Danish companies' impending need for hybrid test beds
Research has shown that Danish companies have growing needs for hybrid testing. However, a lack of in-house expertise and immature technologies have stood in the way of its implementation.
Access to testing, development, and demonstration facilities is crucial for Danish businesses to continue developing and launching competitive products that create jobs and boost exports.
Denmark as a leader in testing
The Research Alliance, a collaboration between Danish Metal, DI, the Danish Academy of Technical Sciences (ATV), and the Danish Society of Engineers (IDA), is working to increase public funding for research. In an opinion piece published in Altinget, the alliance highlights the need for Denmark to be a global leader in testing. This would create an unbroken chain from initial research through to testing and product demonstration in the country.
The release of a new digital map featuring 400-odd Danish testing facilities is just one initiative aimed at helping Danish businesses find their way. The digital map distinguishes between physical and virtual testing facilities, underscoring the relevance of a hybrid approach to testing.
Research reveals companies' testing needs
To position itself at the forefront of these developments, FORCE Technology conducted research in autumn 2021 to discover what Danish manufacturers associate with hybrid testing and what needs they expect to have in this area in the future. This research was conducted under the auspices of the "Hybrid Test Beds of the Future" project, which is funded by grants from the Danish Agency for Higher Education and Science.
The study revealed a clear tendency for companies to overwhelmingly opt for physical testing facilities today, though they expect an increased need for hybrid product testing methods within the next five years. The study also found a number of challenges that business face in integrating hybrid methods into their product testing workflows.
What are hybrid test beds, and what role can they play in product testing?
A generic idea of traditional product testing served as a starting point for this study. This idea can be broken down into three main areas:
- Testing products at physical testing facilities
- Virtual, simulation-based testing
- Testing products in operation.
By combining these testing methods with digital technologies like IoT, ML, and digital twins, hybrid testing methods become possible not only in terms of the technologies used, but also in terms of how data is used throughout a product's life cycle.
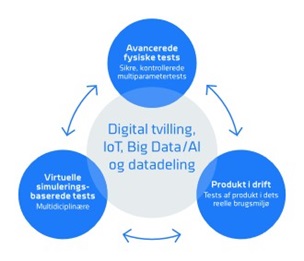
Thus far, the study has identified several situations in which hybrid testing can be highly valuable, outside of areas where its use creates challenges.
"So far, our research has shown that hybrid testing can be challenging to use in product approval contexts that are subject to requirements and standards," explains FORCE Technology's project manager for the "Hybrid Test Beds of the Future" project.
"On the other hand, there is evidence to suggest that there are major savings to be had in cases where a prototype, test subject, or product is so large as to be difficult to test in a full-scale physical testing facility," he says.
"We've also seen a need to test individual components early on by simulating more realistic boundary conditions and observing interactions between the product and the environment. This way, manufacturers can be more certain that their components function and interact as expected in the finished product," he adds.
Danish companies expect more hybrid testing solutions
The study shows clear expectations for a shift from primarily physical testing to more digital and virtual testing as a complement to physical testing - that is, hybrid testing (see Figure 1).
"In my opinion, we're seeing this shift towards more digital testing methods because businesses are being pressured to get onto the market faster and with greater confidence. The traditional 'trial and error' approach is time-consuming and costly in terms of man-hours and engineers alike," says the project manager.
"A more hybrid, more digital approach to product development allows a business to achieve a shorter time-to-market, and costly physical prototypes are replaced with computerised testing. That way, the business's investments and employees - often its most critical resource - can scale a lot better."
