Digital twin enables better decision-making at dairy production facility
The digital twin helps Kold College's dairy training and production facility make smarter decisions and develop more intelligent procedures.
Lack of data increases cost and downtime
The lack of data and ability to predict performance and maintenance needs can lead to many things going wrong in a production process, causing increased costs or downtime.
Digital twin predicts production behaviour
A digital twin is a unique digital representation of a product with all its main features and characteristics. We co-created a digital twin of a pasteurisation plant connected to an IoT toolbox that collects data like temperatures from a plate heat exchanger. The data is sent to a simulation model that generates a point cloud that can be displayed on top of the physical machine with a tablet or AR glasses. Based on that simulation, you can see where biofilm forms (which you want to avoid when producing dairy products) and tweak the process accordingly.
Better safety, hygiene, resource-efficiency and training
At Kold College's production facility, the digital twin helps staff and students make smarter decisions and develop more intelligent procedures. It contributes to reducing costs and improving safety, hygiene and resource efficiency. Kold College also uses the digital twin to educate Nordic dairymen and -women.
You can use a digital twin to design, develop, manage and optimise the performance of any product or system.
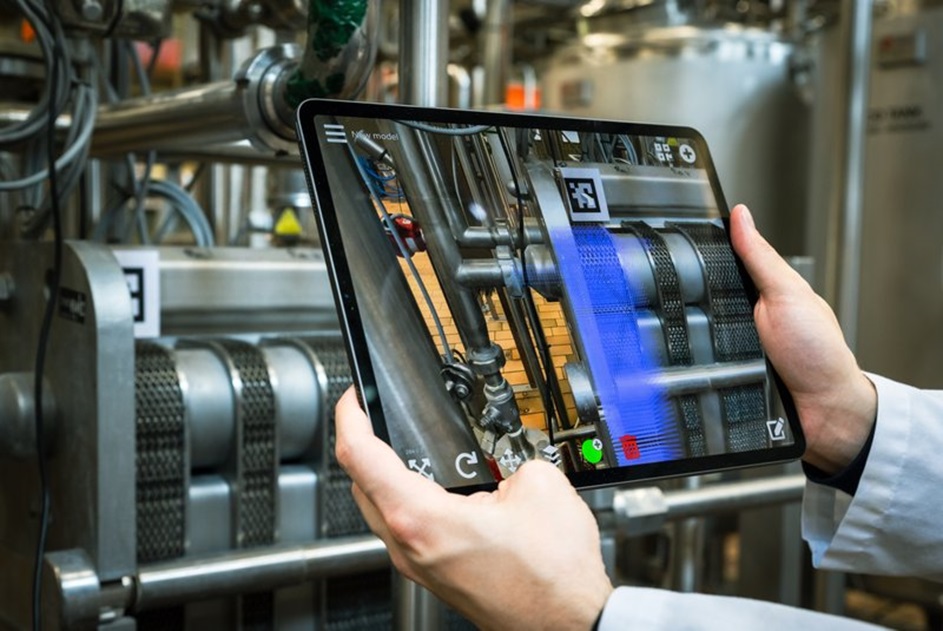
Learn more
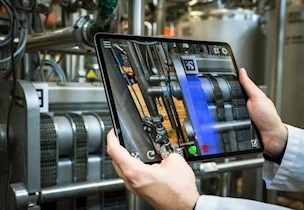
Digital and hybrid testing environments
/Page
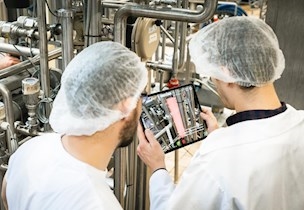
Digital twins
/Service