Materials selection and corrosion protection
You get the best conditions for keeping the functionality and appearance in the product´s service life by selecting the correct materials and the optimal corrosion protection.
By drawing on our unique combination of wide theoretical knowledge and practical experience of many years in the fields of metallurgy, corrosion and coating, you are certain of good results from the beginning.
Achieve a long service life with the correct choice of material
When you design your product, you put a lot of money, energy and consideration into achieving the best possible function, good appearance and high reliability. Corrosion, wear and fatigue resistance may not be the first factors you consider.However, material selection is crucial to obtain a long service life and to avoid damage such as operation failure – for instance due to inadequate mechanical strength - or unacceptable appearance due to corrosion products.
If you choose the correct materials for your product from the beginning, you can prevent damage deriving from corrosion, wear and mechanical impact. In many cases, you may completely avoid corrosion by choosing a resistant material for its actual application environment.
Alternatively, you can prevent corrosion by:
- Use of coating (paint, metallic coating)
- Cathodic protection
- Treating the attacking environment (water treatment, dehumidification).
Aggressive environment imposes very high demands on materials
All metals may corrode if the environment is sufficiently aggressive, and mechanical impact will often increase the risk of corrosion failure. In some industries, corrosion has been a challenge for many years, and they have well-established solutions while other industries experience an increasing number of problems because of:- New types of construction
- New combinations of materials
- Changes of the environment.
Examples of the latter are offshore wind turbines, power plants and equipment for extraction of oil and gas.
The price of the material often determines the price of a product, and therefore products are constantly optimised to save weight, materials and costs of processing. This means that the tolerance for corrosion, wear and mechanical impact is constantly reduced which is why all these factors should be considered and prevented in the design phase.
Choice of material is a multidisciplinary field, and our specialists include the state-of-the-art knowledge of:
- Metallurgy
- Mechanical properties
- Corrosion
- Coating
- Wear etc.
depending on the actual product.
If you consider replacing metallic components with parts made of plastic (polymers) or glass fibers (composites) to save weight or to obtain a lower price, we can be of assistance with information about requirements for the material so that the replacement becomes a success.
As an example of an industry that faces an escalating number of great challenges, we can mention the oil/gas industry. In the Danish part of the North Sea, many oil fields have reached an age at which the oil reserves are limited. This means that in many cases the produced liquids consist primarily of seawater with a small content of oil.
The large content of seawater results in increased corrosion of production facilities and may entail a completely inadequate product life and production shutdown, in an industry where production shutdowns are not acceptable.
Corrosion in oil-producing plants may be prevented by upgrading to more corrosion resistant materials (stainless steel, nickel alloys) or the corrosive environment may be treated with corrosion inhibitors or oxygen scavengers so that the traditional materials can still be used. FORCE Technology advises operators and suppliers of equipment in all phases of the projects.
Wrong choice of material influences product life
The wrong choice of material may cause failure of apparatus and production shutdown after a few months, even though the designed product life is many years. If you choose the wrong stainless steel for a product, or the steel is treated wrongly during welding or processing, it may corrode very quickly. Thus, a product with a designed product life of 20 years may only last a few months.
When you assess how new, advanced materials or innovative surface modifications will be capable of improving your product, we can help you find the optimal solution by a combination of knowledge, analysis techniques and tests.
If you include FORCE Technology in material selection, design review and consultancy on operations already in the planning phase, you can often avoid or minimise corrosion to an acceptable level. Our specialists have unique knowledge and many years of experience from many industries all over the world, and we can help you to avoid damage that might have been predicted.
It is often in the interface between different fields that standard solutions do not work, and here we can draw on our specialists in e.g. metallurgy, corrosion, concrete, plastics, chemical analyses and strength calculations. We give lectures at conferences and in professional networks both nationally and internationally, and we incessantly widen our knowledge and network.