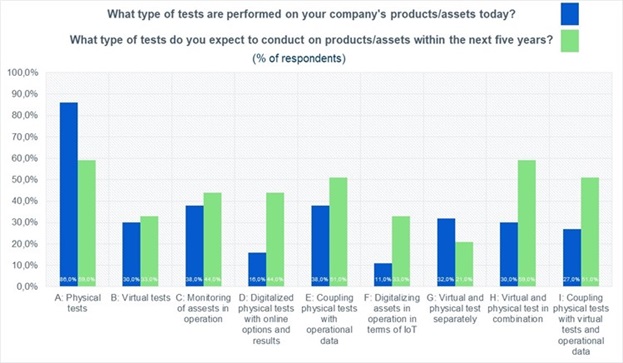
Potential barriers to implementing hybrid testing
The study has found that the largest barrier to hybrid testing is companies' lack of in-house expertise and resources needed to implement this approach (see Figure 2). Additionally, the immaturity of this technology is an issue for many businesses.
"The lack of maturity as a barrier likely has to do with the use of broad terms like 'hybrid testing' and 'digital twins,' which promise all kinds of opportunities, while the reality is that there are only limited use cases and demonstrators. It can be difficult to evaluate the maturity of any technology before it's been demonstrated and accepted by the industry to a certain extent. This is one of the reasons that demonstration cases with real businesses are a key component of this project," the project manager explains.
"Companies' lack of familiarity with hybrid testing is a real challenge, and that's something we want to look into changing with this project.
Digitalisation and data sharing are a big part of hybrid testing, so this technology also makes collaboration with external testing centres like GTS businesses possible. That enables businesses to draw on external expertise."
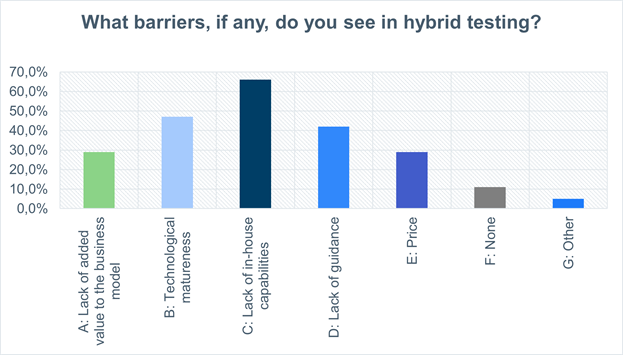
In the long term, there may also be a need to push the standards in this area. In many cases, standards call for particular tests to be performed. However, if it turns out that the same result can be achieved through a combination of physical and virtual testing, hybrid testing may become an option for certification in the future.
For this to happen, simulations must become as reliable as possible. Standardising simulations would also build trust in them among businesses.
Hybrid test beds: creating value in the future of testing
According to the study, more than 80% of the companies surveyed believe that hybrid testing will create value for them. Specifically, they see value in gaining greater knowledge of their products and insight into product quality. Moreover, reducing the number of physical tests required and replacing them with digital simulations can reduce times to market.
In the case of digital data collection from products in operation, businesses and technology vendors are able to see how products are actually used versus how they were intended to be used. This way, they gain insight into needs for future development and improvement.
In the words of the project manager, "There's no doubt that access to data about products, their usage, and their performance is a real gold mine for some businesses. Having that makes new business models possible, as we're seeing in servitisation."
"That data also comes with knowledge of how simulations and digital models used in design and development compare to reality. Then, we and other businesses can take that data, apply machine learning to it, and use it to improve the precision and reliability of the original models," concludes FORCE Technology's project manager.
Real interest and real needs for hybrid test beds
The study has concluded that Danish manufacturing businesses are interested in, and have a need for, hybrid test beds for future product testing. That said, they also need the know-how and expertise to implement hybrid testing solutions in development and manufacturing, plus the physical testing facilities required to apply them.
One of the project's primary focuses is on maturing technologies and offering up-to-date guidance for hybrid testing, including measures to support businesses' in-house expertise. Currently, the project is researching the value of a professional network and/or courses arranged in collaboration with universities to bolster companies' expertise in this area.
Demonstration projects with businesses will assist in the development of the more technically orientated tools, and the flexible nature of the project means that businesses interested in collaborating on these projects in 2023 and 2024 can still apply to join and gain access to the latest knowledge and input on hybrid testing methods.