Material analysis confirmed why Letbek's recycled plastic ground protection mats were cracking
Letbek saw that recycled plastic with a high polypropylene content weakens ground protection mats. Material testing and characterisation helped improve quality, reduce waste and minimise complaints.
Since the 1970s, Letbek has worked with plastic recycling, treating plastics as a circular resource used across product categories such as pipes, covers and designer furniture.
Known issue with recycled plastic confirmed
Letbek manufactures ground protection mats from recycled polyethylene (PE), but had experienced cases of the mats cracking, particularly during cold weather.
As part of the REVMAT project (Reverse Material & Product Requirement Planning), Letbek had the opportunity to investigate the cause of the issue, which they had already suspected. REVMAT is an Innomission project funded by Innovation Fund Denmark and managed by TRACE.
“We were aware that high polypropylene (PP) content might be the cause, as much recycled PE contains small amounts of PP, but we didn’t know the actual threshold,” says Louise Aagaard Jensen, materials specialist at Letbek.
Material analysis revealed a critical mix ratio in recycled plastic
With support from FORCE Technology, Letbek carried out a thorough analysis and characterisation of their recycled plastic. Using Thermogravimetric Analysis (TGA) and Differential Scanning Calorimetry (DSC), samples from Letbek were tested for their PP and PE content, both from batches where mats held up and where they failed.
“We don’t have that type of equipment, so we’re not able to analyse the exact composition of the plastic batches we receive,” explains Louise Aagaard Jensen.
The material analysis clearly showed that mats with more than 10% PP typically cracked, while those that remained intact contained less than 6% PP.
“It was a relief to have our suspicions confirmed – and now we have specific thresholds to work with,” says Louise Aagaard Jensen.
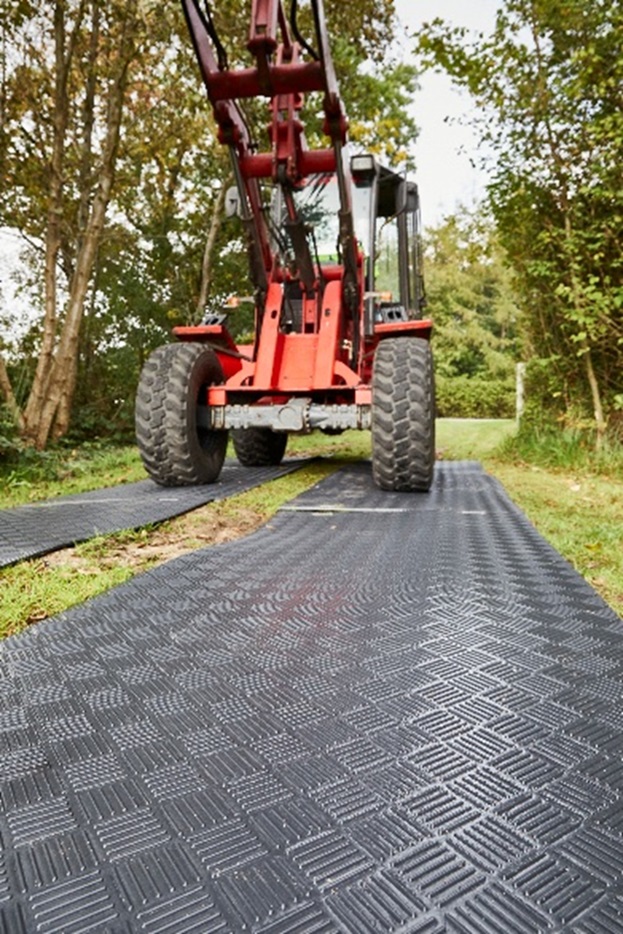
Documented data ensures the quality of recycled plastic
With the results in hand, Letbek can now take concrete steps to improve production quality and impose stricter requirements on its suppliers. Based on the findings, Letbek now requires that plastic for ground protection mats must contain no more than 5% PP.
This not only helps Letbek prevent complaints, but it also ensures that valuable recycled plastic is actually used rather than wasted due to hidden material issues.
“Our goal is to utilise as much recycled plastic as possible – without compromising on quality. Otherwise, we’re just creating new waste,” says Louise Aagaard Jensen.
If there are undesirable variations in material composition, Letbek can resolve it by blending different plastic batches to ensure the overall PP content stays below 5%. This way, they can continue using recycled plastic and minimise resource waste.
Material analysis is changing practice in recycled plastics
Letbek’s experience highlights a key learning for the plastics industry: even in low-spec products like ground protection mats, material analysis can be essential for success.
“It’s well known that recycled PP content can make products too brittle. But very few have data showing where the limit is. Now we do – and that makes a big difference,” says Louise Aagaard Jensen.
In the past, the PE–PP ratio was often overlooked, especially in products considered to have “low technical demands”.
“We haven’t had a single report of cracked mats since starting the project,” concludes Louise Aagaard Jensen from Letbek.
Related content
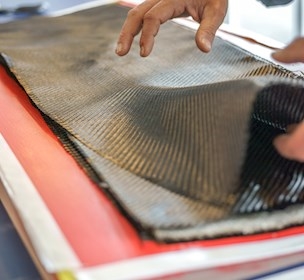
Test and analysis of plastics and composites
/Service
Ensure optimal material selection and design when working with polymers and composites.
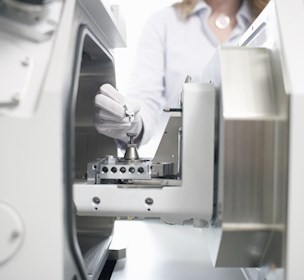
Surface characterisation laboratory
/Facility
Advanced equipment for surface characterization and analysis - including 3D, microscopy and X-ray.
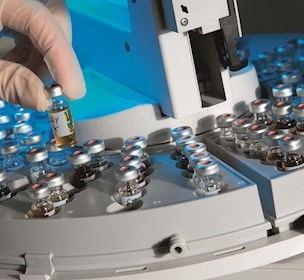
Chemical analysis laboratory
/Facility
In our chemical analysis laboratory, we perform characterisation of all types of substances.