Modern hull form optimisation using CFD leads to energy efficiency
CFD analysis is a fast and efficient tool to predict the performance of vessels before they are built and to optimise existing vessels. For Karstensens Skibsværft, this analysis is central in the design phase of new, energy-efficient vessels.
The Danish shipyard Karstensens Skibsværft has a long tradition of designing and building fishing vessels. To determine whether the dimensions of new designs of purser/trawlers are efficient, they use FORCE Technology’s experts to investigate the hydrodynamic efficiency of the hull design and optimise the hull lines.
Adjustment of the design within given constraints
To achieve an optimum design, parametric hull form optimisation is coupled with a modern and efficient RANS CFD solver. The hull lines will be varied based on parameter changes, steered by an optimisation routine to achieve the optimum design for a given operational profile.
It is essential that these adjustments are kept within the hydrodynamic constraints defined by the customer regarding displacement and stability of the vessel.
“Karstensens Skibsværft benefits from close cooperation with FORCE Technology when developing hull lines. Every new hull design is tested comprehensively with CFD analysis and evaluated with regard to other constraints such as displacement and draft,” says Kent Damgaard, Director, Karstensens Skibsværft.
Predicting the power demand
CFD calculations can simulate the flow around the ship and the free water surface, thus estimating the hull resistance and the power demand of the ship’s engine. Especially for high speeds, a crucial point for lowering the power demand of a vessel is to minimize its wave making and reduce flow-induced vortices.
During the CFD analysis for Karstensens Skibsværft, the experts examine:
- Wave-making of the vessel
- Pressure distribution along the ship hull
- Velocity distribution in the propeller plane
- Streamlines along the vessel and in the flow domain
Based on the CFD analysis, we provided Karstensens Skibsværft with suggestions for altering the vessel design so that the final power demand is reduced for the vessel’s operational condition.
Energy efficiency
The outcome of the CFD-based hull form optimisation is a hydrodynamically optimised ship design when it comes to energy efficiency but also in terms of lower fuel consumption. A recent example of a hull optimisation indicates that fuel savings of up to 7 % can be achieved.
These benefits are of great importance to Karstensens Skibsværft:
“CFD analysis and optimisation is a valuable tool to which we had no access 10 years ago. Karstensens Skibsværft finds it beneficial when coordinated with a detailed service profile for each design,” explains Kent Damgaard.
Perspective
CFD analysis is a relatively accurate and quick way to predict the performance of a ship design. It is well-suited in the design phase of vessels where hull form development plays an important role in achieving the optimum design.
For verification of the final ship design, it is a good idea to perform physical model tests in a towing tank. FORCE Technology has many years of experience performing different kinds of model tests in our towing tank, such as resistance, self-propulsion, seakeeping and manoeuvring tests.
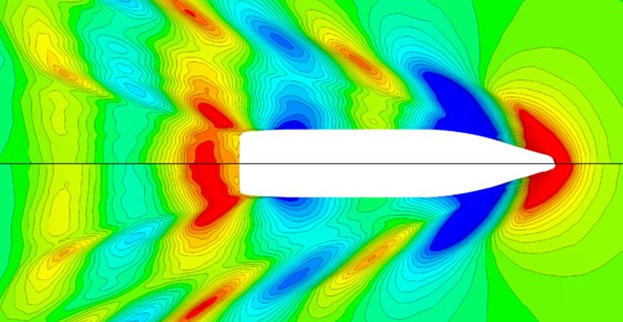