Optimising manufacturing with automated ultrasound inspection for systems in operation
Automated ultrasound inspection can be used to analyse the state of components and systems during deployment. Quickly gain insight into how to extend component lifetimes and determine where repairs are needed to avoid accidents.
As a facility owner or operator, regular inspections are an important part of your work. You may need to assess the status of piping, wind turbine blades, heat exchangers, or tanks to optimise your operation and ensure that no accidents occur at the facility.
Automated ultrasound allows you to operate more cost-effectively by examining your product or structure and inspecting it for potential faults that could impact quality, safety, and performance.
Below are some of the benefits of automated ultrasound inspection:
- Lifetime extension and cost reduction
Facility owners can significantly improve their financial situation by extending the lifetime of all or part of their systems. Automated ultrasound inspection offers valuable data and input for use in determining the status of components and systems. For example, you can determine if wind turbine foundation components, jacket structures, or tanks need to be replaced or repaired, or if their lifetimes can be extended.
- Get to the bottom of accidents and avoid repeat incidents
If an accident occurs at your facility, you need to determine what went wrong and prevent it from happening again. You also need to know whether similar components at your facility have the same issue that increases the risk of future accidents. With automated ultrasound equipment, you can be certain that your weld inspections and corrosion measurements are objective and accurate.
- Improve your working environment and minimise accident risks
With an automated ultrasound inspection solution, you can use a remote-controlled robot to inspect the inside of a tank that contains or is located in a hazardous environment. This avoids the need for meticulous cleaning and eliminates the risk of exposing personnel to hazards like ionising radiation, extreme heat, and toxic vapours.
Detecting defects with automated ultrasound inspection
In addition to knowing the status of your systems and how to extend their lifetimes, finding faults in your products and structures is also important to avoid complaints in the future.
With automated ultrasound inspection, you get:
- Complete inspections
- Full documentation
- Faster production
- Less unplanned downtime
- Improved product quality
- Reduced manufacturing costs.
You can use our automated ultrasound solutions to:
- Inspect welds
- Measure material thickness and corrosion
- Detect cracks and crevices
- Specify ToFD defect sizes.
An add-on is also available to upload all your data to a cloud-based platform. This way, you can view data from all of your manufacturing sites at once and access your data from anywhere in the world.
Wind turbine blade defect types
A wind turbine blade is a complex structure that has the potential to contain a variety of defects. Due to the physical nature and geometry of these defects, automated ultrasound inspection is especially well-suited to detecting defects in wind turbine blades.
Our automated ultrasound solutions scan your turbine blades for typical internal manufacturing defects, including delamination, adhesive defects, and resin-deficient areas. The ultrasonic equipment visualises and measures the area, depth, and total laminar thickness of defects.
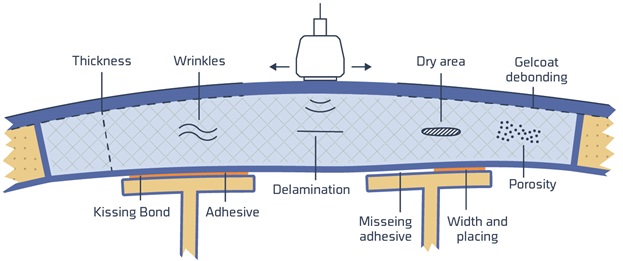
Solutions for production control
We also have solutions for automated X-ray and ultrasound inspection for production and product quality control.
Get help to optimise the operation of your system
Contact us for help choosing the right automated ultrasound inspection equipment to meet your needs. We have more than 40 years of experience developing both standardised equipment and unique, customer-specific solutions.
Services
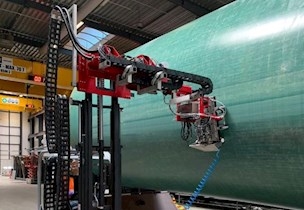
X-ray and ultrasonic inspection in production lines
Optimising manufacturing process control and product quality with X-ray and ultrasonic inspection.
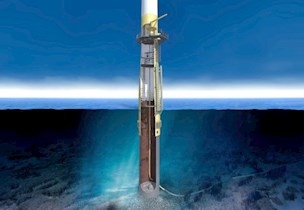
Cloud-based, automated ultrasound inspection
Automated, cloud-based ultrasound inspection reduces inspection time and secures data.
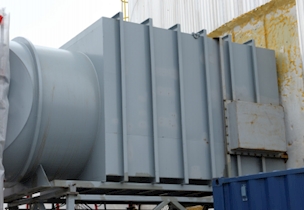
Ammonia tank inspection
In-service inspection of ammonia tanks provides a significant economical benefit.