Our expertise, width and international recognition often make us impartial experts appointed by the court. If the damage has already occurred, we can perform inspections and status assessments of the equipment and give advice on improvement of the construction, corrosion protection and operation so that future damage resulting from corrosion is minimised.
Examples of typical tasks involving choice of material and corrosion protection are:- Design review of new structures
- Design and monitoring of cathodic protection
- Preparation of painting specifications
- Failure analysis
- Chemical analyses of metals and coatings
- Consultancy on water treatment in heating and cooling plants
- Status assessment and control of corrosion on-site
- Test of corrosion and coatings
- Courses in materials and corrosion protection.
Downloads
- Brochure: Analysis and test of stainless steel
- Product sheet: FACT-Lab - test of materials in realistic environment
- Product sheet: Metallographic laboratory
- Product sheet: Process plants and stainless steel
- Paper: GfKORR Conference 2018 Corrosion issues and monitoring techniques for offshore wind turbine foundations
- Paper: Atmospheric plasma sparying of electrodes for conversion of electricity to hydrogen
- Paper: NACE Corrosion 2006 Corrosion problems in seawater pump caissons practical solutions
- Paper: Corrosion 2004 CP design of a super 13% CR flowline
- Paper: EUROCORR 2009 Influence of bacteria on silver dissolution from silver palladium surfaces
- Paper: EUROCORR 2009 Nickel and lead release to drinking water - Danish and European results
- Paper: EUROCORR 2010 Effect of material and water quality on disinfection and risks of corrosion
- Paper: EUROCORR 2011 Accelerated crevice corrosion testing of 6mo stainless steel flanges with different gasket materials in seawater
- Paper: EUROCORR 2011 Corrosion protection of offshore wind farm structures - Present understanding and future challenges
- Paper: EUROCORR 2011 Inspection and monitoring of corrosion inside monopile foundations for offshore wind turbines
- Paper: Corrosion 2004 Evaluation of impressed current system on fpsos by use of CP computer modelling
- Paper: NACE Corrosion 2006 Methods for cathodic protection of FPSOs - Where do we go?
- Paper: NACE Corrosion 2009 Corrosion aspects for stainless steel surfaces in the brewery, dairy, and pharmaceutical sectors
- Paper: NACE Corrosion 2009 Specifying stainless steel surfaces for the brewery dairy and pharmaceutical sectors
- Paper: NACE Corrosion 2013 Rapid corrosion test for detecting intermetallic phases in duplex stainless steels
- Paper: NACE Corrosion 2014 Challenges in pre qualification corrosion testing of CRAs based on ASTM G48
- Poster: Optical characterisation of nanostructures in embedded materials
- Paper: NACE Corrosion 2004 Optimizing of corrosion protection based on a combination of cathodic protection (CP) and coating
- Paper: NACE Corrosion 2007 Pitting corrosion resistance of electropolished seamless stainlesssteel tubes type EN 14404
- Paper: NACE Corrosion 2005 Problems in cooling water systems caused by poor design operation and water treatment
- Paper: NACE Corrosion 2003 Resistor controlled cathodic protection for stainless steels in chlorinated seawater
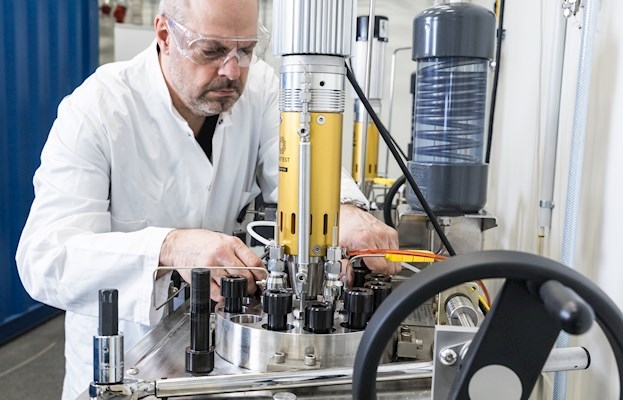
Facility