Phased array ultrasonic inspection (PAUT) of storage tank on the CHP Skærbæk Power Station
Phased array ultrasonic testing has been used to inspect the k-weld of a hot water storage tank on Ørsted’s (formerly DONG) CHP Skærbæk Power Station. The inspection of the k-weld did not reveal any failures or defects.
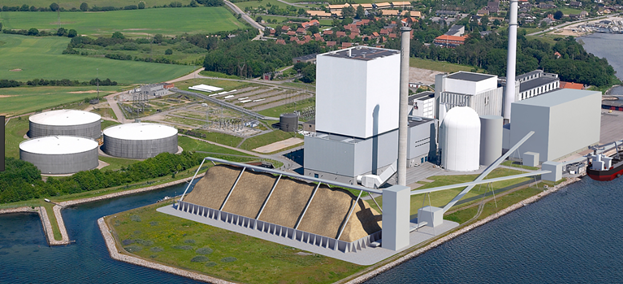
New ultrasonic methods provide new inspection options
At the CHP Skærbæk Power Station the hot water storage tank continuously leads hot water out to the district heating customers in the Triangle Region in Denmark. The tank circumference is 90 metres, the height is 50 metres, and it contains roughly around 30.000 m3 of water.
Every eight years, the k-weld must be inspected for potential failures and defects due to operation. The k-weld is an important part of the tank, as it ”unites” the bottom plate and the tank wall making sure there are no leaks. The tank was built and welded at a time where non-destructive testing was at a lower technological level compared to today.
First attempt with phased array ultrasonic inspection of storage tank
The inspection of the storage tank k-weld was a part of a larger tender from CHP Skærbæk Power Station, which FORCE Technology was rewarded.
On similar tanks, the k-weld has previously been inspected with traditional automated ultrasonic equipment, where a magnetic wheel scanner, equipped with two probes, scan the weld in a meander pattern to cover it in the circumferential direction of the tank.
Furthermore, it was necessary to perform multiple test on the circumferential direction of the tank too compile a complete rapport on the weld condition. This was a very time-consuming process.
Access to the inspection area has also a great influence on the choice of inspection method. As the bottom plate of the tank at CHP Skærbæk Power Station is bolted to a shell, the ultrasonic probe can’t reach the edge of the k-weld.
Therefore, FORCE Technology suggested an alternative inspection method based on automated phased array ultrasonic testing. This method only requires one probe, which, kept in the same position, can cover the entire weld in the circumferential direction of the tank – in spite of the bolts and the limited access to the weld.
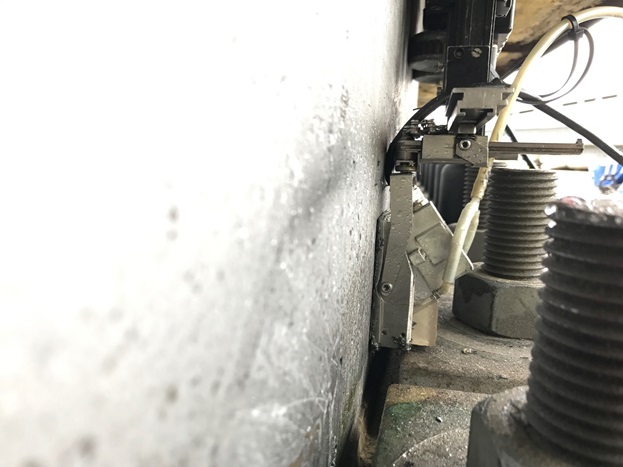
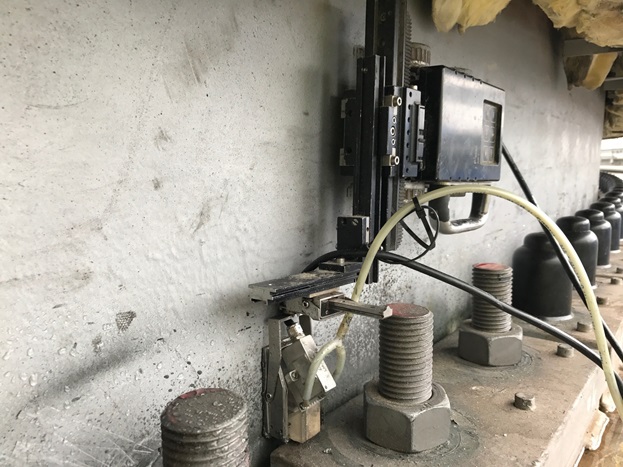
A fast method providing lots of data and safety
From this perspective phased array ultrasonic testing is an interesting technology, which can reduce the inspection time and ease the inspection of welds with limited access.
At CHPs and in the industry in general, inspection time is an important factor. The less time spent on inspection, the sooner the data will be ready for evaluation, and the sooner it is possible to assess what improvements and other measures that might need to be done. Reducing the inspection time with even 1 hour will result in significant savings.
Although phased array ultrasonic testing can minimize the inspection time, this does not affect the quality of the images and the data collected. Phased array ultrasonic testing as inspection method provides more detailed and long lasting images and data of the weld condition. These images and data can be used in the future maintenance work on the tank making it possible to assess, whether there is a development in the size of indications previously found.
The k-weld inspection did not find any non-acceptable indications that could pose a threat to the future operation of the hot water storage tank. The data and images that Ørsted’s CHP Skærbæk Power Station got from the inspection with phased array will provide a standard of comparison for future inspections of the k-weld.
Phased array ultrasonic testing can also be used on other inspection jobs at CHPs and in industries in general. The reason for this is the speed and the amount and quality of data that are stored and can be reviewed again for areas of doubt and for comparison regarding future inspections.
However, as for every other kind of inspection it’s also for phased array ultrasonic testing as inspection method important to specify what needs to be inspected and for what reason. By these means, this can be central for the subsequently evaluation of images and data.
Enhance your knowledge with courses in advanced ultrasonic testing
Would you like to enhance your knowledge within advanced ultrasonic testing and be able to fulfill the industries requirements to a modern and qualified NDT inspector? Join one of our courses in advanced ultrasonic testing.
Since companies often have unique demands and requirements, we also prepare and supply tailored and customer-specific courses - suited to match your purpose and level of experience.