FROSIO-certified consultancy on specification for coating
How to ensure that your steel structure can withstand its future environment? FROSIO–certified inspectors assist you in selecting, documenting and performing an surface treatment.
Get FROSIO-certified (NS 476) specifications for the correct surface treatment
All constructions – small as well as large - are exposed to changing climate impact and corrosion, shortening their service life. The velocity of degradation depends on the environment to which the construction is exposed.
It is crucial to determine whether the surroundings constitute an indoor office climate, a moist factory building for e.g. foods, a hill in the countryside or at sea.
Paint and galvanization are widely used to protect the steel surface against corrosion attacks. The selected paint system and how the coating process progresses are very important if the construction is to be efficiently protected, for many years.
You have to choose which requirements to state in the specification. If the requirements are not sufficient, it will have consequences for the construction’s service life.
If they are too demanding – compared to what is necessary – it makes the coating unnecessarily more expensive and difficult to execute.
FORCE Technology’s specialists and FROSIO-certified (NS 476) inspectors may be of great value when determining which requirements to include.
- Requirements as per standards such as NORSOK M-501, ISO 12944, etc.
- Requirements for surface quality of steel – the degree of degradation that can be accepted before pre-treatment and coating
- Special requirements for steel type as to silicon content and material thickness to achieve the required zinc layer thickness by hot dip galvanising
- Which degree of pre-treatment should the steel have as regards welding and edges?
- After blast blasting, which degree of cleanliness is necessary for good adherence?
- How much salt is acceptable on the steel surface?
- What is the corrosion category?
- Which type of paint system should be selected?
- Is the proposal from the coating company well suited for its purpose, and which strengths and weaknesses does it have? Which degree of reporting and documentation should you require from the coating company?
- Which tests/inspections should be performed in the process as well as afterwards?
- How should the tests/inspections be performed? Internally by the customer or as a third party inspection?
- Acceptance criteria? Are there special requirements as to appearance? Easy-to-clean properties, colour fastness and visibility of repair?
Precise specifications provide expected results
The coating company must perform their work according to the specification. If there is no clear specification, they are right to do what they think best. However good practice is not the same everywhere.
Therefore, it is important to include everything in the specification. We typically base it on internationally recognised norms and standards for coating, for instance DS/EN ISO 12944, DS/EN ISO 1461 and NORSOK M-501. By specifying according to standards, the requirements become unambiguous.
Thus, the coating company knows that when you have specified e.g. P3 according to DS/EN ISO 8501-3, the welds must be burnished, must have no welding beads, and all edges must be rounded to a radius of 2 mm etc.
The coating company also knows that when you have specified the paint system C5.08 as per DS/EN ISO 12944:2018 , it requires a base coat with a zinc-rich primer with either epoxy, polyurethane or ethyl silicate as binder in a dry layer thickness of 60-80 µm.
Moreover, 2-3 coats of epoxy, polyurethane or acrylic should succeed it to a total dry layer thickness of 320 µm.
A good and precise specification ensures that your coating company knows exactly what you expect them to deliver. Thus, your steel construction - regardless of whether it is a wind turbine, a bridge, a tank or something else – is optimally protected against degradation by corrosion.
FORCE Technology’s specialists and FROSIO–certified inspectors (NS 476) provide you with impartial and professional sparring on selection of coating as well as requirements for execution and inspection of the coating.
A good specification based on international standards also ensures that in the case of disputes, nobody will doubt what you required originally.
FROSIO-certified inspectors
Becoming a FROSIO inspector is an internationally acknowledged education as per the Norwegian standard NS476, which includes 2 weeks training with final theoretical and practical exams. The course participant is subsequently granted a Level I-III, based on his or her level of experience, of which level III represents the most experienced participants. The course certificate must be renewed after 5 years.
In the NORSOK M-501 standard, this course certificate has been ranked alongside the NACE painting inspector education. The education includes corrosion protecting wet coating/varnishing and deals with quality assurance of all parts of the process from the starting point of the substrate to pre-treatment and selection of paints to the application of paint, inspection methods in practice and current valid standards in the field.
Impartial and specialised consultancy
FORCE Technology’s specialists and FROSIO–certified inspectors (NS 476) will give you impartial and professional sparring as to which coating/surface treatment to choose, and which requirements to set forth to your coating company as to application and inspection of the coating.
With an unambiguous specification, you get correct and long-lasting protection,
Feel free to contact us, and we will help you get it right.
Services
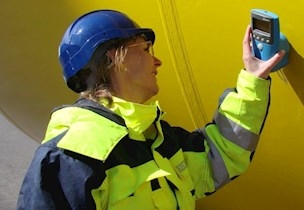
FROSIO-certified coating inspection
Make sure the surface finish on your steel structure is well done and remains intact and effective.
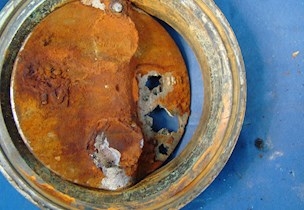
Corrosion and materials examinations
Corrosion and material data helps you in relation to design, product knowledge, and product failure.
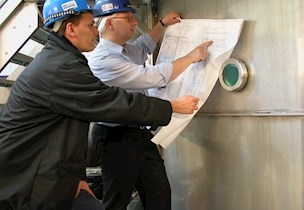
Organisation and planning of operation and maintenance
Avoid downtime and unexpected repair by organising and planning your maintenance.