Portable NDT scanner efficiently detects and evaluates defects in critical structures
P-Scan is an advanced automated NDT system for inspecting materials. It detects and documents defects in welds, pipelines and pressure vessels, offering safer, more cost-effective and precise inspections.
Manual inspection: Time-consuming and often imprecise
Inspecting critical structures in industries such as oil and gas, petrochemicals, and power generation is fraught with challenges, including high costs, significant time investments and the necessity for skilled labour.
Traditional manual inspection methods can be imprecise and may lead to missed defects or false positives. The requirement for highly trained professionals further escalates costs and limits scalability, making efficient and accurate inspections a challenging goal to achieve.
"The P-Scan system has considerably improved the inspection process of our wind turbine blades. The inspection time is drastically reduced, and the quality is drastically increased. Besides that, the resources required for inspection are significantly reduced.
Implementing FORCE Technology's automated ultrasonic system has undoubtedly positively impacted our final product and the economy."
/Customer, Wind power sector
Automated NDT scanning and data analysis is an efficient method to achieve consistent inspection quality
The P-Scan system is an innovative NDT solution that addresses these challenges. It utilises advanced ultrasonic technology to deliver high-resolution images and precise measurements of defects in various materials.
The system's automated scanning, data acquisition and analysis features ensure consistent and thorough inspections, significantly improving reliability and efficiency.
-
Excellent and proven high precision rate
Round-robin tests have proven significantly better detection rates for automated UT inspection than manual UT inspection. -
Safer working environment
By reducing the need for manual inspections, the P-Scan enhances safety by minimising workers' exposure to hazardous environments and potential inspection errors. -
More cost-effective than manual inspection
Automation and reduced labour requirements make the P-Scan a more economical solution for inspecting critical structures.
There is a P-Scan system for any inspection need
The P-Scan system is available in both custom and standard configurations, ensuring a perfect solution for every NDT inspection requirement. To help us advise you on the optimal system for your context and materials, please consider the following questions:
-
What materials will you be inspecting?
Different materials may require specific types of scanners and ultrasound settings to ensure accurate and reliable results. -
What is the size of the objects you need to scan?
The size of the materials being inspected will influence the choice of scanner and system configuration to accommodate various dimensions and shapes. -
How long will the system be in use?
Consider the duration and frequency of usage to ensure the system's durability and reliability over time and its ability to handle continuous operation if needed.
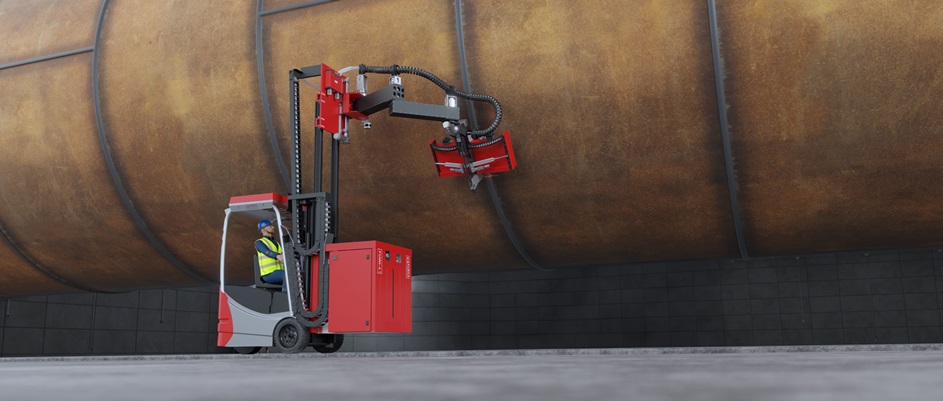
Want to find out how we can help?
