With CFD simulations Chinese coal-fired power plant now complies with NOx emission regulations
A Chinese coal-fired power plant faced challenges with increasing NOx emissions, despite being equipped with a Selective Catalytic Reduction (SCR) system designed to reduce NOx emissions by at least 90%. In response to the regulatory compliance needs, FORCE Technology applied advanced Computational Fluid Dynamics (CFD) and Experimental Fluid Dynamics (EFD) techniques to optimize the SCR unit design, achieving regulatory compliance and substantial cost savings.
Challenge: Rising NOx emissions despite SCR installation
To meet statutory NOx emission limits, the power plant repeatedly increased ammonia injection levels, incurring significant costs. Investigations revealed severe erosion of the catalyst layer within the SCR unit, rendering it ineffective. Despite replacing the catalyst multiple times with assistance from three different subcontractors, the emission issue persisted.
A deeper analysis by FORCE Technology uncovered a critical discrepancy: the installed SCR unit's construction differed from its original design. Specifically, additional components, such as guide vanes, had been introduced, altering the flow dynamics and causing uneven gas distribution and catalyst erosion.
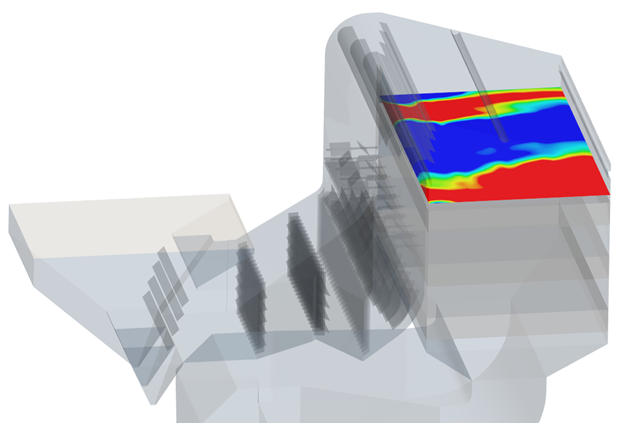
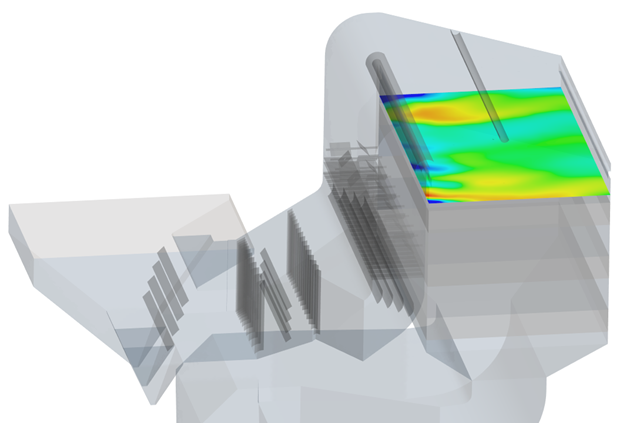
Solution: CFD modeling and redesign
FORCE Technology created a CFD model based on the actual installed SCR unit, simulating flue gas flow and identifying problem areas. The simulation results closely matched visual observations from the plant, confirming that high-velocity gas regions were eroding the catalyst layers and reducing performance.
Using these insights, FORCE Technology optimized the SCR unit design to ensure:
- Improved homogeneity: The redesign achieved a more uniform flue gas and ammonia mixture before reaching the catalyst layers.
- Simplified geometry: Adjustments, including streamlined guide vanes, reduced manufacturing and installation complexity while increasing catalyst efficiency.
- Reduced erosion risk: A balanced velocity field minimized high-velocity areas, extending catalyst lifespan.
