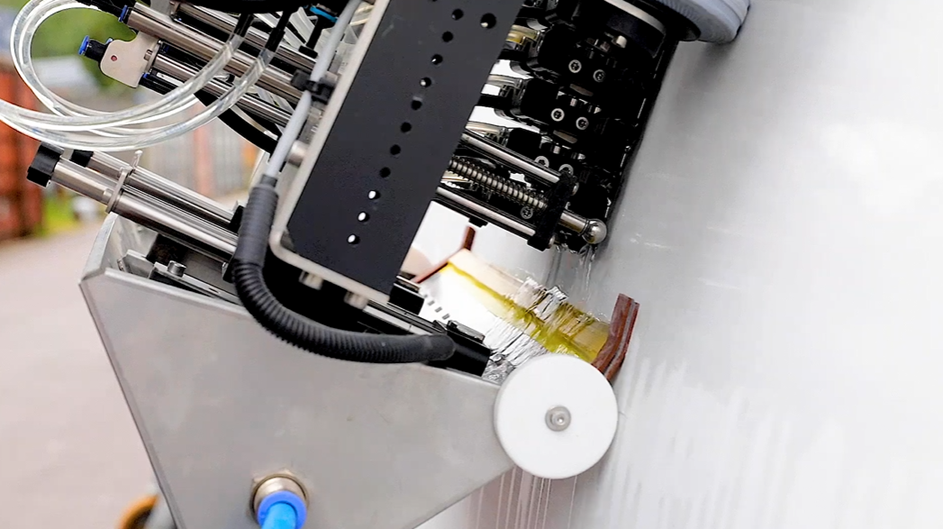
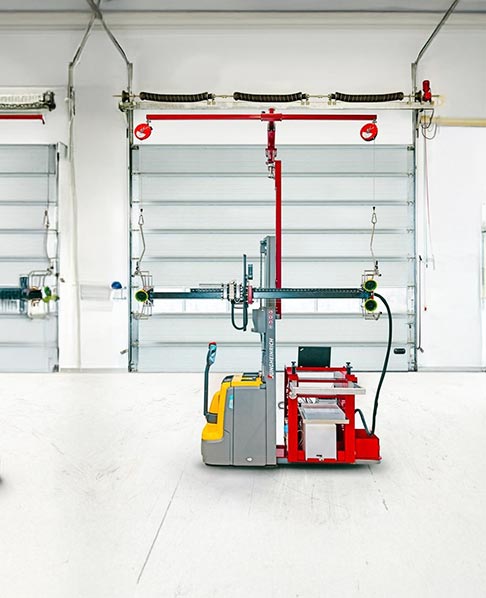
The AMS-91PA: flexible scanner for complex or repaired blade areas
A compact supplement to forklift-mounted scanners, the AMS-91PA is ideal for hard-to-reach or repaired blade areas.
Its small size and versatile configuration options allow scanning in any position.
Available with or without pallet lifter, it’s a flexible choice trusted by blade manufacturers for precise, efficient inspections.
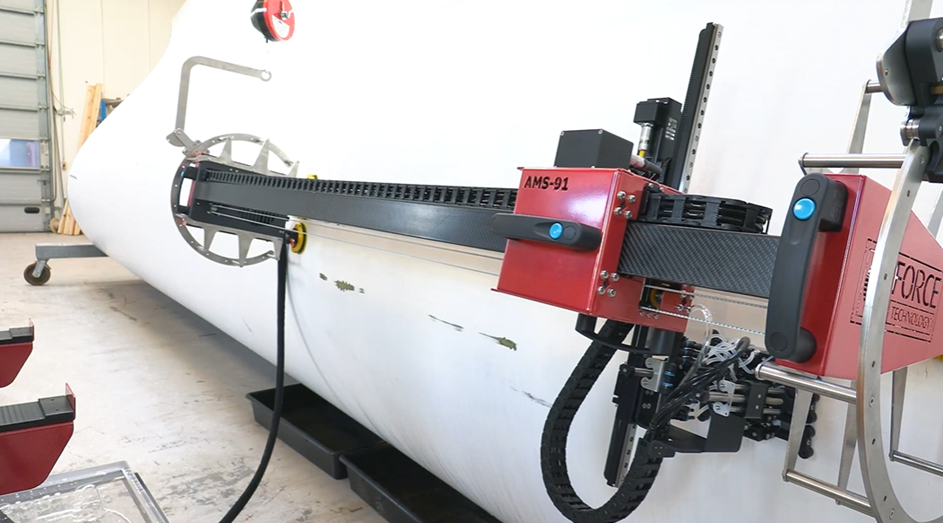
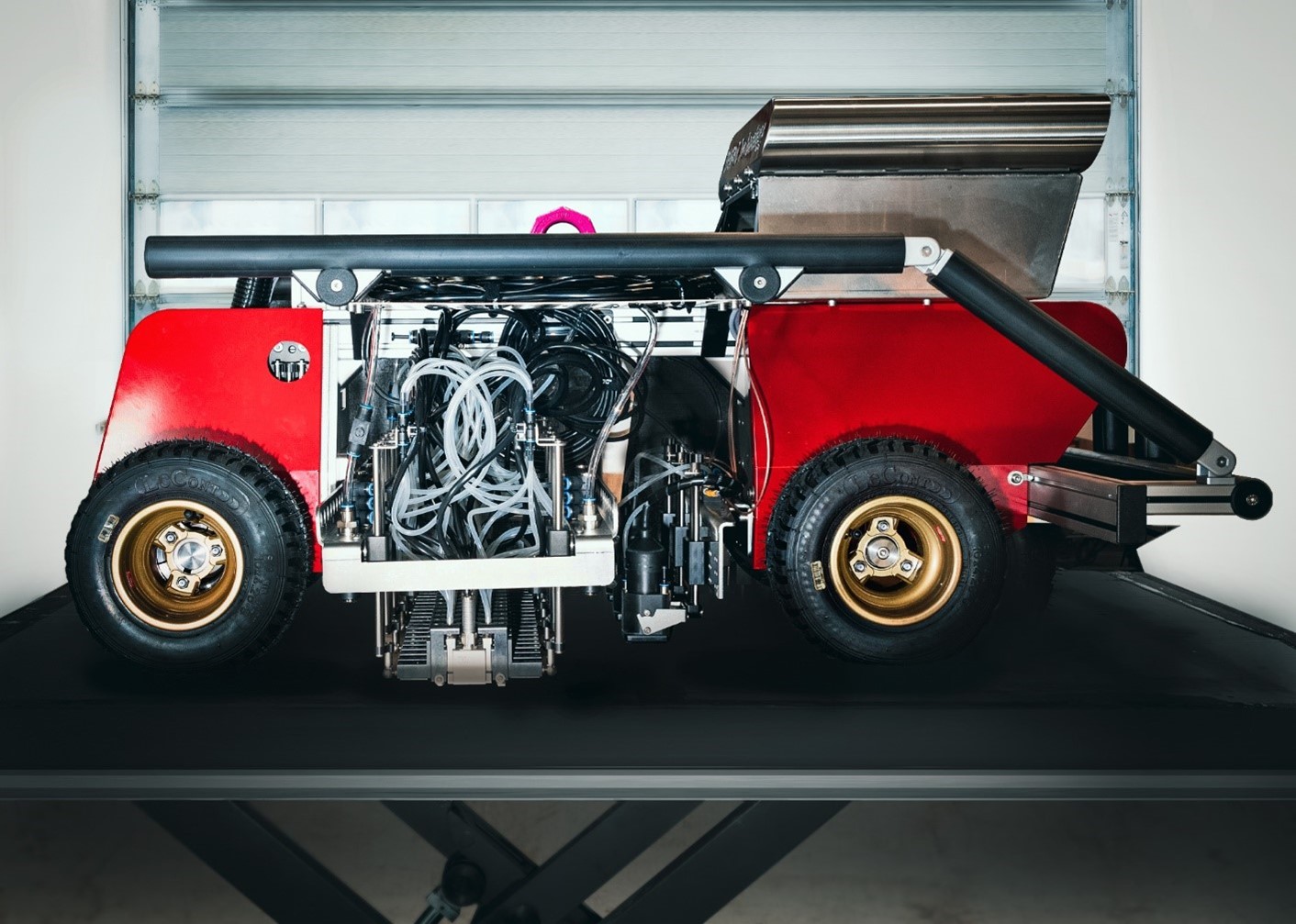
The AMS-46PA: efficient spar cap inspection in the workshop
This version of the AMS-46PA is the narrow configuration, tailored for spar caps assembled from layered carbon profiles.
Used in the workshop to verify bonding quality before installation, it supports both Phased Array and single crystal line scan probes.
It is available with auto-steering for efficient, hands-free operation.
Solutions: Automated ultrasonic P-scan inspection of blades during service
Once in operation, turbine blades are exposed to harsh weather, strong winds, and constant mechanical stress, especially as blade lengths increase. These conditions heighten the risk of damage over time. In-service inspections are essential to detect flaws early and prevent costly failures. While similar in principle to inspections performed during manufacturing, in-service solutions must adapt to more challenging access conditions. Rope access is frequently used to access outer areas of the wind turbine. Below are some of the flexible scanner setups available for in-field blade inspection.
