Understanding photobiological safety: Key insights for manufacturing systems integrators
As a manufacturing systems integrator, ensuring photobiological safety is crucial when integrating light sources into your systems to avoid harmful exposure to UV, IR, and intense visible light.
Photobiological safety is crucial for light source manufacturers and those who integrate these into broader systems such as production lines, Machine Vision setups, lamp installations, and UV applications. For manufacturing systems integrators, understanding the risks to operators and personnel is essential to ensure the safe operation of these systems and maintain compliance with industry standards.
Why photobiological safety matters in manufacturing systems integration
Light sources, especially those emitting UV, IR, and high-intensity visible light, can pose significant risks to humans if not properly managed. Overexposure to harmful light can lead to severe health effects, including retinal damage, skin burns, and eye injuries. It is essential to mitigate these risks through comprehensive testing and safety assessments.
Steps for ensuring compliance with EN/IEC 62471
- Risk assessment: The first step is to thoroughly assess the light sources used in your systems. This involves identifying potential hazards, such as UV or blue light exposure (Blue-Light hazard) and evaluating the level of risk to operators and personnel.
- Compliance testing: Once risks are identified, working with accredited laboratories to test the systems according to EN/IEC 62471 is essential. This testing helps verify that the systems meet safety standards and are safe for use in your intended applications.
- Proper labelling: Ensure all systems are labelled with appropriate warnings and compliance marks after testing. This not only informs users of potential risks but also demonstrates that the systems meet required safety standards.
- Continuous monitoring: Photobiological safety is not a one-time consideration. As technology evolves and new light sources are integrated into systems, it's crucial to regularly reassess and test these systems to ensure ongoing compliance with safety standards.
Applications and their challenges for manufacturing systems integrators
Photobiological safety is a critical consideration across numerous systems where light sources play a key role. However, achieving both safety and performance can be challenging. Manufacturing systems integrators must balance the need for high-performing light sources with the stringent safety standards requirements.
Below are some of the systems where these challenges are most prominent:
- Production systems
- Surface inspection systems
- Colour quality control
- Machine vision
- UV disinfection sites
- UV curing systems
Adequate lighting that meets photobiological safety standards in production systems
Light sources in production systems are primarily used for general illumination and specific tasks such as assembly, inspection, or safety in a manufacturing environment. The focus is on providing consistent, adequate lighting across large areas to ensure operators' safety and efficiency.
The challenge lies in selecting light sources that deliver the required brightness and coverage while meeting photobiological safety standards. This often requires a trade-off between performance and safety, necessitating careful calibration and shielding to protect workers without compromising the system's functionality.
Necessary precision of light sources is needed for surface inspection systems
Surface inspection systems utilise advanced lighting techniques to detect and analyse surface defects such as scratches, dents, and discolouration on materials like metals, glass, and plastics. These systems require high-intensity, uniform illumination to ensure even the smallest imperfections are visible.
The challenge is to maintain this level of precision while ensuring that the light sources comply with photobiological safety standards, protecting operators who may work close to these intense light sources for extended periods.
Colour quality control relies on safe and controlled lighting environments
In textiles, automotive, and printing industries, precise colour matching and quality control are critical to maintaining product consistency. These systems rely on specific lamps to reproduce and verify colours accurately.
Achieving this requires highly controlled lighting environments, often involving multiple light sources to simulate different conditions. However, using intense, specialised lighting over prolonged periods can pose risks to personnel.
Machine Vision requires intense specialised lighting safe for personnel
In contrast to general production lighting, Machine Vision systems rely on highly controlled, focused lighting to enhance contrast and reveal details during automated inspection processes. The performance of these systems depends heavily on the quality and intensity of the light sources used. The light sources must be precisely tuned to the vision system's specific needs, often requiring specific wavelengths, intensities, and uniformity to capture images for analysis accurately.
However, maintaining photobiological safety for operators working near these systems can be challenging, especially when the required light intensity is high and potentially invisible (IR). Manufacturing systems integrators must ensure that the light sources meet the necessary photobiological safety standards without diminishing the effectiveness of the vision system.
UV disinfection sites must be powerful enough and still protect workers from harmful exposure
UV light is widely used for its germicidal properties in hospitals, laboratories, and water treatment facilities. The challenge here is to maximise the disinfection efficacy of UV light while protecting personnel from harmful exposure. UV light sources must be powerful enough to destroy pathogens and include safeguards such as timers, sensors, and protective shielding to prevent accidental exposure.
Manufacturing systems integrators must navigate the complexities of ensuring that these systems meet both the performance specifications for effective disinfection and the strict safety requirements to protect human operators.
Manufacturing systems integrators must implement safety measures in UV curing systems
UV light is also widely used for adhesives, coatings, and inks in curing systems. These systems require high-intensity UV light to quickly cure materials, which enhances production efficiency. However, the challenge is ensuring operators are not exposed to harmful UV radiation during the curing process. Manufacturing systems integrators must implement safety measures such as protective shielding, interlocks, and proper ventilation to prevent accidental exposure while maintaining the performance of the curing process.
Regulations and standards for photobiological safety
Compliance with the EN/IEC 62471:2008 standard is essential for ensuring photobiological safety in light source integration. This standard, required under the Low Voltage Directive 2014/35/EU, is crucial for assessing the potential hazards of optical radiation emitted by light sources.
Compliance ensures that integrated systems are safe for end-users, particularly in industrial and commercial applications where operators are directly exposed to these light sources. Securing CE marking for products within the European market is a mandatory requirement for product distribution and includes compliance with these standards.
Manufacturing systems integrators must protect users and ensure compliance with photobiological safety standards
For manufacturing systems integrators, understanding and implementing photobiological safety standards is not just a regulatory requirement—it's a responsibility to protect users, operators, and the integrity of the systems they design.
Whether integrating light sources into medical equipment, production systems, or commercial spaces, ensuring compliance with photobiological safety standards is essential. This approach safeguards health and enhances the reliability and trustworthiness of the systems in which these light sources are used.
By staying informed and proactively managing risks, manufacturing systems integrators can create safer, more effective systems across various applications.
Please do not hesitate to contact us if you need further information on ensuring photobiological safety in manufacturing integration systems.
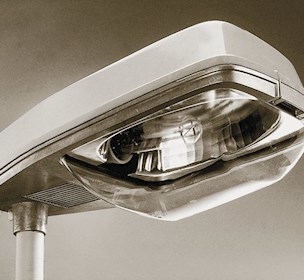
Accredited test of photobiological safety
/Service
Requirements for documenting photobiological safety of products with visible light, IR, and UV.
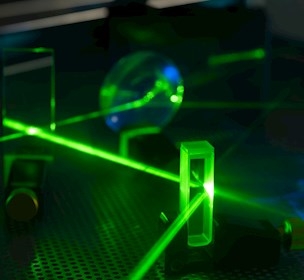
Photonics, light, and optics laboratories
/Facility
Accredited testing of e.g. sensors, light sources, lighting products and retroreflective materials.
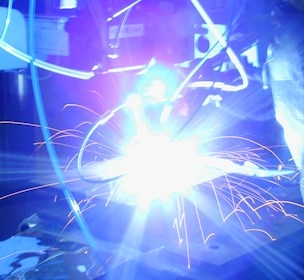
Laser safety - get the necessary risk assessment
/Service
Lasers are subject to EU directives and AT's regulation, and require regulatory risk assessment.