Automated, x-ray guided laser welding is the secret behind the Ariane 6 rocket nozzle
When the Ariane 6 launcher made its maiden flight on July 9, 2024, it featured a new rocket nozzle design that had been developed with significant reductions in components and production time.
Long history and great expertise behind the development of Ariane 6 rocket nozzle
For more than two decades, FORCE Technology has participated in development projects for ESA, the European Space Agency. The latest addition is a new rocket nozzle concept where ESA demanded that it must be adaptable to various engines.
In addition, production costs and throughput time had to be significantly reduced without compromising dependability or operational reliability.
The space industry has the highest requirements for quality, performance and operational reliability, and there is a constant need for new innovative solutions.
”It is a privilege that FORCE Technology can participate in the project and bring our expertise and technological power of change into play," says Thomas Aaboe Jensen, program manager at FORCE Technology.
Additive manufacturing and laser technology contribute to exorbitant improvements
The development of the new design for the rocket nozzle was realised via additive manufacturing, laser welding technology and customised sensor technology that controls and guides the laser process.
The development work was performed in close co-operation with Swedish GKN Aerospace and in the process the cooperation developed into a professional partnership where FORCE Technology acted as a natural extension of the development department at GKN Aerospace. A ping pong of ideas often ended up being tested in practice at FORCE Technology’s unique facilities.
”We constructed a fully automatic production plant which first laser-welds approx. 1,400 cooling channels in the high-temperature resistant stainless steel and subsequently adds the necessary reinforcements using additive manufacturing,” says Thomas Aaboe Jensen.
The rocket nozzle has a diameter of 2.1 meter at its widest point and a height of 2.3 meter. The combination of the new design of the rocket nozzle and FORCE Technology’s new production method resulted in a 90% reduction in the number of sub-components, a 40% cost reduction, to a 30% reduction in production time.
In addition to many and different prototypes for testing during the development phase, FORCE Technology also delivered the sensor system for a new advanced production plant at GKN Aerospace, where future nozzles will be manufactured.
Knowledge must be brought to use in society and contribute to long-term development
FORCE Technology makes unique test facilities and specialist competences available to Danish companies to speed up the Danish innovation and strengthen the competitiveness of the companies.
”As a GTS institute, it is only natural for our newly developed concepts to be brought to use in industry in a broader context. We are therefore always willing to assist Danish companies if they can benefit from our knowledge and technology and thus contribute to the long-term development of society," says Thomas Aaboe Jensen from FORCE Technology.
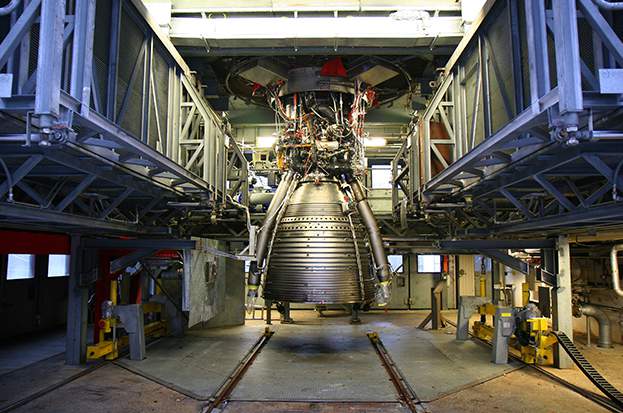
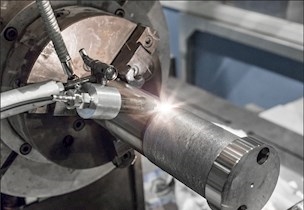
Laser welding is made available to the Danish industry
/Facility
Space technology
/Industry
Aerospace presents unique challenges for materials and equipment, to avoid accidents and loss of life.
Pyroshock and satellites
/Article
Before launch, a satellite's equipment must be tested for the effects of the launch.
Laser fusion, X-ray and ultrasonic equipment
/Facility
Our facilities are equipped with a broad variety of advanced production equipment.