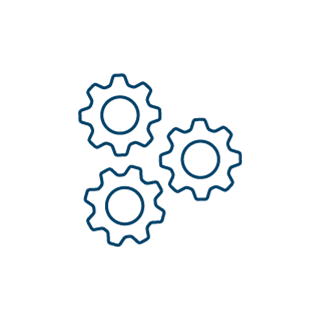
In-service phase
Detect damage early and minimise downtime with flexible blade inspection solutions tailored for challenging on-site conditions.
Designed for rope access or basket setups, our P-scan systems adapt to harsh environments and complex geometries—delivering high-precision data without compromising safety or efficiency.
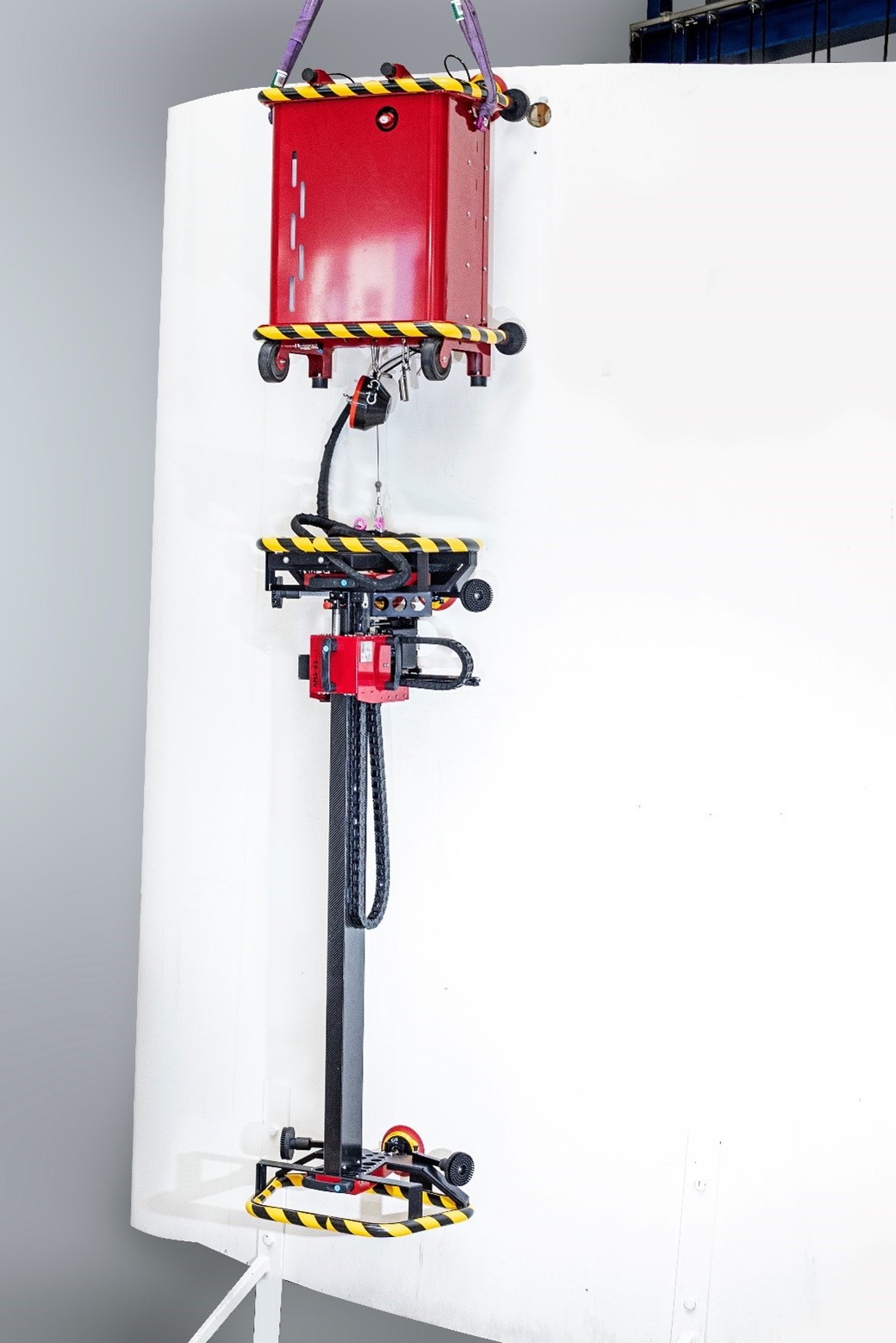
The AMS-91PA Rope: enables high-precision blade inspection via rope access
A control box is lowered onto the blade and attached using suction cups.
