Ammonia instead of oil: How an SME grew its green knowledge
Demands from customers are taking off. Betech can now document that a number of its gaskets are able to withstand liquid ammonia, a fossil-free alternative to oil in ship engines.
It all starts with the wind or the sun providing the energy needed to transform water into hydrogen. Nitrogen is added to the hydrogen, turning it into ammonia. The ammonia can then be used as a replacement for the oil that fuels ships. Ammonia is a fossil-free fuel that does not release CO2 during combustion. For these reasons, the use of ammonia as fuel constitutes a Power-to-X value chain of interest to the maritime sector in reducing its carbon footprint.
However, just like a real chain, a value chain is no stronger than its weakest link—and Betech, a small business that produces gaskets, seals, moulded rubber components, vibration dampers, and other technical products has tested two of its spiral-wound gaskets (also known as SWGs) to find out if they can support the green transformation. Testing was conducted as part of a MADE Demonstration Project with FORCE Technology.
"Today, these two gaskets are being used in flanges between pipes to supply fuel to traditional ship engines. This is relatively straightforward. Our question was whether we could use the same gaskets when we have ammonia flowing through the pipes, rather than oil. From a technical perspective, they ought to work, but we wanted documentation from a recognised institute like FORCE Technology"Bjarne Feddersen / Produkt lead Betech
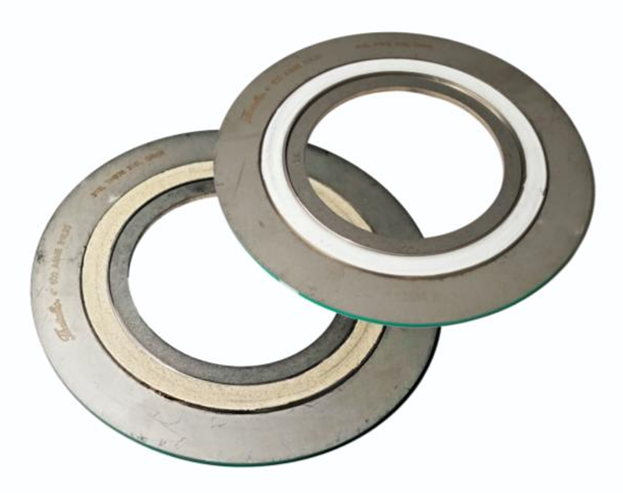
Betech had two SWGs tested for their ability to withstand liquid ammonia, a fossil-free alternative to oil in ship engines.
Testing standard and high-end products
Ammonia in a ship's fuel supply system must be pressurised to remain liquid, so the two spiral-wound gaskets were tested in accordance with industry standards that dictate the pressures, temperatures, and times that gaskets must be able to withstand.
"We built a test set-up with flanges to simulate a piping joint. Each gasket was exposed to ammonia at 20 bar and 60 degrees, as well as ammonia at 83 bar and 45 degrees, for 96 hours. The gaskets handled those conditions just fine," explains Jonas Greibe Hansen, a polymer specialist in FORCE Technology's Product Testing and Chemical Analysis department.
The test set-up would reveal any leaks if the gaskets failed under the test conditions. FORCE Technology also visually inspected the gaskets after testing. As expected, Betech passed the tests without issues. Both a standard product and a high-end product from Betech were tested.
"We sent both of them to be tested, so if our standard product failed and our high-end product passed, we would still be able to put an ammonia solution on the market," Feddersen says.
Building Power-to-X capabilities with a MADE project
Now, Betech has prepared itself for an emerging market.
"We've already received inquiries from subcontractors for major manufacturers that are developing ship engines for alternative fuels. Now, we can justifiably claim that we, too, offer reliable sealing solutions in this area. On top of that, the MADE project is important to us as a business because it helps us to build our capabilities in the field of Power-to-X fields, allowing us to maintain our position as the market matures," Feddersen explains.