Digital and sustainable innovation in industry
Unlock the power of data and IoT technologies to optimize production processes and drive sustainable business growth.
Enhance operational efficiency and reduce environmental impact
We specialize in guiding companies through digital innovation, improving operations, and ensuring accurate data governance for sustainable development and safe critical infrastructure.
With expertise in both commercial services and research collaborations, we support the industry with a deep understanding of IoT and production - backed by the impartial perspective of a trusted research and technology institute.
Combine digital transformation with sustainability
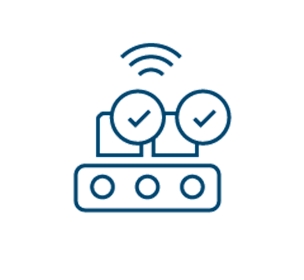
Digitalise production for sustainable innovation
/Service
Increase production efficiency, reduce costs and promote sustainability through digitalisation.
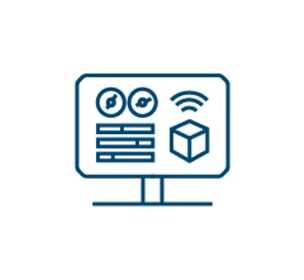
Get Data Quality - ensure data integrity
/Service
Achieve operational excellence in your data-driven processes.
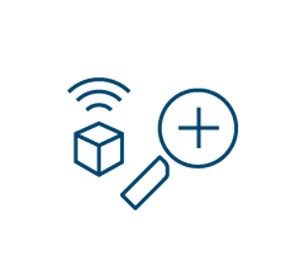
Smart technology advisory services
/Service
Identify, validate and evaluate digital technologies with us as your impartial partner.