The advantage of automated Hull Line Optimisation
Depending on the project stage and hull form development, it is either important to focus on main design parameters, such as LPP, breadth and volume distribution, or to concentrate in detail on local areas such as the bulbous bow, transom or the skeg design.
Much optimisation work can be done manually based on experience, but keeping an overview of the performance of many design variants in several operational conditions and making the right hull form deformations while simultaneously satisfying design constraints on for instance LCB, displacement and tank and thruster tunnel arrangements is quite difficult without some sort of automation.
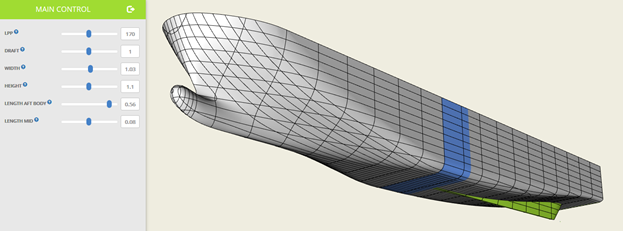
To ensure a qualitative hull line optimisation, we rely on our long-term experience within CFD applications using CFD tools and procedures that are well proven and continuously checked against towing tank tests in all projects involving both CFD and tank tests.
What to optimise for?
In many cases, it is sufficient to optimise ship hull lines for the lowest resistance as the wave making reflects the major part in the power consumption. But to estimate the influence of hull form changes on the stern flow properties and the propulsive performance qualitatively, the effect of propulsion on the flow has to be accounted for.
FORCE Technology takes hull form optimisation to the next level by incorporating simplified approaches that allow the optimisation to use propulsive power as the objective. By using this method, it is possible to work with both reduction of the resistance and improvement of the propulsive efficiency based on CFD results, propeller open-water data and information from our large database with model test results.Does it make sense to optimise for one design point?
Many hull forms are designed and optimised for operation at one speed and one draught. In reality, however, many ship types are not constantly operating at the design point since the speed and loading conditions vary during operation.
Operational data has been incorporated in the optimisation process. Hull lines will be optimised to show better resistance and propulsive characteristics over the entire operational profile which will help the shipowner to reduce the fuel cost during operation.
We have been involved in a large number of optimisation assignments with good results. When looking at the ship's performance, it is not unusual to see that the resistance and power consumption, on average over the operational profile, have been reduced by 3 to 7% between initial and final designs.
As the estimated saving is typically used as the basis for evaluation of a business case which is used to judge if a design change is profitable, it is important that the accuracy of the estimated saving is reliable. Our CFD-based saving predictions are in good agreement with the savings measured by physical model tests.