P-Scan is an advanced automated NDT system for inspecting materials. It detects and documents defects in welds, pipelines and pressure vessels, offering safer, more cost-effective and precise inspections.P-Scan specifications
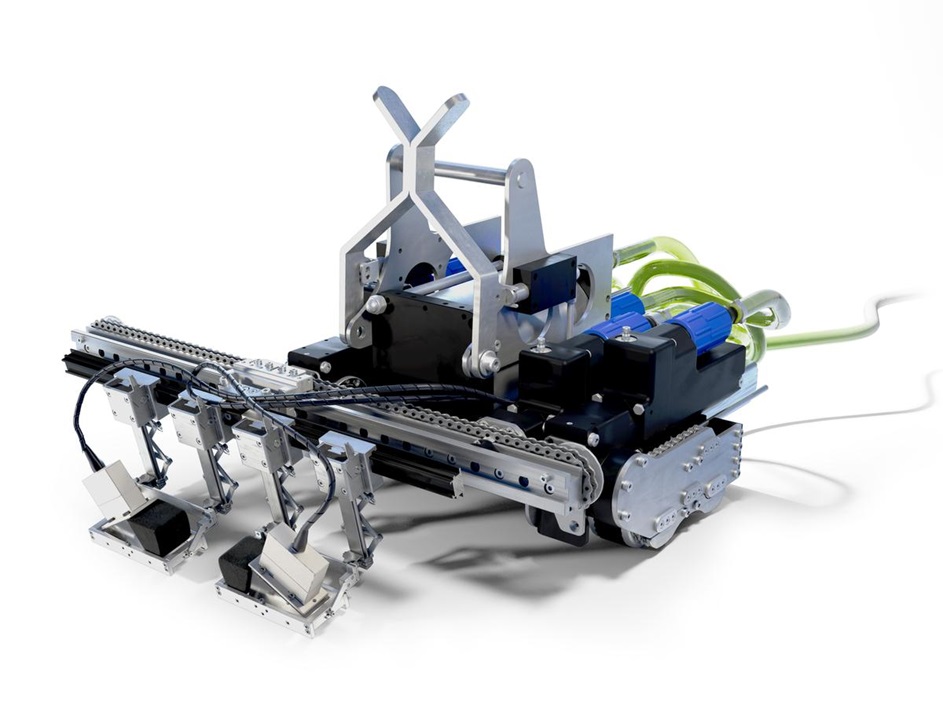
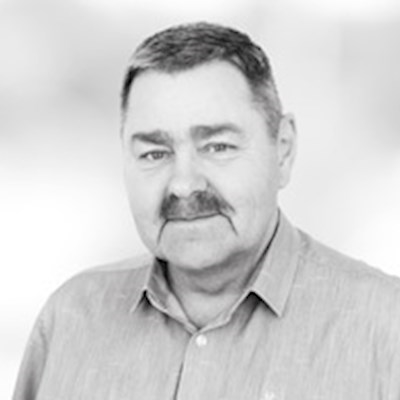
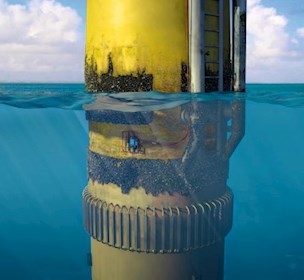
Ultrasound inspection for systems in operation
/Service
Automated ultrasound inspection can be used to analyse the state of components and systems in operation.
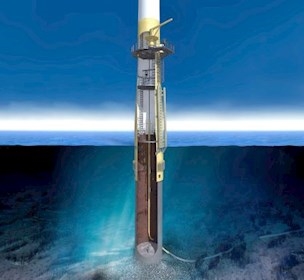
Cloud-based, automated ultrasound inspection
/Service
Automated, cloud-based ultrasound inspection reduces inspection time and secures data.
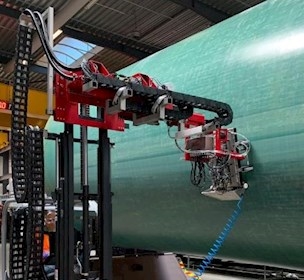
X-ray and ultrasonic inspection in production lines
/Service
Optimising manufacturing process control and product quality with X-ray and ultrasonic inspection.