Corrosion tests help select the right well materials for onshore underground CO2 storage
Ensuring the safety of CO2 storage wells required precise corrosion testing for material reliability, leading to the selection of corrosion-resistant materials and enhancing the wells' integrity.
Pragmatic underground CO2 storage solution is a piece of the green transition puzzle
Underground CO2 storage was aimed as a pragmatic solution to mitigate emissions from hard-to-abate sectors such as heavy industry, where immediate and complete decarbonisation is challenging. Repurposing existing underground wells in Stenlille, Gas Storage Denmark is developing CO2RYLUS, Denmark could become first onshore CO2 storage facility.
Lack of textbook well corrosion data required new test protocol
The corrosivity of supercritical CO2 and formation water depends on reservoir chemistry. Since no textbook corrosion data is available for a scenario like the one in Stenlille, we planned and performed a series of corrosion tests within the CCUS partnership with Welltec A/S to assess the potentially corrosive effects of high-pressure CO2 and formation water on steel materials.
Simulated conditions in injection and monitoring well provided actionable results
Specialists within geophysics, geology, well design, plant operation and corrosion joined forces at two workshops to design two tests that simulated the conditions in the injection well and a monitoring well. The test performed by the Welltec Test Flow Loop team was set to simulate a long-term exposure of injector well materials to a large amount of formation water and supercritical CO2 containing impurities.
The test performed by the FORCE Technology team examined the galvanic effects in the well packer design. In short, the tests showed lower corrosion rates than anticipated, though there were some concerns regarding carbon steel corrosion. Consequently, Gas Storage Denmark opted for highly alloyed materials for modifications.
Interesting results obtained by both tests
- Supercritical CO2 caused corrosion of carbon steel, but due to the limited dissolution of water, the corrosion rate was low.
- CO2-saturated brine solution caused considerable corrosion of carbon steel, but at a lower rate than expected due to a strong pH-buffering effect.
- Stainless steel with 25 Cr resisted all tested conditions, including supercritical CO2 and oxygen-depleted brine solution, saturated with CO2.
- No obvious galvanic effects were observed between the stainless steel and carbon steel.
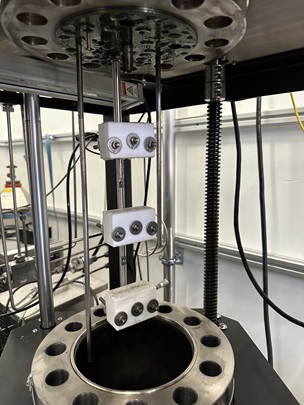
two weeks of exposure.
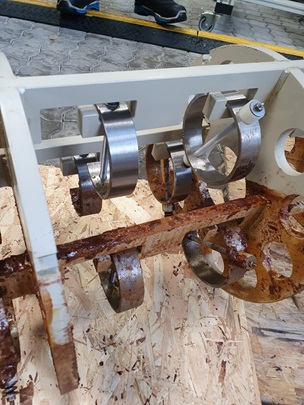
rack at Welltec’s facility after 4 weeks exposure partly to brine to formation
water + ScCO2 with impurities mixture and partly to only supercritical CO2 with
impurities.
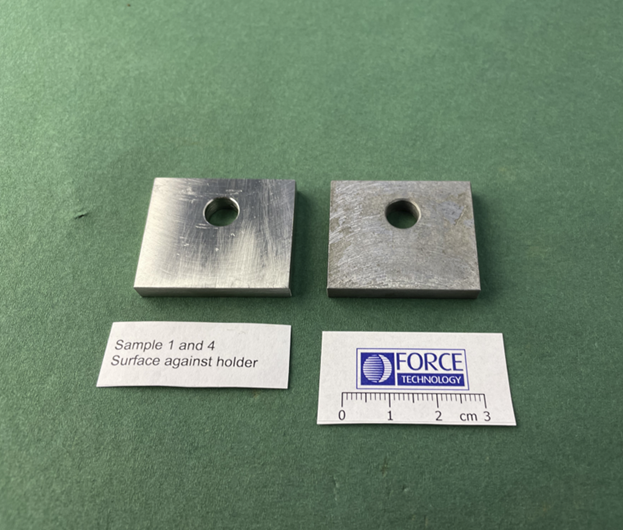
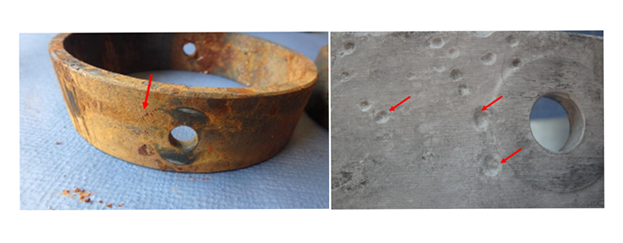
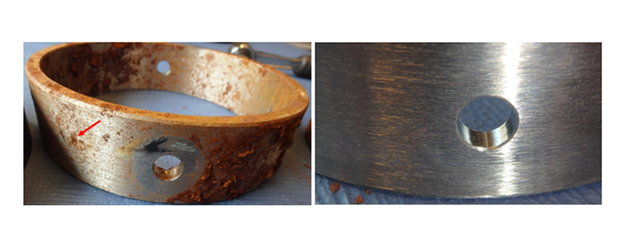
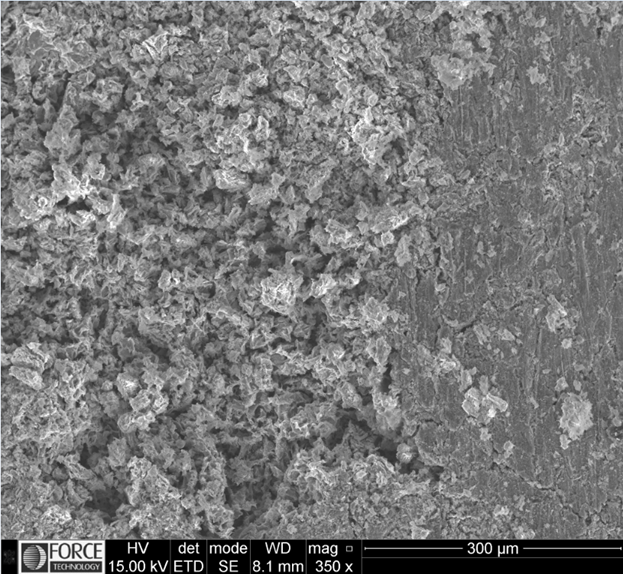
Partnership helps ensure the safety of underground CO2 storage infrastructure
"Given the novel opportunity of repurposing wells for underground CO2 storage at Stenlille, combining expertise to ensure safe usage and mitigate potential risks is imperative. This case exemplifies how complementary expertise working together can help ensure safety by designing customised tests that document the durability of well materials. Coming tests will simulate the conditions met in pipelines for CO2 at different impurity levels," FORCE Technology Materials Test and Analysis Specialist Troels Mathisen says.
"With complementary capabilities and a spirit of close collaboration, FORCE Technology and Welltec are perfectly positioned to deliver high-quality services for material and equipment testing. Simulations of true downhole CO2 environment can be quite challenging, and the combination of expertise in corrosion testing and an agile engineering mindset allows us to solve that puzzle", Kasper Holst Fornitz, Welltec's Technology Innovation Engineer for New Energy and Climate Technology department, says.
Welltec A/S is a global technology company that develops and provides efficient, hi-tech solutions for the energy industry.