Condition monitoring with non-destructive testing (NDT)
We use non-destructive testing to analyse the condition of objects, structures, and systems during operation. Gain insight into where to extend component lifetimes or repair components to avoid accidents.
We offer NDT inspection for all types of objects, structures, tanks, pipes and systems, whether onshore or offshore. This gives you critical insight into factors like corrosion, wear and tear, and other damage incurred during operation. You can then use this insight to optimise your maintenance operations.
Supporting safety, operations, and finances with NDT
As a system owner, you are responsible for the continuous monitoring and optimisation of your system.
This is true in multiple dimensions:
- Safety
Staying aware of your system's status is essential to ensure that it is safe for operators and other employees to work on or with the system. You must also ensure that the system complies with applicable regulatory requirements, and that the compliance is documentable to the authorities.
- Operation
Operation includes a variety of parameters. Above all else, this means minimising downtime and ensuring that the system runs as efficiently and smoothly as possible. If the system functions sub-optimally, the result may be additional cleaning expenses, emission taxes, and so on.
- Finances
Naturally, finances and optimum operation go hand in hand. An optimised system is subject to less wear, extending its lifetime. Continuously repairing and replacing individual system components as needed is also important to extend the lifetime of the system as a whole.
Specially tailored inspection and consultancy for valuable insights
There are multiple factors that influence wear, corrosion, and similar processes, including materials, the environment, loads, construction, and so on. This also means that determining the state of an object, structure, or system in operation can be much more complex than simply inspecting it immediately after manufacture.
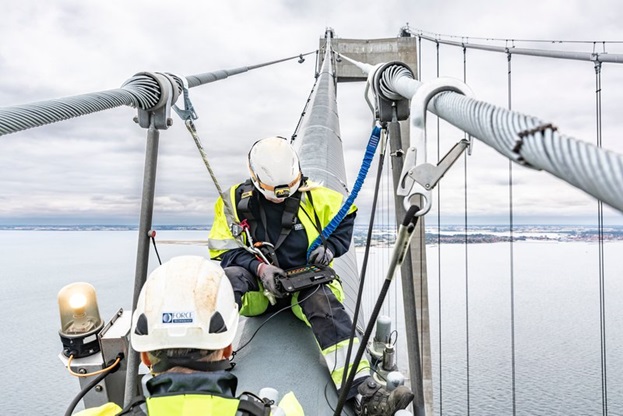
Consequently, we often use a combination of inspection methods in NDT tailored to the specific task at hand. These may include manual, automated, and advanced methods, including drone technology and rope access.
A versatile partner in condition monitoring
We have inspectors located in Denmark and around the world. Our regional offices enable us to rapidly respond in the event of a breakdown, accident, or other incident. This also means that our customers enjoy the convenience of having local contacts familiar with their particular facilities.
We work onshore and offshore, providing NDT inspection services to businesses in all industries; for example, food and pharmaceutical manufacturing, heavy industry, and energy - including CHP plants and wind power.
We work closely with in-house experts specialising in materials, fault mechanics, welding, and surface characteristics. That way, you can rest assured that we will always be able to find a solution to any problem that might occur.
NDT encompasses various non-destructive testing methods
NDT stands for non-destructive testing. We use all recognised NDT methods, including manual, automated, and advanced methods. Our comprehensive library of testing equipment enables us to use such non-destructive testing methods as
- visual inspection
- X-ray inspection
- ultrasonic testing
- vortex inspection
- penetrant inspection
- magnet inspection
- phased array
- digital radiography
- P-scan
- ToFD (Time of Flight Diffraction)
- 3D MFL (Magnetic Flux Leakage).
NDT is commonly used to inspect metals, concrete, polymers, and composites in industries ranging from energy generation, infrastructure, and transportation to pharmaceutical and food manufacturing.
Monitoring manufacturing processes with NDT
Incorporate NDT into your manufacturing to facilitate quality assurance and documentation for the materials, objects, and structures you deliver.
NDT methods - what are the most common NDT methods?
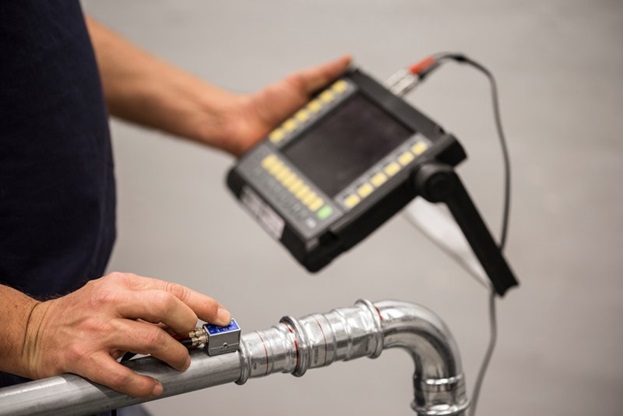