Corrosion testing of materials and components for carbon capture and storage (CCS)
Corrosion testing in HPHT autoclaves is of significant importance prior to selecting materials for the infrastructure of the carbon capture and storage technology.
Restoring the balance of the natural carbon dioxide (CO2) cycle
With years and years of extracting and burning of fossil fuels the natural carbon dioxide (CO2) cycle of the Earth is out of balance. CCS is a viable technology to help restore the balance.
The CCS technology aims at capturing the CO2 from the atmosphere after the burning of coal, oil and gas. Once captured it must be compressed into liquid form or it exists as supercritical CO2. It is then transported to a long-term storage site which is often a suitable geological formation like a depleted oilfield. The liquified gas or supercritical CO2 may be transported by trucks, ships or in pipelines.
In order to develop the concept of CCS, plants and facilities must be built or remodeled to capture and liquify CO2. Besides, the infrastructure of pipes, pumps and injection wells for transportation and storage is needed.
Corrosion is a factor of great importance when designing new large-scale facilities
Bearing in mind that CO2 may exist in four different phases which are solid, liquid, gaseous, and supercritical, the proper handling of CO2 is crucial during CCS. Corrosion may easily appear in the various phases during capture, transport and storage.
Hence, when dealing with liquified or supercritical CO2 corrosion is a matter of great importance to bear in mind in the CCS planning phase. Thorough understanding of materials and environment interactions is vital when selecting materials for the carbon capture and storage technology.
Variables such as water and impurities need to be strictly controlled in order not to end up with materials that do not last long due to corrosion. It is very costly having to replace infrastructural parts of your CCS facility or perform unplanned maintenance offshore and it always results in significant downtime.
With supercritical CO2 the correct choice of materials is of utmost importance
If you choose the correct materials for the application from the beginning, you can prevent damage deriving from corrosion, wear and mechanical impact. Material selection is crucial to obtain a long service life and to avoid damage such as operation failure – for instance due to corrosion or inadequate mechanical strength.
You need to test your materials at supercritical conditions to make sure they can withstand the high temperature, the pressure and the aggressive environment they are to be used in. Often your CCS equipment has to tolerate up to 300 bar and at least 100 ˚C.
With High Pressure High Temperature (HPHT) facilities your materials prove their capabilities
With our HPHT facility we are able to assist you in selecting the optimum solution bearing both technical capabilities and financial aspects in mind. We can test your materials and components under the equivalent circumstances as when e.g. depositing CO2 in depleted oilfields.
The test equipment facilitates testing under supercritical conditions such as high pressure and high temperature testing in harsh environments (liquids and gases). We offer a large variety of techniques for examination of aqueous corrosion of metals, focusing especially on corrosion resistant alloys (CRA’s).
HPHT-Lab holds specialised equipment and facilities, to test your candidate materials:
- Pressure 0-350 bar
- Temperatures (25-350 °C)
- Hastelloy C-276 autoclaves, 7.5-liter capacity
- Flow simulation, stirrer or rotating cage (100-3000 rpm)
- Gas boosting system, CO2 and N2 (up to 350 bar)
- Possibility for dosing of chemicals and gas mixtures during testing
- Electrochemistry directly in the autoclave (HPHT reference electrode)
- Several coupon mounting options
- Standardised testing according to e.g. EN, ASTM and NACE.
After the test is performed, our specialists will examine the impact of the aggressive environment on the material and evaluate its performance and ability to resist corrosion.
Please contact us if you want to know more about our facilities or need help within CCS technologies.
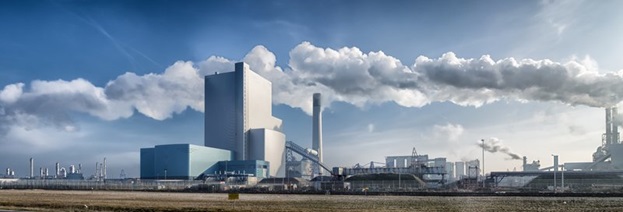