- Inside the control box: the P-scan system, embedded computer, water pump, vacuum pump (for both the control unit and scanner suction cups) and a water container.
- Outside the control box: a weight balancer suspends the scanner, making it effectively weightless for the operator.
The scanner is mounted on the blade at the planned inspection area and is equipped with:
- Phased Array probes, single crystal line probes, or both
- Integrated water supply for automated coupling
- An external video screen for controlling scanner mechanics and the P-scan interface (e.g. start/stop scanning), as well as for visualising collected data
- Suction cups that can be released individually at each end or simultaneously via a central control button
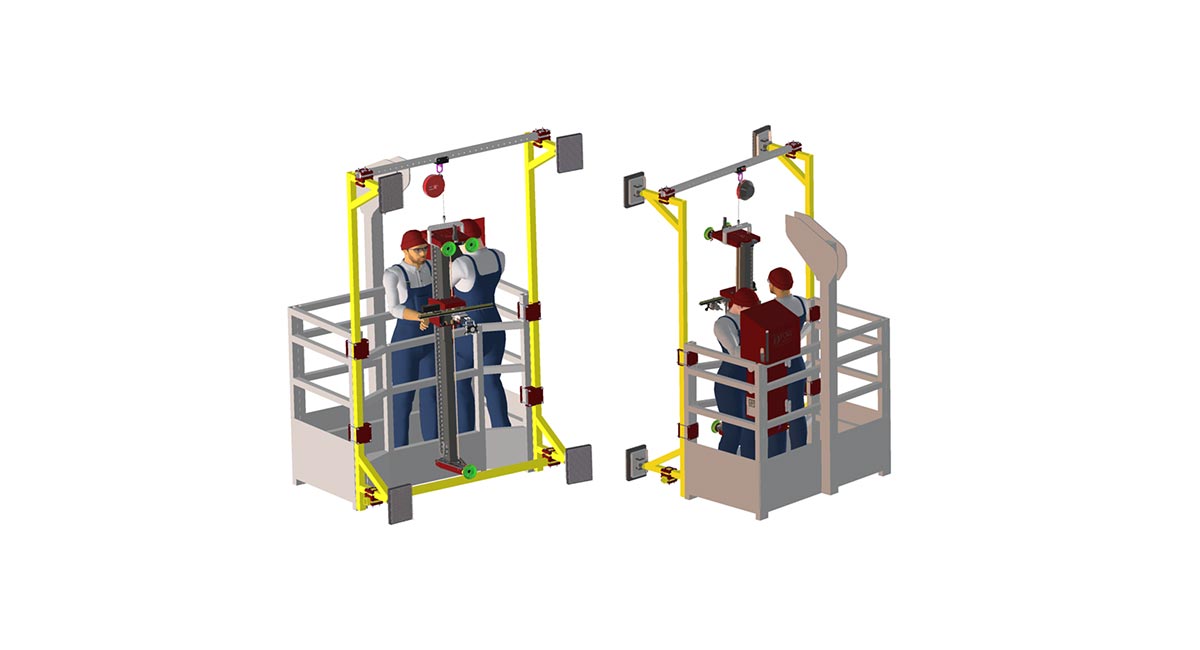
The AMS-91PA Basket: efficient blade scanning with extended coverage
The same scanner in a different configuration can be operated from a basket. In that case, the design of the control unit changes and moves from the blade to the basket. The scanner now hangs in the same weight balancer but on the basket and is mounted on the blade in the same way.
The scanner coverage is flexible with respect to the width of the scanning area. Lengthwise, the coverage is roughly 1,5 m per scanning, here seen with two operators ready for inspection in front and rear view.
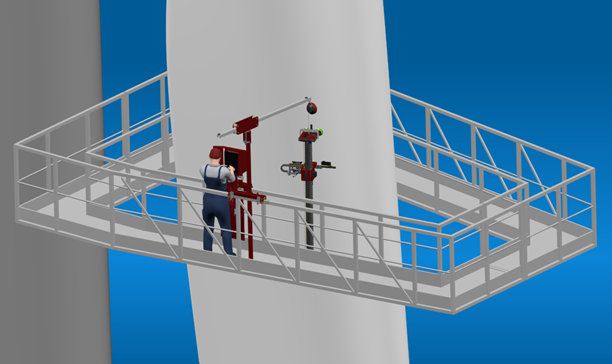
The AMS-91 scanner: versatile 360° blade scanning for any scenario
The same multi-purpose AMS-91 scanner can be mounted on a 360° platform if required.
The possibilities are almost endless with this scanner.