Kvasir's carbon-neutral fuel: a revolution in maritime transportation
At its testing facility, Kvasir has begun producing a carbon-neutral fuel for ships. Now, the company wants to scale up production. How can it do so profitably while guarding against corrosion?
With goods and passengers in constant motion across the world's oceans, the maritime transportation industry is one of the largest greenhouse gas emitters. But what if it were possible to produce a fuel for ships that had no impact on the atmosphere's CO2 content? This is exactly what Kvasir Technologies, a small Danish company, set out to do.
Replacing fossil fuels with biofuels in maritime transportation
Kvasir Technologies has developed a specialised technology for producing crude bio-oil which leverages the large quantities of waste generated by agriculture and forestry operations throughout the world. This bio-oil may eventually replace fossil oils as fuels for heavy transportation operations.
"We're converting inedible biomass, such as straw, into biofuel for ships. We pressure-cook the biomass in alcohol at 400 degrees," says Joachim Bachmann Nielsen, executive director and co-founder of Kvasir Technologies.
"We've successfully demonstrated that it is possible to produce crude bio-oil in experimental autoclaves and a pilot set-up using stainless steel and nickel alloys. In scaling up the technology, we want to find more affordable materials for a full-scale facility to ensure that our process remains among the most cost-effective.
However, we need to choose materials that minimise the risk of corrosion, wear, and cracking, which can occur due to the high temperatures involved and potential impurities in the biomass being processed."
Can surface treatments keep costs down for a full-scale facility?
In a knowledge bridge project entitled "Materials for Extracting Crude Bio-Oil," supported by Energy Cluster, Kvasir Technologies collaborated with TRD Surfaces ApS and FORCE Technology to study the breakdown mechanisms that impact steel and nickel alloys. The project's participants also investigated methods for measuring corrosion, optimising materials, and thereby finding the materials that are best suited to use in a full-scale facility.
"We needed to find a solution that was just as resistant to corrosion, wear, and cracking as our experimental set-up, but preferably at a much lower price point," Nielsen explains.
This is where TRD Surfaces ApS, a small business that produces wear-resistant and corrosion-resistant surface treatments, came into the picture. TRD Surfaces provided two high-chromium steel surfaces for testing in the experimental autoclaves.
"We expected that our surfaces would be effective in the atmospheres they were exposed to in the project. When we looked at the treated surfaces after testing, it was clear that they had superior corrosion resistance," says Mads Brink Laursen, CEO of TRD Surfaces ApS.
Incorporating material selection into the design phase at Kvasir
To test a variety of solutions, FORCE Technology developed a corrosion test in which small pieces of treated and untreated metal, also called "corrosion coupons," were placed in an experimental autoclave and exposed to the harsh environment inside. The results demonstrated that it is possible to significantly reduce the cost of the materials needed for the processing facility by treating the metal surfaces with solutions from TRD Surfaces.
"The results of the corrosion measurements clearly showed a major difference between the samples. That made us more aware of how important it is to address this issue starting in the development phase, so we can consider material choices and surface treatments in the design phase," Nielsen explains.
Opening doors and attracting investors
The project created a bridge of knowledge between the participants, and both small businesses see a bright future ahead of them.
"For us, the project validated the effectiveness of our surfaces in a new market segment. We can use that knowledge and the project's results to open doors to new development projects," says Laursen. "This is a new area for us, and we've gained valuable knowledge regarding stress corrosion and our surface treatments. On top of that, it's always exciting to be at the forefront of technological developments and to build relationships with new potential partners," he adds. Laursen is the CEO of TRD Surfaces ApS.
The project showed that corrosion coupon exposure testing is especially valuable when corrosion data for a particular process, such as Kvasir's, is unavailable. As a result, Kvasir intends to incorporate corrosion coupons into its next facility, both to further optimise material selections and to continuously monitor the state of corrosion in the facility.
There are considerable savings to be had from using low-alloy, surface-treated materials, and by minimising the risk of corrosion and damage to the facility, it'll be easier for us to attract investors.Joachim Bachmann Nielsen, CEO and co-founder / Kvasir Technologies
With this project in the books, the company is now even closer to producing a maritime biofuel that can compete with fossil oil.
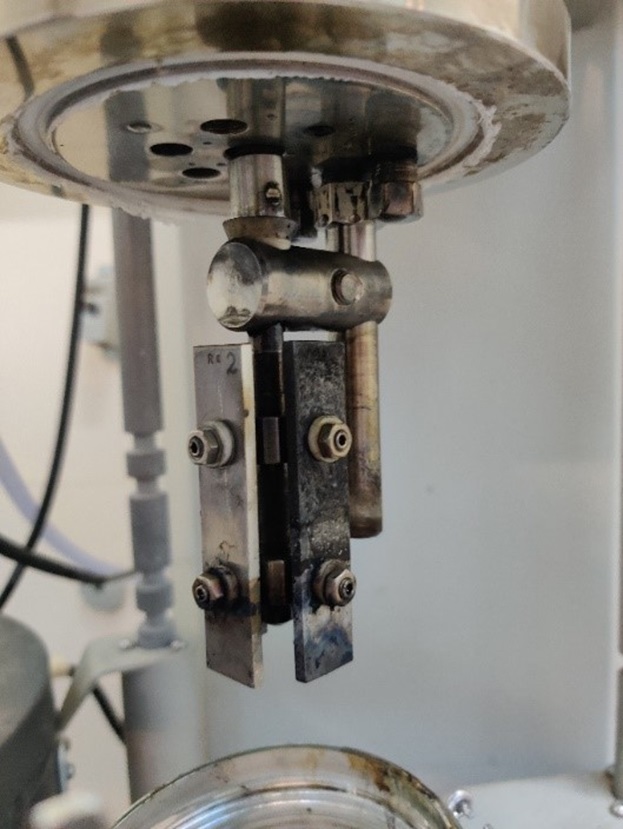
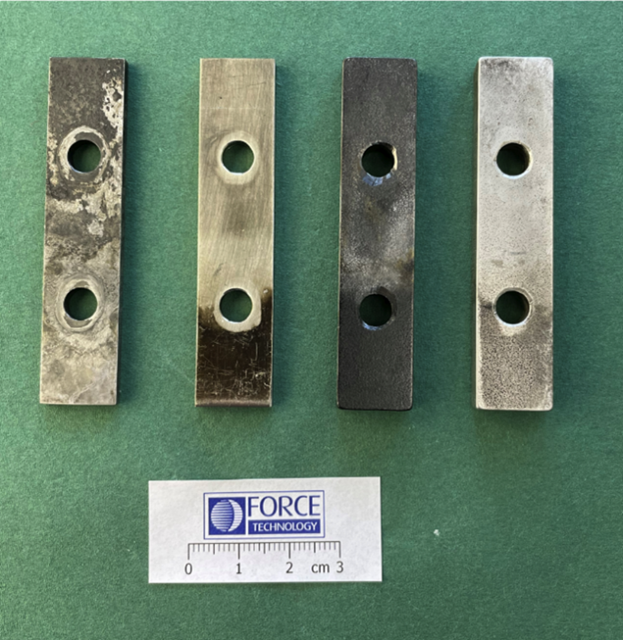