Monitoring manufacturing processes with non-destructive testing (NDT)
Incorporate non-destructive testing (NDT) into your manufacturing oversight to facilitate quality assurance and documentation for the materials, objects, and structures you deliver to your customers.
Non-destructive testing offers you the greatest insight into your manufacturing process and product quality, allowing you to guarantee and document compliance with internal and customer-supplied standards and requirements.
Our NDT-based manufacturing oversight services can help you to:
- Comply with established requirements and standards
Manufacturers of materials, objects, and structures are often subject to a variety of quality assurance requirements. These may include acceptance and rejection criteria set by customers or regulatory agencies in standards that your products must meet.
- Reduce the risk of manufacturing defects
By continuously monitoring the quality of your products using NDT, you can fix any issues that occur in the blink of an eye. This helps you to avoid customer complaints, unnecessary waste, and the need to dispose of defective products.
- Document product quality and uniformity
You may additionally be subject to internal or customer-supplied requirements for product quality and uniformity. Uniformly high quality is often a point of competition for manufacturers, so your ability to document this credibly and impartially is critical.
- Inspect welds and joints
Whether you manufacture objects, systems, or structures, there are often critical points that can impact properties related to safety and product lifetimes. Typical examples include joints like welds, which can become weak points if defects occur in them during manufacturing.
Flexible, NDT-based manufacturing process control tailored to your operation
Looking at a product from the outside may not be enough to tell if it was manufactured or welded correctly. Non-destructive testing lets us look inside a product or weld to determine whether it meets agreed-upon standards or requirements.
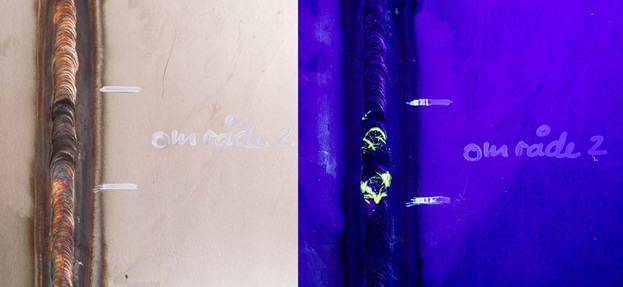
We adapt our inspection services to your needs based on a variety of parameters. This means that we choose approaches and methods based on such factors as materials, construction, and accessibility, as well as based on customer-supplied or government-mandated documentation requirements you may be subject to.
NDT encompasses various non-destructive testing methods
NDT stands for non-destructive testing. We use all recognised NDT methods, including manual, automated, and advanced methods. Our comprehensive library of testing equipment enables us to use such non-destructive testing methods as
- visual inspection
- X-ray inspection
- ultrasonic testing
- vortex inspection
- penetrant inspection
- magnet inspection
- phased array
- digital radiography
- P-scan
- ToFD (Time of Flight Diffraction)
- 3D MFL (Magnetic Flux Leakage).
NDT is commonly used to inspect metals, concrete, polymers, and composites in industries ranging from energy generation and transportation to pharmaceutical and food manufacturing.
In addition to manufacturing process control, we also use NDT to inspect objects, systems, and structures that are already in operation. Condition monitoring using NDT methods gives you insight into the condition of your system, so you know what to do to extend its lifetime.
Condition monitoring with non-destructive testing (NDT)
We use NDT to analyse the condition of objects, structures, and systems during operation to understand where to extend component lifetimes or conduct repairs.