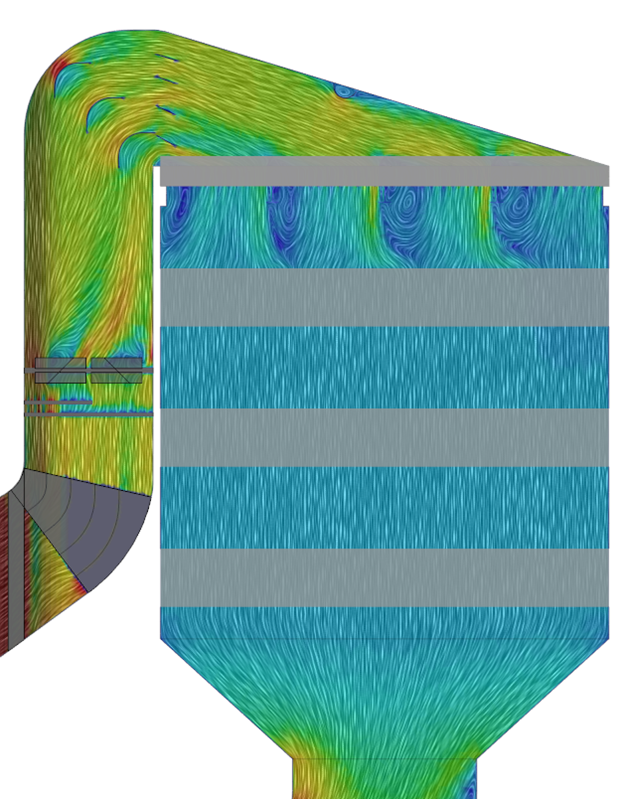
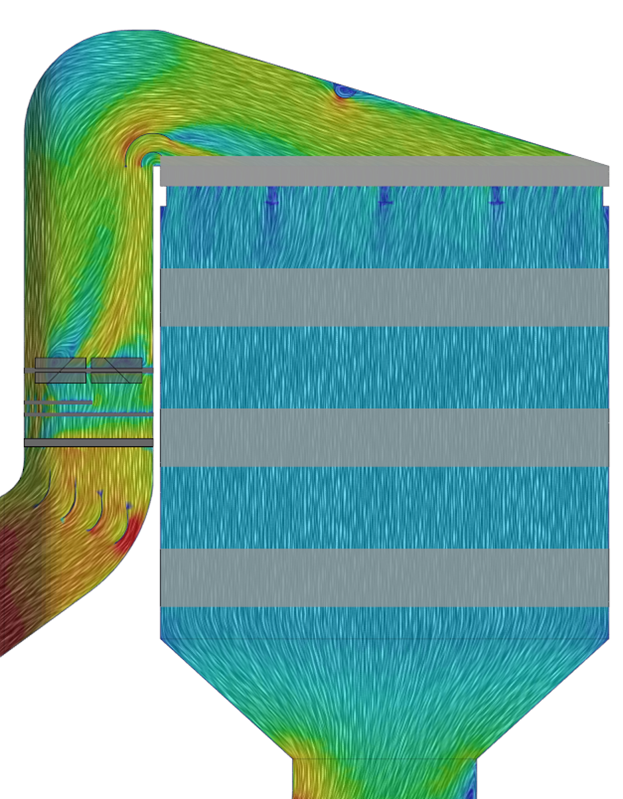
Validation with EFD
To validate the redesign, FORCE Technology constructed a 1:15 scale EFD model. This experimental testing confirmed that the optimized design would significantly enhance performance, reducing NOx emissions and ammonia consumption while ensuring compliance with environmental regulations.
Implementation and results
The redesigned SCR unit was implemented successfully. The plant now operates within the Chinese environmental regulatory limits, avoiding frequent and costly repairs. The streamlined guide vane setup and improved flow dynamics have also reduced operating expenses, including ammonia usage.
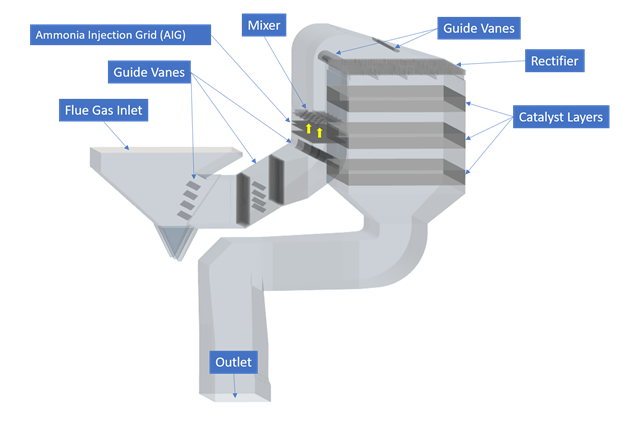